It takes time, perfect materials, and a lot of expertise to build a high-quality string instrument, and the best ones can cost millions of dollars. Even average violins can cost hundreds of dollars, putting them out of reach for the majority of beginners and music classrooms.
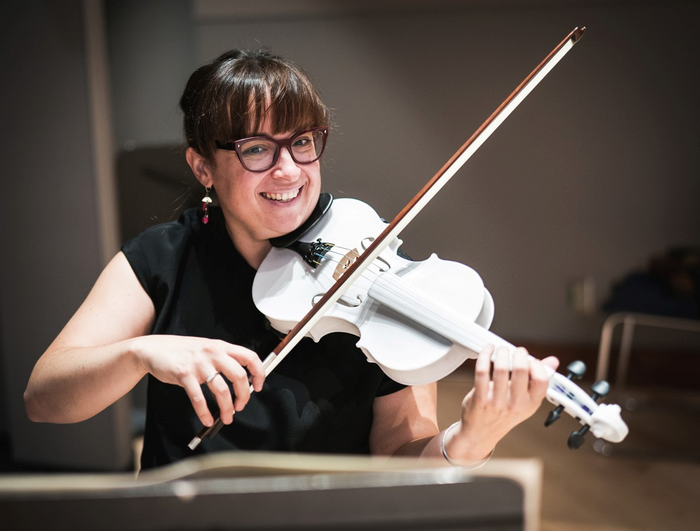
Mary-Elizabeth Brown rehearses Harry Stafylakis’ concerto “Singularity” on an early iteration of the 3D-printed violin. Image Credit: Shawn Peters.
One organization is attempting to address this by 3D printing low-cost, long-lasting violins for music students. Throughout the process, they investigated the aspects that contribute to the best violin sounds and conducted a concerto conducted specifically for 3D printed instruments.
In her talk, “Old meets new: 3D printing and the art of violin-making,” Mary-Elizabeth Brown, Director of the AVIVA Young Artists Program, explored the steps taken and the lessons learned. The presentation took place on December 6th, 2022, at 10:35 a.m. Eastern time in the Golden Eagle B room, as part of the 183rd Meeting of the Acoustical Society of America, which is held at the Grand Hyatt Nashville Hotel from December 5th to 9th.
The team’s inspiration roots in multiple places. Our goals were to explore the new sound world created by using new materials, to leverage the new technology being used in other disciplines, and to make music education sustainable and accessible through the printing of more durable instruments.
Mary-Elizabeth Brown, Director, AVIVA Young Artists Program
The 3D-printed violin was made in two sections. Similar to a typical acoustic violin, the violin’s body is built of plastic polymer and is intended to produce a resonant tone. The neck and fingerboard are printed in smooth ABS plastic to be pleasant in the musician’s hands. As a result, the violin has a deeper, more mellow sound than traditional instruments.
The next step is to explore design modifications as well as efforts to lower the costs of production while making such instruments more widely available, especially in the realm of education.
Mary-Elizabeth Brown, Director, AVIVA Young Artists Program