.jpg)
Plant shutdowns typically occupy less than 5% of the time, in an industry which demands continuous operation. However, this brief period accounts for over seven out of every ten major accidents, occurring while non-routine tasks are being performed such as plant shutdown, startup, or online maintenance.
This is due to the very disruption of routine, and the carrying out of unfamiliar processes, opening, and cleaning or the emptying of equipment, and the multiplication of people’s movement as well as of vehicles moving within the plant, including forklifts and trucks, all at a level several times above normal.
This has been experienced for decades by a certain Louisiana manufacturer of chemicals, which has always been marked by and recognized for its strong emphasis on safety in the workplace. The knowledge gained led to the adoption of a high-class solution for detection and surveillance of explosive limits in one of the most accident-prone plant areas, because of a high level of movement – the areas of entry, exit and movement through the plant of construction vehicles.
The Need
When the plant was in the process of shutdown, there were hundreds of vans and trucks, welding trucks, forklifts, and contractor vehicles, going in and out of the site every single day. In hazardous areas which may contain inflammable gases or vapors, there was a high risk that these would mix with air, which behaves as an oxidizing reagent.
When the vapors or gases enter the engine cylinders along with the mixed air, a readymade fuel source is created which pushes up the ratio of fuel to air inside the engine. This has the potential to trigger an explosion by increasing the temperature of the engine or sparking.
To prevent this, the hazardous area around the plant was first demarcated and sealed off by a yellow gate, using the log of traffic entry during the previous shutdown. Once the vehicle entered the gate, it was inside a zone subject to continuous lower explosive limit (LEL) monitoring. The firm in charge of safety for the company oversaw choosing which option would work best to accomplish LEL detection in this situation.
One choice might be to use a fire watch safety employee armed with a portable LEL monitor to meet each vehicle at the gate through the pathways within the plant and then back out through the yellow gate. This would not work here because of the hundreds of vehicles involved.
The Solution
The safety provider for the company suggested the use of continuous area monitors, and in particular the Radius® BZ1 Area Monitor from Industrial Scientific, which was fitted with LENS™ Wireless technology. The devices were already familiar to the safety team from another client experience. The most compelling feature was the battery life.
Each monitor runs for seven to eight days on a single charge, which meant they could run each device continuously for this period instead of deploying ten people during each shift of each day, just to recharge the monitors. They had already experienced the hassles of the latter case with detectors made by another company.
Thus, this time around they opted to use 171 Radius monitors over all, of which 146 were set up in a network over the 60 days or so that it took to shut down the plant. This also avoided the need for daily bump testing, since each monitor needed to be bump tested only after seven to eight days, when its battery ran out and it was rotated out for recharging.
.jpg)
“What immediately drove us to choose the Radius was the battery life. We knew that we would be able to let every monitor run for 7 or 8 days instead of having to send out 10 people per shift per day to change out batteries, as was the case with another manufacturer’s instruments that we used in the past.”
The Lens wireless technology of Radius BZI monitors meant that each monitor within the network began to send and receive information from all the other devices automatically, and thus a dangerous LEL reading or gas detection alarm by one monitor would be instantly picked up by all the others, as well as showing the machine from which the alarm originated. This enables prompt identification by vehicle drivers of the hazard zone so that they can immediately shut off their vehicles and leave the area.
The arrangement of the monitors was as follows: groups of 18 to 20 devices were placed at strategic points along the corridors through which the vehicles moved. They were placed atop aluminum pedestals about two feet above the ground, so that they could withstand the rugged environment, including drenching rains and constant dust clouds.
25 of the total of 171 monitors were always kept in reserve, having been completely charged, so that they could be switched into the network wherever they were needed. Whenever one group of 20 monitors was about to run down, their central processing units or SafeCore® Modules were simply withdrawn from the base of each unit and replaced with the charged reserve modules.
There were 20 DSXi Docking Stations which needed only to be unboxed to be fit for work, and these were used to recharge and bump test the exhausted SafeCore Modules, which were then kept ready to rotate back into the network when the next group of units needed to be recharged. This cycle kept the plant vehicle corridors under continuous surveillance throughout the 60 days of the project.
.jpg)
Twenty-five instruments were kept on reserve, fully charged, and rotated in as needed. This continuous rotation allowed for uninterrupted monitoring for the 60-day duration of the project.
The Result
The safety provider estimated that the cost of using Radius monitors more than halved the financial costs as compared with employing fire safety watch staff, as well as sharply reducing the number of work permits that needed to be issued. Again, out of the total number of 171 monitors, only two presented any working issues, which resulted in an incredible 99% performance rate.
The customer was also extremely impressed, giving in a positive quality notice to the safety provider and expressing appreciation of the working of the Radius monitors. Following this, the chemical manufacturing plant has used the Radius BZI Area Monitors for eight to ten newly added projects, on a smaller scale, making it their go-to area monitor in such situations.
References and Further Reading
i] William Bridges, Process Improvement Institute, Global Congress on Process Safety, 2016; Necessity of Performing Hazard Evaluations (PHAs) of Non-Normal Modes of Operation (Startup, Shutdown, & Online Maintenance).
[ii] OSHA Fact Sheet: Internal Combustion Engines as Ignition Source
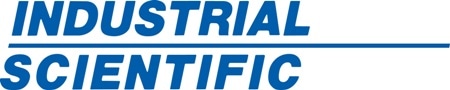
This information has been sourced, reviewed and adapted from materials provided by Industrial Scientific.
For more information on this source, please visit Industrial Scientific.