A team of researchers recently published a paper in the journal Nature Communications that reviewed the fabrication of microrobots using three-dimensional (3D) printing methods and their applications.
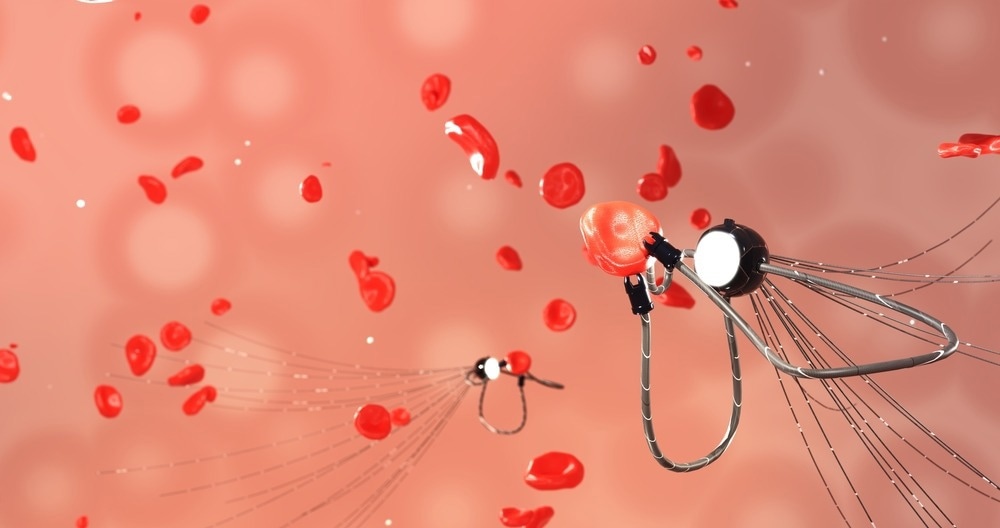
Study: 3D-printed microrobots from design to translation. Image Credit: Siwakorn TH/Shutterstock.com
Background
Microrobots have gained significant attention among the scientific community owing to their exceptional abilities to execute tasks in hard-to-reach sites within the human body. These robots can be maneuvered in a swarm or individually and actuated precisely for imaging, surgery, sampling, and drug delivery applications. Microrobots can also be used in environmental applications, such as water treatment.
Recent developments in 3D printers have allowed high-resolution microrobot fabrication with a shorter design-production turnaround time. Specifically, these printers are suitable for users lacking extensive micro-manufacturing skills.
In this study, the authors reviewed the latest applications of 3D-printed microrobots, briefly discussed the microrobot actuation methods, and looked at the 3D-printing techniques and materials used for microrobot fabrication. The authors also discussed the advantages of integrating microrobots with smart materials and implementing physical intelligence (PI) and artificial intelligence (AI) in these robots.
Materials
Polymers, including natural proteins, photo-cross-linkable hydrogels, and photopolymers are used extensively for microrobot fabrication using 3D printing techniques. Among them, photopolymers are more beneficial as they can be printed into 3D objects using a laser through a photochemical reaction method.
Photopolymer materials such as additives, monomers, and photoinitiators are often used in laser printing. SU-8, an epoxy-based negative photoresist, and IP-series photoresists, a group of standard photopolymerizable, are commonly used for high-resolution 3D microfabrication.
Hexahedral multifunctional microrobots, magnetic microrobots, and swimming microrobots fabricated using SU-8 photoresist are used for targeted cell delivery, delivery and transportation of targeted cells, and targeted cargo transport, respectively.
Magnetic helical microswimmers, optically-controlled microrobots, and helical swimming microrobots fabricated using IP-L780 are used for targeted gene delivery, microsurgery, and single-cell, targeted, and remotely-guided drug delivery, respectively.
Magnetic microrobots, microswimmers, and magnetic micrometers fabricated using IP-Dip are utilized for targeted transplantation of stem cells, single-particle manipulation, and targeted discharge, transportation, and trapping of motile sperms, respectively.
