In a paper recently published in the journal Japan Architectural Review, researchers used computational fluid dynamics (CFD) to evaluate a fume hood’s capture performance and the factors influencing the airflow rate of the exhaust, the heat source, and the experimental instruments and workers present.
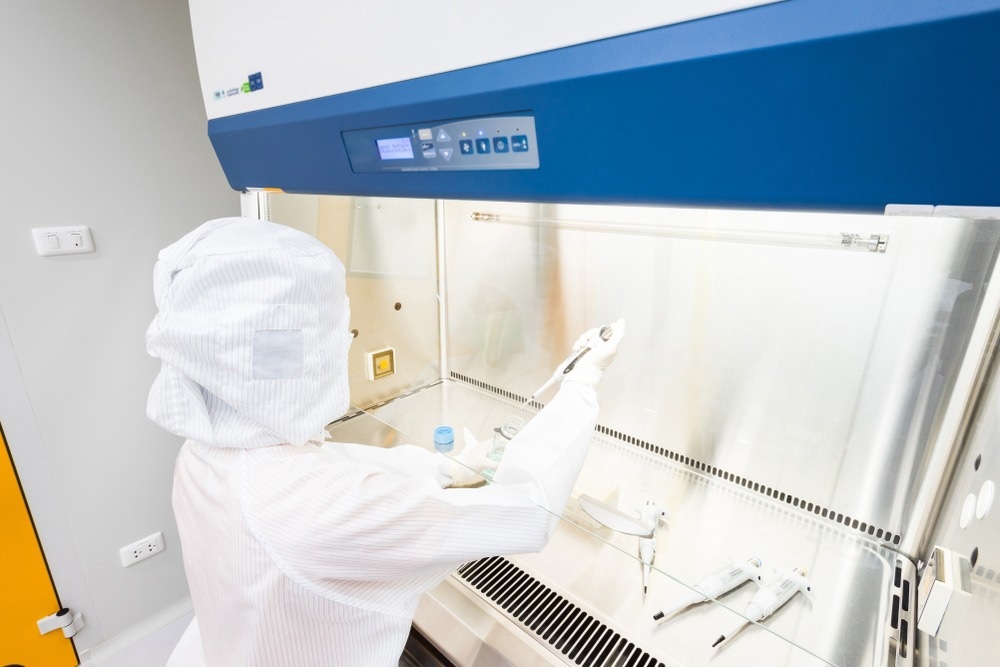
Study: Impact of heat generation and use of experimental instruments in a fume hood on pollutant capture efficiency. Image Credit: warut pothikit/Shutterstock.com
Background
Mixed-mode ventilation systems are typically implemented in interior environments, such as businesses and homes, with the intention of reducing indoor pollutant emissions. In university laboratories where dangerous chemical substances are handled, fume hoods are frequently constructed. Chemical containment and leak prevention are the primary functions of the fume hood.

Analysis model for the fume hood with the CSP. Image Credit: Muta, R., Ito, K., Jpn Archit Rev
The mean air velocity at the opening surface is used to assess the fume hood's performance. However, several earlier investigations have shown that this parameter is insufficient on its own to assess fume hood performance. Studies have suggested that it is crucial to assess the opening surface velocity both in an idealized environment and in real-life situations while taking various significant aspects into consideration.
About the Study
In this study, the team quantitatively assessed the fume hood's ability to capture pollutants with the installation of heat generation and experimental instruments within the fume hood under standard working conditions. For numerical analysis, a digital twin model of a lab-installed conventional fume hood was developed. The digital twin concept also included a thorough computer-simulated person (CSP) to replicate the position of an individual working before the fume hood.
For the investigation of scalar transport and flow, ANSYS Fluent 2022 R2 was utilized as a commercial CFD program. The flow field's turbulence was modeled using the SST k–ω model. By adjusting the airflow rate of the exhaust, the air velocity of the opening surface was established at three different levels. Furthermore, to verify the fume hood's ability to effectively capture contaminants, the team examined the scalar concentration distributions. The analysis models were discretized, and ANSYS meshing equipped with a polyhedral mesh element was used to mesh the models. In order to achieve the accurate value of the flow and scalar distributions, numerical and boundary conditions, grid design, and other criteria were verified.
