Apr 18 2002
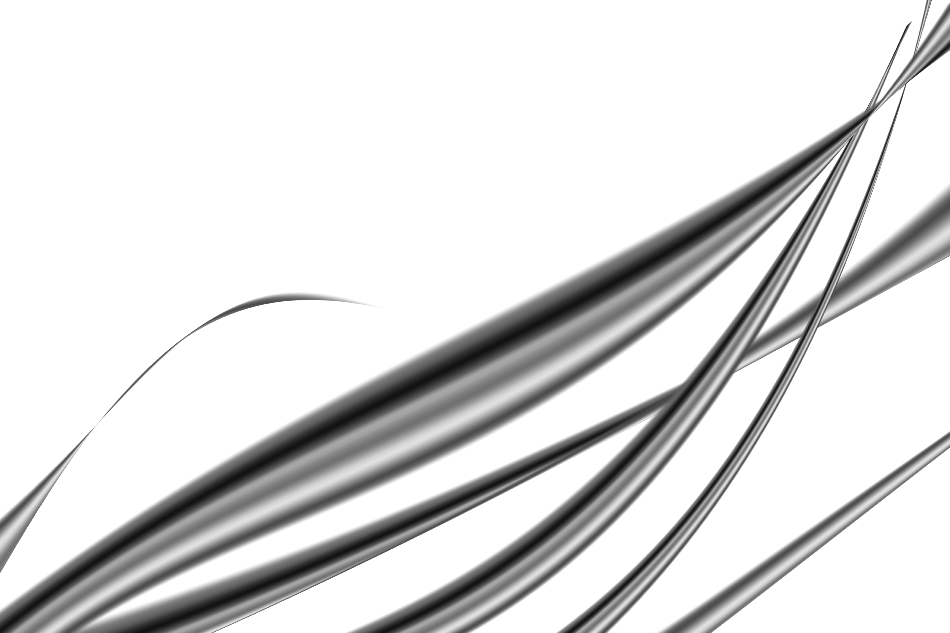
Apple Pho / Shutterstock
The basis of the nickel-titanium shape memory alloy (SMA) class is the intermetallic equiatomic binary alloy NiTi. Its moderate solubility range allows its composition to be changed, and also enables it to be alloyed with other elements to alter both mechanical and shape memory properties.
The nickel-titanium shape memory alloys exhibit common shape memory behavior and return to their original shape upon being heated to more than their phase transformation temperature.
When heated to this temperature, the alloy transforms from its low-temperature monoclinic martensitic structure to the high-temperature cubic austenitic structure.
Manufacture of Nickel-Titanium Alloys
Several methods can be used to manufacture nickel-titanium alloys, including vacuum melting methods like:
- Vacuum arc melting
- Electron beam melting
- Plasma arc melting
- Vacuum induction melting
Due to the high reactivity of titanium, vacuum methods are generally preferred. However, inert atmospheres can also be utilized effectively.
Hot Working
In general, ingots are hot worked in the temperature range of 700 °C to 900 °C as the subsequent stage in the process of sheet, wire, or bar formation. Different processes like extrusion, press forging, bar rolling, and rotary forging are employed for this purpose. Alloys do not react readily with air; hence, they can be hot worked.
Cold Working
Several cold working methods can also be employed, the most common among which is wire drawing, that yields diameters as small as 0.05 mm with superior surfaces. Yet, work hardening happens instantly and constant annealing is often needed.
Work hardening and proper heat treatment can reduce the deformation stress. Apart from enhancing the strength of the austenitic phase, this process also provides a two-way shape memory effect to the alloy.
Fabrication
Welding
Although nickel-titanium alloys can be welded, they tend to produce brittle joints. Brittleness can be minimized by relieving stress, but the high temperatures that are needed could lead to degradation of the shape memory effect. It is also necessary to perform welding under inert gases to avoid the accumulation of passive oxide.
Soldering
While soldering nickel-titanium alloys, the accumulation of passive oxide can pose challenges, quite similar to the welding process. Although the soldering process is hard, it can be performed using an Sn–3.5Ag solder with extremely high flux. By contrast, plating with gold or nickel before soldering can lead to better solder joints.
Joining
Adhesives like epoxies, cyanoacrylates, etc. can be used to join nickel-titanium alloys. Mechanical techniques such as swaging and crimping have also been found to be useful. It is also possible to use the shape memory effect itself, which has been applied commercially in couplings.
Machining
Traditional methods can be used for machining nickel-titanium alloys, but due to high wear, which is very common, carbide tools are recommended.
Alternative methods like electro-polishing and electro-discharge machining can be utilized under suitable conditions.
Coating and Plating
Coating and plating of nickel-titanium alloys can be done. However, optimal adhesion is essential to withstand the high strains experienced in certain applications.
Although it is possible to use alternative coating methods, shape memory properties can be destroyed due to the high curing temperatures.