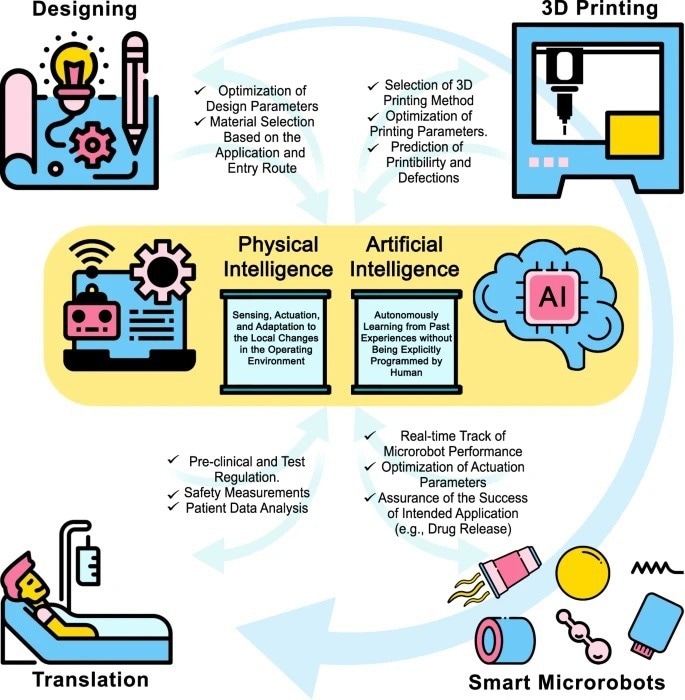
A schematic view of a microrobot from bench to bedside. The design and material-selection process can be assisted by AI and PI to design an application-specific device. AI can also improve the 3D printing process by optimizing printing parameters to reduce printing defects. In the application phase, AI can help clinicians to track microrobots and enhance maneuverability by tuning actuation parameters to ensure proper functionality. On the other hand, PI enables microrobots to sense different stimuli in their environment and respond to those stimuli independently (e.g., drug release at a particular pH level in the target site). In order to translate proof-of-concept microrobots to clinical medical devices, new microrobots must undergo standard tests to ensure safety for short- and long-term uses in the human body. However, these tests require cumbersome and costly procedures, which delays the rapid translation of microrobots. Thus, besides developing new materials, fabrication methods, and actuation modalities, more straightforward test procedures should be proposed to truncate the current test process while maintaining safety factors. Some elements in Fig. 1 have been designed using resources from Flaticon.com. Image Credit: Dabbagh, S.R. et al., Nature
3D Printing-based Microrobot Fabrication Methods
3D printing methods commonly used for microrobot fabrication include fused deposition modeling (FDM), inkjet 3D printing, microextrusion 3D printing, selective laser sintering (SLS), laser-induced forward transfer (LIFT), direct laser writing (DLW), continuous liquid interface production (CLIP), digital light processing (DLP), and stereolithography (SLA).
SLA
Microrobots with 10 μm resolution are 3D printed using the SLA technique. Resins, including hybrid polymer, photo-activated monomer, DC 500, DC100, DM 220, and GM-08 are used in the SLA-based fabrication process.
Good precision and surface quality, high quality, and fine spatial resolution are the key advantages of using the SLA technique for microrobot fabrication. However, slow printing rate, high cost, and limited choice of material are the major limitations of the SLA technique.
DLP
Microrobots with 25-100 μm resolution can be fabricated using the DLP technique. Materials used in this 3D printing technique include super WAX, super CAST, acrylate-based resin, epoxides, and diamond microparticles.
Low required initial vat volume, faster printing and less influence of oxygen interference compared to SLA, low cost, and high printing accuracy are the major benefits of using the DLP technique. Poor mechanical properties of the printed structures are the main disadvantages of the technique.
CLIP
Microrobots with 75 μm resolution are printed using the CLIP technique. Cyanate ester, elastomeric polyurethane, flexible polyurethane, rigid polyurethane, and acrylates are used to fabricate microrobots in this method. CLIP technique has a higher production speed compared to DLP. The method requires resins with a low viscosity, which is a significant disadvantage.
DLW
Two- or multi-photon polymerization (TPP/MPP) technique can be used to fabricate microrobots with 100 nm resolution using acrylates. High spatial resolution is the key advantage of this process, while low printing speed and limited choice are the major limitations of this technique.
LIFT
Microrobots with 10 μm resolution are printed using the LIFT method. Metal complexes and hydrogel materials are typically used in the LIFT-based microrobot fabrication process.
Extensive material choice and fine printing resolution are the major advantages of the LIFT technique. This technique can also print inks with different viscosities and embedded particles. The slow fabrication process is the most significant disadvantage of this method.
Other 3D Printing Methods
Microrobots with 50–200 μm resolution can be fabricated using SLS, inkjet 3D printing, FDM, and microextrusion 3D printing. Among them, SLS and FDM have several limitations regarding microrobot fabrication compared to inkjet 3D printing and microextrusion 3D printing.