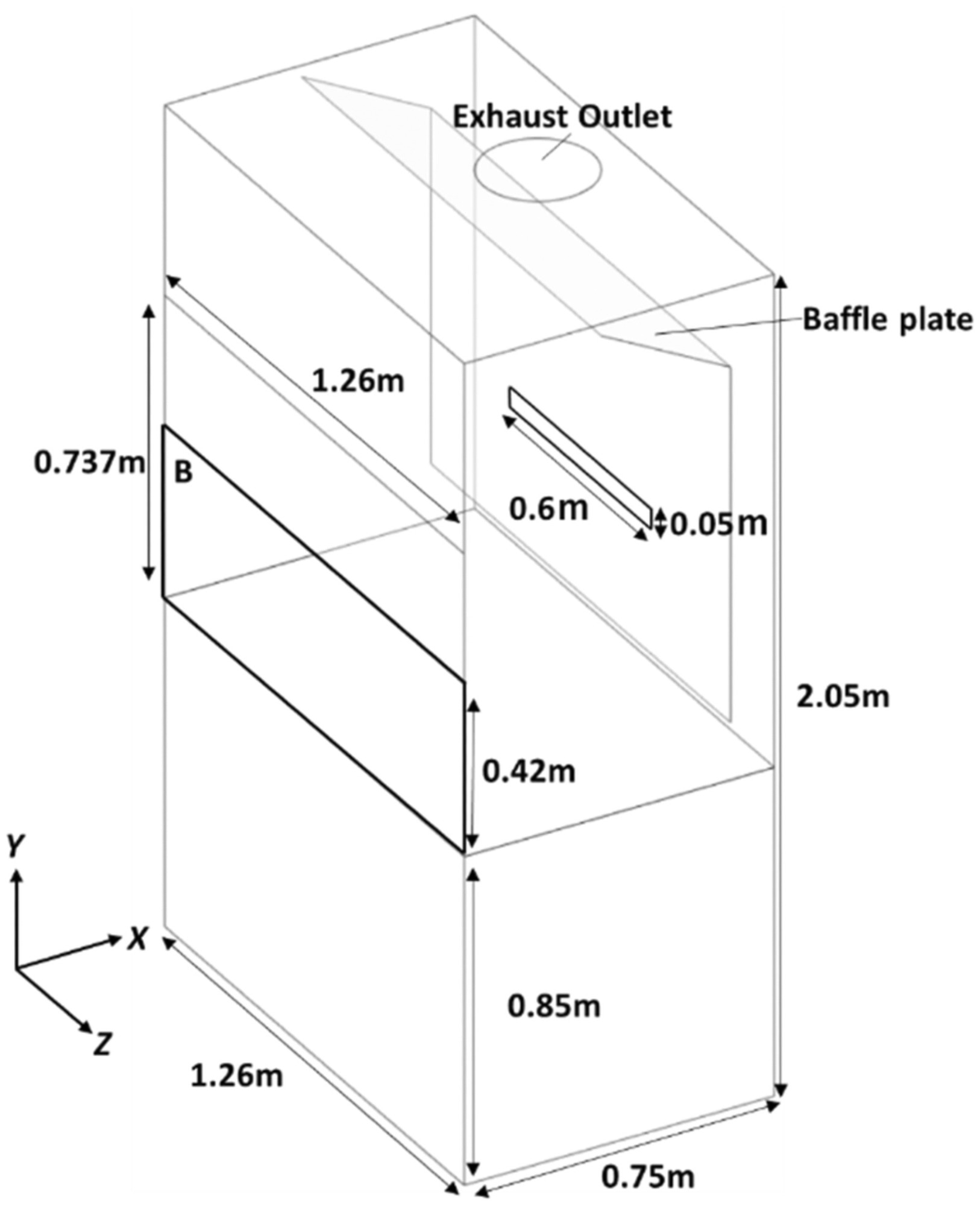
Fume hood model. Image Credit: Muta, R., Ito, K., Jpn Archit Rev
Observations
The team discovered that the experimental device, which interfered with airflow, had an impact on the fume hood's ability to trap particles. The CSP present in front of the heat source and the fume hood had no discernible impact on the fume hood performance when the velocity of the opening surface was at 0.5 m/s. Regardless of how the exhaust airflow rate was set, the obstruction close to the opening surface had a considerable impact on the distribution of opening surface velocity and the creation of the circular flow. The team noted that there was a risk of leakage when the workbench present in the fume hood was close to a high-concentration area.
Moreover, the findings of the concentration distribution analysis showed that the method utilized to assemble space under the obstruction was inefficient in the case of ventilation. The lower half of the fume hood's ventilation efficiency was enhanced by the distance between the opening surface and the obstruction. However, in a usage scenario wherein the velocity of the opening surface was set at 0.5 ms-1, the pollutants behind the obstruction were effectively discharged.
The local area's ventilation efficiency was measured by analyzing the circumstances for consistent pollutant formation in the local purging flow rate (L-PFR) of the lower portion of the fume hood. The L-PFR was adjusted for the airflow rate of the exhaust. In all the assessed circumstances, the L-PFR was greater than 1.0. As a result, even with the obstruction, the air input into the fume hood was effectively diluted before purging the contaminants from the bottom area. By moving the obstruction to almost 0.1 m away from the opening surface, the ventilation efficiency could be significantly increased.
