The development of projection micro stereolithography (PμSL), a powerful three-dimensional (3D) printing technique, has allowed the production of customized 3D microlattices with feature sizes as small as a few microns. PμSL can produce polymer structures with micron-scale high resolution at high printing speeds.
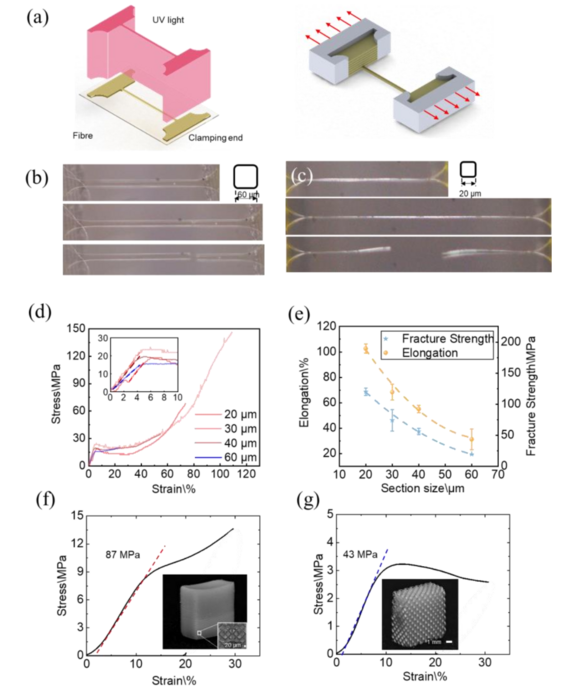
Image Credit: Wenqiang Zhang, Haitao Ye, Xiaobin Feng, Wenzhao Zhou, Ke Cao, Maoyuan Li, Sufeng Fan and Yang Lu.
The mechanical characteristics of as-printed polymers, particularly when the feature sizes step into the micron/sub-micron level, were not systematically studied at the relevant length scales, which limited its ability to predict performance with accuracy in micro/nanolattice and other metamaterial applications.
The City University of Hong Kong’s Prof. Yang Lu shows that projection micro-stereolithography (PμSL)-printed microfibers can become stronger and noticeably more ductile with reduced size ranging from 20 micrometers to 60 micrometers, showing an obvious size-dependent mechanical behavior, in which the size decreases to 20 micrometers with a fracture strain up to ~100% and fracture strength up to ~100 MPa.
This size effect enables the fabrication of microlattice metamaterials with desired/tunable mechanical characteristics for a variety of structural and functional applications. It also allows the customization of the material strength and stiffness of PμSL-printed microlattices over a large range.
By taking into account the size effect of the PμSL-printed polymer, it is possible to create microlattices with various mechanical characteristics while maintaining the same topography and relative density.
The microlattice with struts of 20 micrometers has a measured modulus of ~87 MPa, which is almost twice as large as the lattice with struts measuring 60 μm (~43 MPa). After the lattices were produced, the strain caused an increase in the stress of the lattice with 20 micrometer struts.
The micro-sized struts’ strain-hardening phase may be to blame for this. A lattice with a diameter of 60 μm, however, displays the characteristic stress curves of brittle materials.
This discovery serves as a reminder to consider the polymer’s size while building microlattice metamaterials. The tailoring of the material strength and stiffness of microlattice units over a wide range is made possible by the size-dependent mechanical behavior of PμSL-printed acrylate-based resin structures. This enables the reasoned fabrication of microlattice scaffolds with desired/programmable mechanical properties for the creation of new micro/nano-lattice mechanical metamaterials.
Nowadays, vat photopolymerization 3D printing technologies, such as PµSL, can provide an excellent combination of ultrahigh printing resolution and large printing size, paving the paths for geometrically complex components with well-defined hierarchical structures for structural and functional metamaterials.
Yang Lu, Professor, Department of Mechanical Engineering, City University of Hong Kong
Prof. Lu added, “A deep understanding of the mechanical properties of PμSL-printed polymer at small length scales will accelerate the development of advanced mechanical metamaterials such as micro/nanolattice materials with unprecedent performance.”
He concluded, “Size-dependent mechanical properties of materials have been always the central focus of my group’s research. It also inspires us to pay more attention to utilize such size effects for designing advanced mechanical metamaterials with critical features steps into micro/nanoscales.”
Journal Reference:
Zhang, W., et al. (2022) Tailoring mechanical properties of PμSL 3D-printed structures via size effect. International Journal of Extreme Manufacturing. doi:10.1088/2631-7990/ac93c2