February, and love is in the air for St Valentine's Day on the 14th. Across the country, couples will be making the ultimate commitment to each other, backing up their declarations of undying desire with something solid in the form of a ring. These tokens will be more than expressions of true romance, however, they will represent the latest in materials processing technology for jewellery.
Engelhard-CLAL, one of Europe's leading jewellery production specialists, has developed a new process using powder metallurgy technology for making gold, silver and platinum wedding rings. It is currently patenting the proprietary technique, which offers the possibility of high volume production of rings to a more consistent quality.
Traditional Fabrication Techniques
Rings are conventionally produced by punching out flat, washer-shaped rings from sheets of gold, silver and platinum alloys. The washers are turned into the D-shaped or oval-profile rings used in the Jewellery industry by rolling processes.
Powder Metallurgy Fabrication
The powder metallurgy route eliminates the need for punching and much of the rolling. The powders used in Engelhard-CLAL’s new process are produced directly from the molten state by passing the material through high pressure water or gas jets. The powder is then packed into a die and pressed to form a ring that has a rectangular cross-section. At this stage the ring is known as a ‘compact’, and needs sintering to give it strength and workability.
Sintering
Engelhard-CLAL is using a rotary hearth furnace (figure 1) designed by Carbolite for the sintering stage. The furnace enables high throughput of compacts, which are loaded into trays holding several hundred at a time. After loading, the furnace rotates by 10° to allow another tray to be added - the speed of rotation can be adjusted to give sintering times of up to 24 hours.
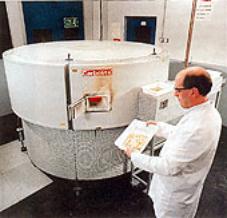
|
Figure 1. Rotary hearth furnace used for powder metallurgy ring production.
|
The heat of passion is nothing compared to the temperature inside the furnace. Rings are processed at 750-800°C under an atmosphere of 95% nitrogen and 5% hydrogen. This prevents oxidation of the precious metals, which would spoil the appearance and properties of the rings. Heating is provided by 27 wire spiral resistance elements supported on ceramic tubes, which are separated into three control zones to provide in-furnace temperature uniformity. After sintering, the trays are pushed out of the furnace chamber and rolled into a water quench tank to cool.
Secondary Forming Processes
The cross-section of the rings is then tailored to that required in the jewellery industry using special ring-rolling equipment.
Closing Remarks
Although the institution of marriage is said to be in decline, Engelhard gets through 600kg of gold, silver and platinum each year, producing 250,000 rings. And if this Valentine's Day provides a bumper crop of conjoining couples, sintering could be made fully automatic to speed up supplies.
|