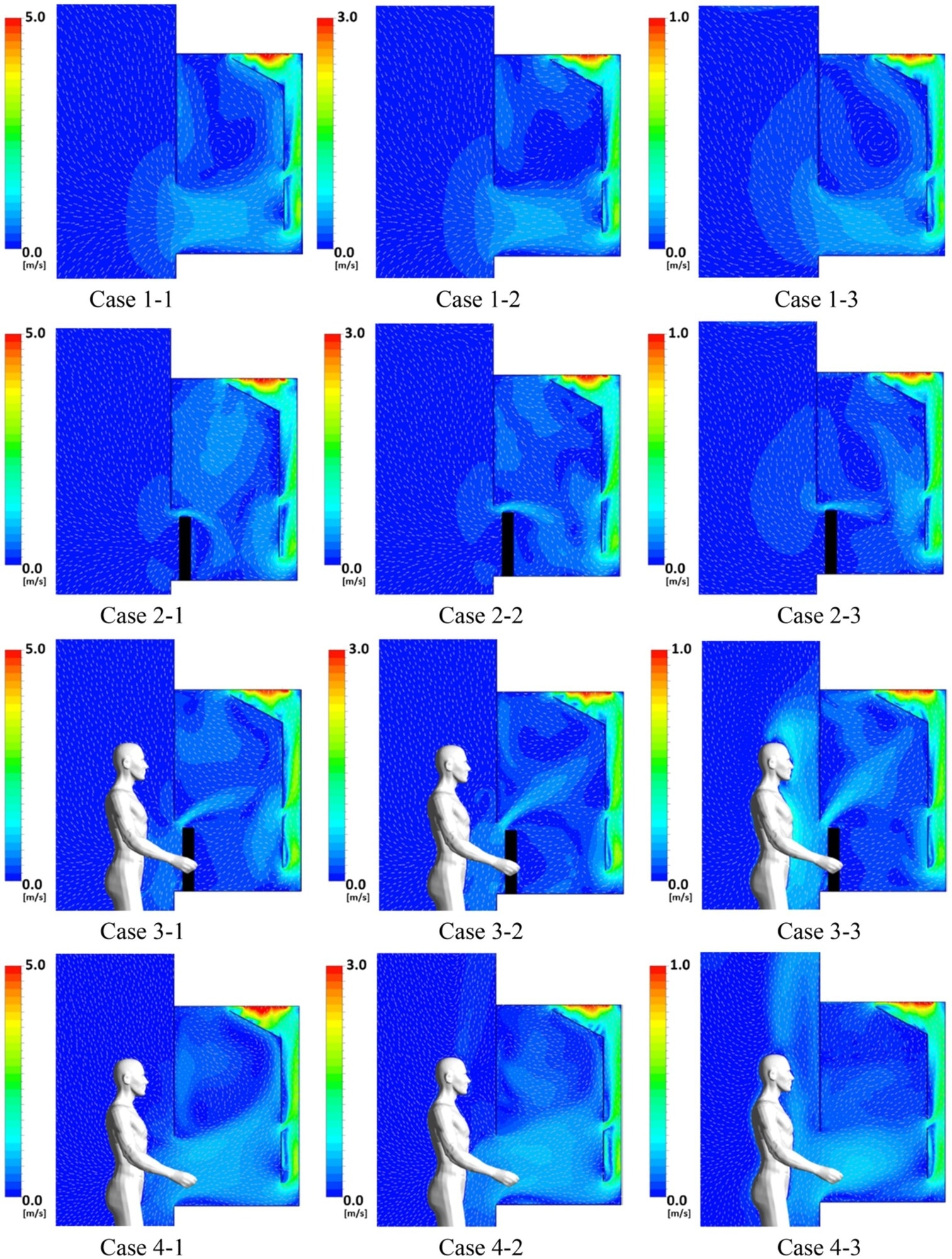
Velocity distribution around the fume hood (Z = 1.63 m). Image Credit: Muta, R., Ito, K., Jpn Archit Rev
Conclusions
To summarize, the researchers examined the pollutant-capturing capabilities of the fume hood along with the corresponding CFD calculations of the scalar and flow concentration distributions. Irrespective of the velocity of the exhaust airflow, it was found that an obstruction placed close to the fume hood's opening surface had an impact on the development of circular flow within the fume hood.
Furthermore, the team found no remarkable difference between a scenario having only an obstruction and a situation having an obstruction along with a CSP. The updraft observed near the CSP induced by metabolic heat, however, disrupted the airflow in the fume hood when the airflow rate of the exhaust was decreased. When the velocity of the opening surface reached 0.1 ms-1, contamination leakage was observed. According to the authors, it is thus useful to position the experimental equipment distanced from the opening surface in order to retain the capture performance in real-life use conditions.
Further Reading
Muta, R., Ito, K., (2022) Impact of heat generation and use of experimental instruments in a fume hood on pollutant capture efficiency, Jpn Archit Rev, DOI: https://doi.org/10.1002/2475-8876.12300
Disclaimer: The views expressed here are those of the author expressed in their private capacity and do not necessarily represent the views of AZoM.com Limited T/A AZoNetwork the owner and operator of this website. This disclaimer forms part of the Terms and conditions of use of this website.