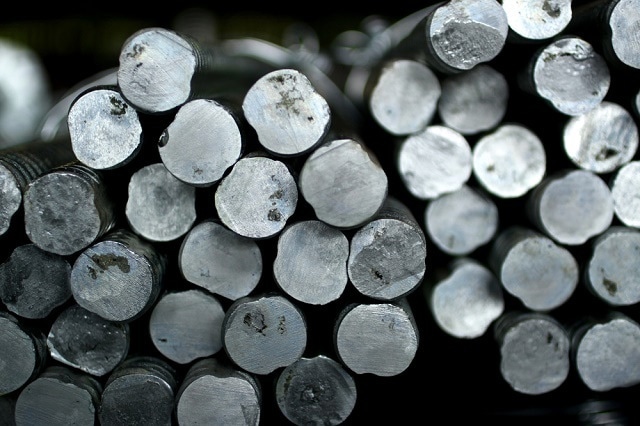
Image Credit: SARIN KUNTHONG | Shutterstock.com
For thousands of years, the development of new metal alloys has mostly been trial-and-error. Typically, one metal component has been dominant; with other metals comprising a small percentage of the recipe.
However, a study published in May by a team from MIT has indicated a new methodology that could help direct attempts to turn this ancient process on its head, potentially opening the door to new classes of alloys with previously unseen properties.
Published in the journal Nature, the process also threatens the customary wisdom that increasing the strength of a metal alloy is invariably a tradeoff causes in a loss of ductility, or the ability to a metal deform without breaking.
The new process is partially based in a hot topic of research right now – high-entropy alloys (HEAs). HEAs include several metallic elements in approximately equal amounts, which some materials researchers have suggested could produce single-phase microstructures and enhanced mechanical durability and stability.
While exciting to scientists, HEA research has yet to produce a viable advanced alloy, so the MIT team decided to take a different route. The researchers combined the standard methods used to make HEAs with the technique used to make steel, one of the sturdiest materials ever developed. The result was an alloy that has more than one stable configuration, which is known as metastability, and some unstable configurations.
The new alloy outperforms most HEAs, and importantly, it was able to increase both stability and ductility. However, it doesn’t have the stability of steel and the MIT researchers said that they are determined to develop more stable HEAs.
The team noted their new alloy is important because proves the validity of their new hybrid process.
3-D Printing
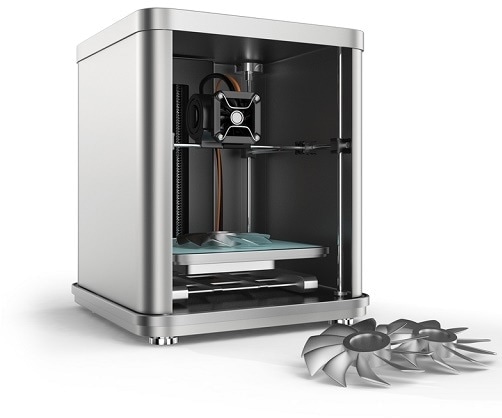
Image Credit: Chesky | Shutterstock.com
Three-dimensional printing is often seen as the future of fabrication, and alloys are undoubtedly a part of that future.
While machine parts can currently be fabricated with 3-D printing, according to the Max Planck Institute in Germany, the use of existing alloys doesn’t take full advantage of the technique’s possibilities. That’s why the German institute created the Alloys for Additive Manufacturing research group.
At Carnegie Mellon University, researchers announced they have been working out the kinks in 3-D printing titanium. X-ray imaging scan on 3-D printed titanium revealed a high degree of porosity within the material. Microscopic spaces in the printed titanium were found to range from a couple to a few hundred microns across. Randomly distributed, the pores are capable of causing a catastrophic fault line.
The team went on to find that the energy, pace, and spacing of the printer’s laser beam all affect the porosity inside titanium 3-D printed objects. Although adjusting these parameters helped the study team to cut back porosity in the 3-D printed titanium, they could not totally eliminate it.
The CMU researchers said they believe studying the titanium powder used in the fabrication process could maximize their outcomes because the factors for porosity are like found at the powder level.
A Big Data Approach
The search for new alloys used to be done incrementally, and often through the process of trial-and-error. But now, materials researchers are leveraging the power of Big Data through the use of supercomputers.
Researchers have already produced entire catalogs of candidate alloys. Even information from failed studies can offer useful data for today's powerful number crunchers. Several of these candidates are totally hypothetical, but engineers are actually starting to narrow down candidate worth synthesizing and assessing for particular applications by looking through their desired properties. For instance, researchers may be trying to see an alloy's conductive or insulating properties, how it behaves as a magnet or how much stress it can tolerate.
Researchers still need to overcome a few obstacles before they can truly tap into the potential of big data. First of all, computer models still provide few clues on how an appealing material can be produced in a lab. Second, the process does not translate well to investigating structural materials, like steel, that are required to construct, for instance, airplane wings or engines. This is due to mechanical properties like springiness and hardness rely on how a material is processed, which is something codes alone cannot describe.
In the short term, materials researchers must rely on experiments and data exchange among various programs. In the long term, researchers must hope for leaps forward in computer science, which are expected to come in the next few decades.
References and Further Reading
Disclaimer: The views expressed here are those of the author expressed in their private capacity and do not necessarily represent the views of AZoM.com Limited T/A AZoNetwork the owner and operator of this website. This disclaimer forms part of the Terms and conditions of use of this website.