Feb 26 2001
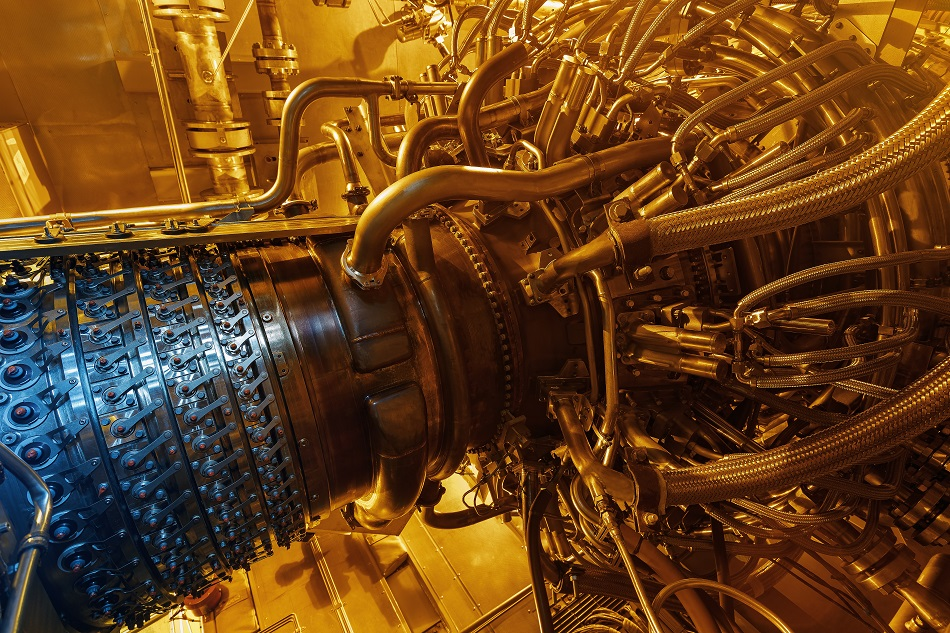
Image Credit: Aleksandr Grechanyuk/Shutterstock.com
The rear end of a high-pressure compressor in an aero-engine is in a temperature environment set by the overall pressure ratio chosen for the engine cycle. Since the 1950s, this temperature level has risen by about 300°C. Simultaneously, it was also discovered that titanium alloys could progressively tolerate temperatures of up to 630°C. Compressors could, therefore, be designed completely with titanium. Regardless, there is evidence demonstrating that in some countries, such as in the United States, nickel alloys are utilized when temperatures reach approximately 520°C, allowing a weight penalty in the procedure.
The development of IM1834 is a good example of a metallurgist's response to the needs of the designer. The requirements were intended for higher tensile and fatigue strength as well as enhanced creep performance. These were met by optimizing the structural balance between primary alpha content and the transformed beta phase in the titanium alloy.
Developments
Producing integrally bladed discs—also called blisks—is a natural setting wherein the blade attachment features are removed, resulting in significant weight and cost savings. For small engines, the most convenient manufacturing method is to machine both disc and aerofoils from a single forging; however, a common disadvantage of this method is that the material strength of the aerofoil may be reduced. Paying more attention to the forging method and to the manufacturing processes could help mitigate this issue.
Metal Matrix Composites
Titanium metal matrix composites can be applied to both aerofoils and discs. Using silicon carbide fiber offers about 50% more strength and twice the stiffness of the high-temperature titanium alloys, combined with reduced density. Consequently, an aerofoil design will benefit from the increased stiffness of selective reinforcement. This will allow users the ability to control vibration modes and blade untwist. This technique could be utilized further using integrally bladed rings which are expected to provide a 70% weight saving relative to a conventional geometry in titanium.
Intermetallics
Intermetallics are another material interest in gas turbine engines. Most intermetallic compounds are brittle at room temperature and could likely be applied in small components such as static and rotating compressor aerofoils. The advantages over titanium include higher specific strength and stiffness, as well as improved temperature and fire resistance. The use of these materials could extend to more critical components; one possible application is an alternative matrix to the titanium alloy in a metal matrix composite, although this would require alternative fibers to minimize any thermal expansion mismatch.
The Future
Current studies on high-pressure compressors have focused on the use of intermetallics in a variety of applications. Currently, it was found that titanium aluminides from the intermetallics class provide excellent elevated temperatures, high stiffness, and good temperature properties. Operating temperatures of about 800°C have been tested with high-pressure compressors, and intermetallics offered a very attractive weight saving of around 50% compared with nickel-based alloys.
This article was updated on 29th January, 2020.