Feb 26 2001
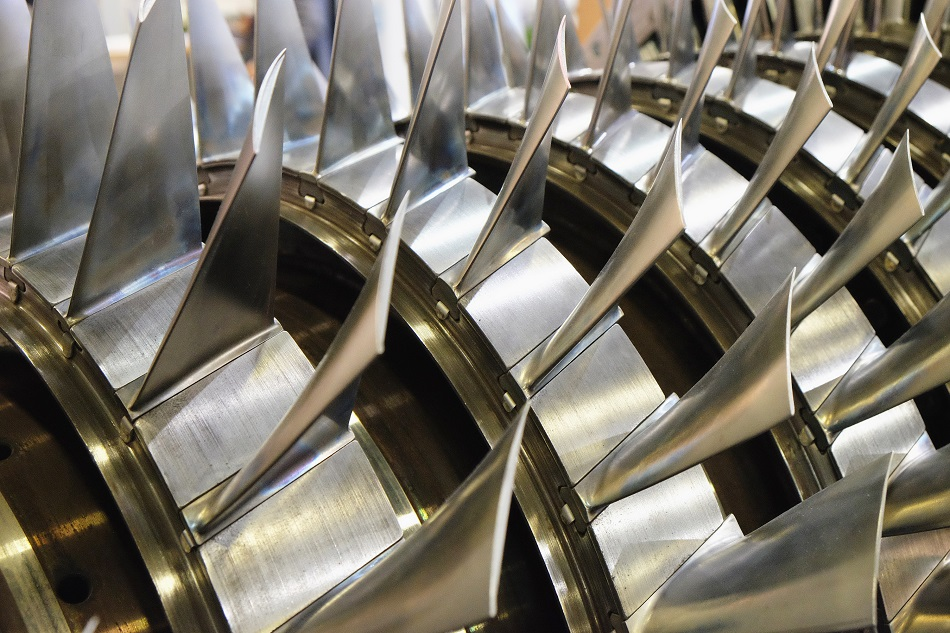
Image Credit: Marina Pousheva/Shutterstock.com
For many years, fan blades for high bypass aero-engines were manufactured from solid titanium alloy forgings and were designed with mid-pan snubbers to control vibration. However, snubbers impeded airflow and reduced aerodynamic efficiency, yielding to high fuel consumption. Modern fan blade designs have removed the snubber to provide a more efficient aerofoil.
This new mechanism simultaneously increased the blade chord for mechanical stability, reducing the number of blades by approximately one third. This has been achieved at reduced weight with a hollow construction and an internal core.
Blade Materials
For both snubber and wide chord blades, a conventional fine grain titanium alloy—which is 6% aluminum and 4% vanadium (Ti6Al4V)—is used. This combination is simple in terms of chemistry, with the aluminum offering strength at low density, and the vanadium facilitating an easier process of hot working a material.
This fine-grain titanium alloy is used for discs and compressor blades up to about 350 °C, but excellent superplastic forming and solid-state diffusion bonding capabilities make it particularly suitable for the wide chord blade.
The low-density core for the hollow design is an integral part of the structure. The two external skins are separated by either a honeycomb filler or a superplastically-formed corrugation, which carries a share of the centrifugal load. Both panel-to-panel and core-to-panel joints must achieve parent material properties to withstand the effects of foreign body impact and fatigue.
For first-generation designs, the joints are made through a transient liquid phase diffusion bonding process, whereas second-generation designs employ solid-state diffusion bonding in association with the superplastic forming of the assembly. The cavity of the bonded construction is inflated at elevated temperatures between contoured metal dyes using inert gas to expand the core and simultaneously develop the blade's external aerodynamic profile.
There is unreliability, however, in these types of blades. Technological endeavors to reduce this limitation proved to be a major competitive advantage. It was only after ten years when an equivalent design appeared from a manufacturer other than Rolls Royce. This service record was the result of thorough development testing.
Fatigue testing in both low and high cycle modes was essential; groups of blades were repeatedly accelerated to their maximum speeds in vacuum to establish low cycle endurance, and high cycle fatigue was investigated on a static vibration rig up to the maximum stress levels likely to be encountered in service.
Technical Considerations
With a large forward-facing area, resistance to bird ingestion is required. Ingestion of several medium-size birds is demonstrated by running an engine at take-off power and requiring it to ingest four birds within one second. The engine should continue to deliver power, accelerating and decelerating for 30 minutes to simulate the likely operating procedure following a severe ingestion incident.
In the very unlikely event of a blade mechanical failure, the engine must be structurally sound and contain all the debris, even if the failure occurs at maximum power.
Containment in modern engines is achieved with aluminum or titanium casings through which the blade fragments can penetrate, to be caught in external windings of Kevlar.
As an indication of the benefits of materials development and design enhancements, engines incorporating the wide chord blade have fan modules that are approximately 24% lighter and an engine that is 7% lighter (typically the Trent 800 engine as used in the Boeing 777).
The Future of Gas Turbine Engines
There is evidence to show that carbon composite materials could resolve fan blade requirements in modern machinery. Currently, these materials limit the speeds that the blade can be designed, requiring a greater diameter for a given thrust. Researchers are continuously developing an integrative approach that will converge the material and the hollow design; this would lead to the satisfaction of airworthiness requirements that focus on creating titanium sheathing around a large part of the composite blade with some weight penalty. The composite can be considered as an alternative core to the titanium honeycomb or corrugation. Companies have also been studying the application of titanium-based metal matrix composites with selective reinforcement provided by silicon carbide monofilaments to control blade untwist.
This article was updated on 29th January, 2020.