Cranfield University’s wholly owned subsidiary, Cranfield Aerospace (CAe) has more than four decades of experience in aviation safety solutions.
CAe innovates and de-risks product solutions to address some of the most complex problems in the aerospace sector. The company offers a wide range of services for both manned and unmanned airborne solutions.
CAe recently contacted Ogle Models and Prototypes to design and build simulated host ejection seats with motion cueing technology for its jet pilot training program. Ogle Models and Prototypes subsequently supplied the replicated seats which were fitted with motion cueing modules from CAe. The entire process, from design to delivery, was carried out on time and with high quality standards.
Motion Cueing Simulator Seats
CAe was searching for a suitable supplier to design and develop host ejection seats (Figure 1) and finally opted for Ogle Models and Prototypes. Ogle Models has six decades of experience in prototyping, designing and model-building and was also located close to CAe. This proximity made the communication and logistics operations easier for both the companies.
.jpg)
Figure 1. Motion cueing simulator seat
The simulator seats (Figure 1) will be utilized to provide pilots working in Air Force Hawk and Indian Navy with highly reliable replica seats in a simulation setting.
The motion cueing technology in the seats uses acceleration data acquired from the simulation physics prototype to convey both skin pressure signals and acceleration signals to give a sense of self motion to the pilots. This effect can be obtained by separating the mechanical modules concealed inside the gun rails and seat survival pack.
Planning, Finishing and Assembling of Seats and Frames
Ogle Models and Prototypes used the data and drawings supplied by CAe to plan which components had to be developed from the start, which could either be reclaimed from scrapped seats or can be obtained from new materials. Once this process was completed, Ogle Models and Prototypes had to plan the sequence, wherein each component was required to facilitate a systematic assembly of the seat and frame.
After the planning phase was over, back moulds and seat cushion were CNC machined from ureol model board and then produced in GRP style. Then, the main frame was developed and the corresponding micro switches, components and working mechanisms were installed step by step and tested to ensure that each component worked as planned.
Ogle Models and Prototypes and CAe worked closely all through the project. CAe and then visited the Ogle Models Letchworth offices to ensure that the project was being carried out on the scheduled time and also in line with its high quality standards.
.jpg)
Figure 2. The seat was modelled to look and feel as close to the real thing as possible.
Once the frames and seat models were finalized, the whole unit was separated and all the parts were finished to the desired specification prior to the final assembly. After the seat was organized for the last time, the labels that would be normally seen on a production seat were applied so that the seat looked and felt as real as possible (Figure 2).
Conclusion
CAe was happy with the outcome of the project and the excellent service provided by Ogle Models and Prototypes. With continuous investment in expertise and technology, Ogle Models and Prototypes provides excellent design and model-building solutions for a variety of applications.
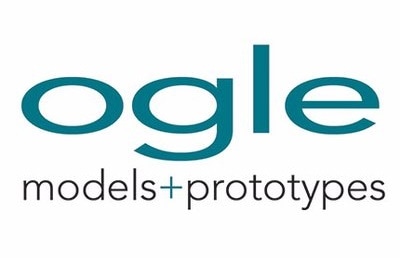
This information has been sourced, reviewed and adapted from materials provided by Ogle Models and Prototypes.
For more information on this source, please visit Ogle Models and Prototypes.