Feb 26 2001
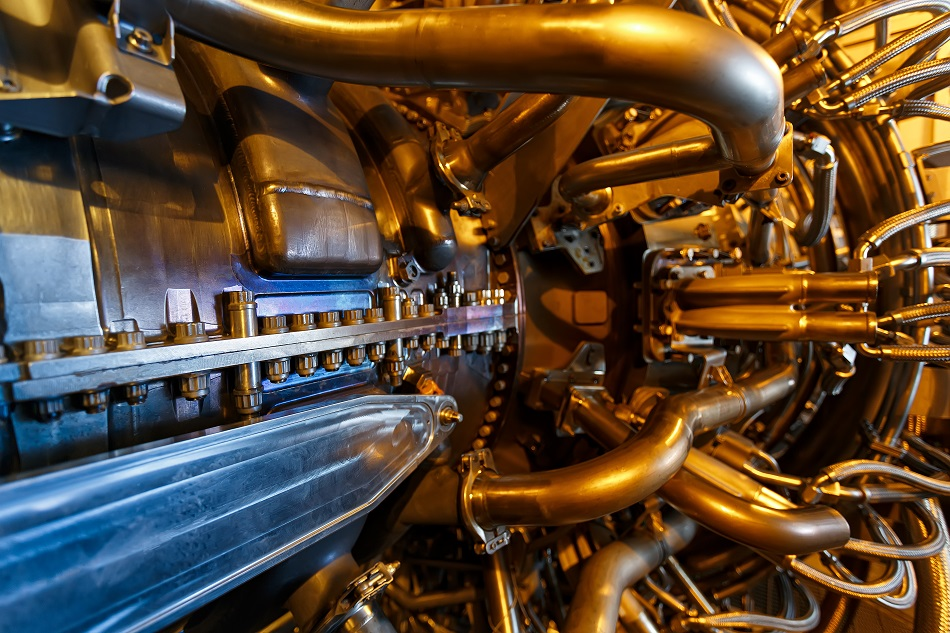
Image Credit: Aleksandr Grechanyuk/Shutterstock.com
Developments in advanced materials over the years have contributed to the spectacular progress in the thrust-to-weight ratio of the aero gas turbine. This has been achieved mainly through the substitution of titanium and nickel alloys for steel. Aluminum has virtually disappeared from the aero engine, and future projections regarding this show that composites of various types of materials are possible. The aero-engine designer requires a much wider range of materials than the airframe designer because the temperature range is large, whereas a civil airframe, even that of Concorde, lies entirely within the capability of aluminum. Materials also supply the enabling technology for equally significant improvements in performance and reliability.
The RB211 and Trent engine families provide good examples of the link between material capabilities and engine performance. Civil engine programs are now becoming the drivers for materials development, replacing the military programs that were the leaders at the beginning of the gas turbine era. The earlier approach of technology transfer from military to civil is tending to switch direction.
The turbine entry temperatures of modern civil engines are now approaching those of the latest military combat engines, and the longer operational lives expected by airlines place greater demands on materials technology.
Design Parameters
The key design parameters of gas turbine engines are fan airflow—which is related directly to thrust, particularly at take-off—and the pressure ratio and flow size of the core, which determine the fuel consumption and climb thrust for a given engine size. Take-off thrust is determined by the airflow which is directly related to fan diameter. Increasing the physical size of the material is a relevant consideration because of its effect on low weight and structural stiffness.
Core engine size is equally important because the power output to drive the fan is determined by core mass flow and combustor temperature rise. Component development provides increased temperature capability, but the physical size of the compressor is not easily changed and mass flow through the core can only be increased by supercharging to higher overall pressure ratios.
Aerospace components such as the fan blade, the rear of the high-pressure compressor, and the high-pressure turbine would show how materials are responding to the required performance and design parameters in operation. They also highlight the potential of advanced materials such as titanium and nickel alloys, plus the possibilities for composite materials, concerning increased and efficient performance. In the production of larger diameter, low weight fan blades, the contribution of advanced materials is vital, not only for density but also through advanced fabrication methods. New materials must also withstand the demands for increasing compressor delivery temperature and turbine entry temperature. Specific fuel consumption depends on thermal as well as propulsive efficiency; meanwhile, thermal efficiency depends on the maximum temperature of the cycle, as with any heat engine. Maximizing efficiency within the design is important for fuel consumption.
Summary
- Civil aero-engine performance development has depended heavily on advances in materials, not for their properties but also in their manufacturing and processing.
- In all phases activity, simultaneous consideration of service duty and manufacturing process is vital. This demands the closest co-operation between the engine manufacturer and suppliers.
- Composite materials—each appropriate to its operating temperature environment—will become increasingly important, but the pace of their introduction will depend on success in achieving low-cost manufacture and cost-effective exploitation.
- Researches are currently exploring the utility of new products and materials at lower costs.
This article was updated on 29th January, 2020.