Applications of 3D-printed Microrobots
Environmental Applications
Water Treatment
Microrobots can eliminate and detect heavy metal ions, detoxify dangerous microorganisms, decontaminate organic pollutions, and absorb oil droplets during water treatment. Moreover, sunlight-actuated decontaminator microrobots can be distributed in surface water resources without requiring an external power source.
However, recycling and recollecting microrobots is difficult after they are distributed in large water reservoirs. Additionally, microrobots cannot travel long distances, often in the range of meters, using the current actuation methods.
Biomedical Applications
Sensors and Actuators
Microrobots can facilitate precise and quick manipulation, can be integrated with several sensing mechanisms, and operate using off-board and on-board actuation methods. However, the use of metallic parts in microrobots can potentially lead to toxicity in vivo and in vitro. Microrobots can also provide inaccurate measurements as they are susceptible to small changes in environmental parameters.
Drug Delivery
Microrobots can release drugs at specific sites with particular environmental properties or upon receiving external stimuli, such as acoustic or magnetic pulse, and selectively/controllably degrade after drug delivery.
Moreover, microrobot swarms are suitable for large-scale drug delivery. However, partial degradation of microrobots and inadequate drug delivery due to actuation method limitations are the major disadvantages of using microrobots in drug delivery.
Particle Monitoring/Tracking and Imaging
Microrobots can be used for in vivo real-time tracking and imaging. Coloring microrobots are used to improve monitoring accuracy without requiring complex functionalization steps. However, microrobots can be displayed as a cloud due to limited spatial resolution. Moreover, the particle tracking ability of microrobots can be limited depending on the imaging system's operational range.
Tissue regeneration and surgical procedures are other biomedical applications where microrobots play a significant role.
Actuation Methods
In vivo and in vitro actuation of microrobots is considerably challenging due to the limitations associated with their submillimeter scale. The propelling mechanism must generate sufficient force to overcome the viscous forces without compromising the biocompatibility and structural integrity of microrobots.
Actuation methods are classified as off-board and on-board methods. Self-actuated microrobots/microrobots with on-board actuation use their preloaded biological or chemical power sources for propulsion when they react with specific substances in their operating environment without requiring any external actuation.
Microorganism-based actuation and chemical actuation are examples of on-board actuation. Off-board actuation methods use external force fields, such as electric, light-based, ultrasound, acoustic, and/or magnetic propulsion, to drive the microrobots in fluidic environments.
Magnetic actuation is used most extensively, specifically in biomedical applications, owing to its acceptable penetration depth in the tissue, easy operation, precise control, and availability. However, light-based actuation is considered more suitable due to limited penetration in the tissue.
Translation Challenges
The performance and production of microrobots must be considered and optimized to efficiently translate them from laboratory to in vivo clinical setups. These aspects include the selection of proper microrobot design based on application-specific design strategy, biocompatible and biodegradable materials, proper manufacturing method, effective actuation and control methods, compatibility with existing medical imaging approaches, and ability to execute the intended medical tasks.
Conclusion
To summarize, microrobots have demonstrated significant potential in both environmental and biomedical applications. However, more research is required to develop faster 3D printing methods for microrobot fabrication without compromising the printing resolution. Moreover, a comprehensive test procedure must be designed for microrobots to reduce the number of current test methods while ensuring safety.
Future Outlook
Recent advancements in 3D printing have enabled the incorporation of several smart materials in microrobots. Layers of different smart materials, such as nanomaterial-based composites, shape-memory alloys, biomaterials, and stimuli-responsive polymers that demonstrate self-healing, self-actuating, self-sensing, and shape-changing and/or signal generation abilities in response to external stimuli can be utilized in microrobots to realize behaviors such as healing, sensing, selective deformation, adaptation, degradation, propulsion, heat generation, and cooling.
The integration of AI approaches, such as deep learning and machine learning, into the microrobot 3D printing process can enable researchers to realize optimal microrobot performance while optimizing the required material and printing time. PI is another method to improve the microrobot performance in response to changes in the local environment. This method can enable microrobots to learn, act, control, interpret, and sense autonomously and continuously.
Disclaimer: The views expressed here are those of the author expressed in their private capacity and do not necessarily represent the views of AZoM.com Limited T/A AZoNetwork the owner and operator of this website. This disclaimer forms part of the Terms and conditions of use of this website.
Source:
Dabbagh, S.R., Sarabi, M.R., Birtek, M.T. et al. 3D-printed microrobots from design to translation. Nature Communications 2022. https://www.nature.com/articles/s41467-022-33409-3