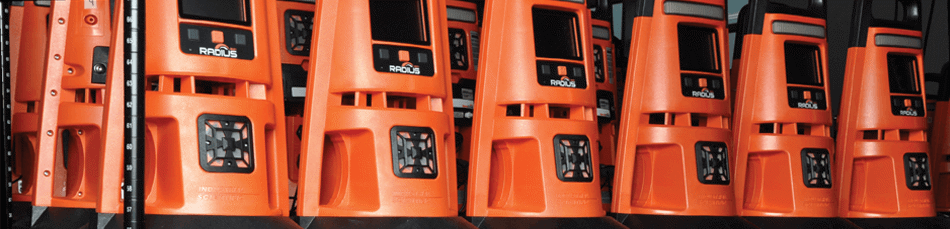
Setting up a new plant turnaround is a major project, with heavy financial investment as well as the potential for significant effects on the players involved. This requires meticulous planning and a failsafe performance. The pattern of workflow, number of people and the types of equipment as well as moving parts are all likely to see a lot of changes during this process.
During this upheaval, it is vital to keep everything connected with the project in synchrony, so that they come together to keep the plant down for as short a time as possible, which enhances its working to the greatest extent possible, without compromising safety aspects throughout the project.
The Radius® BZ1 Area Monitor is ideally suited for this task, helping to achieve faultless continuous monitoring of the area of operational revamping in every application where this is a must, even as workers keep on with their personal gas monitors as required by the plant’s safety rules. The device has been subjected to extensive testing and verification before being stringently recommended for such application scenarios. The reasons for this strong advice include:
Long Battery Life
The Radius BZI can operate for up to seven or eight days in succession without requiring a battery recharge, which means the need for workers to maintain the instrument is significantly less. For instance, a battery recharge requires the charging of the battery and bump testing, which in this case is needed only once a week rather than once a day, as with many other systems.
This means not only that less labor is involved, reducing the costs of maintenance, but also that hazardous risk exposure by the workers is very much less than expected as they need not enter the areas of renovation. By simply ensuring that two reserve monitors are always charged, downtime can be avoided completely, by just replacing a worn-out instrument monitor with a fully charged one as required.
The structure of the instrument makes recharging easy: by taking out the SafeCore® Module, which is the central processing unit (CPU) of the monitor and placing it correctly within the DSX™ Docking Station, the instrument is automatically recharged, and bump testing completed. In addition, the ability to monitor the process being carried out for seven to eight days without an instrument change means that fewer entry permits need to be issued for workers to attend to these machines.
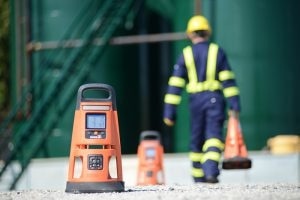
The Radius BZ1 can quickly be deployed across a plant during a shutdown or turnaround.
Easy Set-up
The design of the Radius BZI means that the monitors just have to be switched on and put into the right locations to keep a watch over the hazardous area day and night, without the frustration or unnecessary delays common with other monitors. These are built with special LENS™ Wireless capability to ensure that they receive and transmit data from and to each other within the network without any additional computers or software, having to register licenses or any other tools.
Again, if an alarm is activated on any of these instruments, it triggers off the same reading on all the others in the same network. An optional facility is the ability to incorporate the Ventis® Pro Series personal gas monitors from Industrial Scientific, which can be conveniently added in by simply switching them on and setting the channel to the one already used by the network, so that the area is under moving and static surveillance.
Availability for Rental
This facility allows plant managers to decide against a permanent investment, instead using these high-end instruments as part of a detailed turnaround project on a rental basis. This suits the type of project which is by nature a short-term and constantly changing one. The number of instruments and the date of delivery need to be communicated according to the progress of the project and the need for them, even at the last minute.
This will not compromise the availability of the required number of monitors to make sure the hazardous area is under constant surveillance to assure safety, for as long as the need persists. More monitors can be added, or damaged to inoperative ones replaced, at will, within a period of less than 48 hours. This prevents significant downtime. All these monitors are maintained only by Industrial Scientific staff and are already set to client specifications before delivery.
Thus, during any plant turnaround project planning, it is advisable to think about where continuous area monitoring will add value and safety to the operational processes.
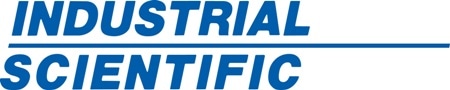
This information has been sourced, reviewed and adapted from materials provided by Industrial Scientific.
For more information on this source, please visit Industrial Scientific.