Nov 5 2018
Exploring Structural Steel
From the buildings people visit, to the homes they live in, to the roads they travel, the structural steel plate is a multipurpose construction material that provides fabrication versatility and structural strength without extreme weight. This article takes a deeper look at structural steel, its composition, characteristics, uses and more.
.jpg)
“Alexandra Bridge” by tsaiproject is licensed under CC BY 2.0
What is Structural Steel?
A regulated category of steel, structural steel has to meet industry standards for dimensional tolerances and composition. In the United States, steel grades are specified and regulated by ASTM International. Likewise, Europe and Canada have their own regulating bodies and standards. While Leeco Steel does offer EN standard steel plate and CSA G40.21 steel plate, this article will concentrate on ASTM standards.
A wide range of structural steel grades is available, with the most popular being ASTM A572 and ASTM A36. These steel grades along with other structural steel grades are mainly used for building frames of bridges and buildings.
They are also employed in the construction of:
- Freight cars
- Construction equipment
- Truck parts
- Machinery
- Crane booms
- Transmission towers
- Truck frames
A research published by the American Institute of Steel Construction shows that structural steel contains 47% of all construction materials, making it highly probable that structural steel is responsible for some of the design in structures, buildings, or bridges encountered by people.
Producing and Testing Structural Steel
In order to fully comprehend how structural steel varies from non-structural steel, like the steel used on truck beds, ships, or military tanks, it is important to look at the composition of the structural steel.
Steel can either be made from raw materials, or can be manufactured from recycling old steel. During the process of changing recycled steel into new steel, existing steel is melted down and refined to fit certain specifications. It is a much longer process to make steel from raw materials.
Steel is an alloy containing carbon and iron, both of which are abundantly available but seldom found in pure form. In order to make steel from raw materials, iron is obtained from iron ore, which contains plenty of iron oxides. Most of the iron ore in the United States is extracted from taconite, which is abundantly available in Minnesota. During the extraction process, taconite is ground into a sandy composition, and magnets are used for separating the iron ore (in the form of magnetite) from other substances and minerals.
Although iron is often believed to be strong and hard, raw iron ore is so soft that it can be cut with a knife and some muscle. Iron-based alloys get their strength from the addition of carbon.
An iron-carbon alloy is generally produced by combining coke with iron ore and applying heat until the coke ignites. Coke is a carbon-rich form of coal. As a result of this strong heating, coke drops carbons and adheres to oxygens from the iron oxides, leaving a combination of carbon and iron. This process is called reduction.
Following reduction, around 4% carbon is present in the material, which is subjected to more heating and cooling processes to reduce the amount of carbon, rendering the material stronger and harder. As soon as the carbon content falls below 2.1% of the material’s weight, the material becomes steel. In order to make structural steel, carbon should be further reduced until its composition is just 0.05%–0.25%.
.jpg)
The final outcome is a structural steel,which is economically priced, 100% recyclable, and has a high strength-to-weight ratio. Different grades of structural steel are available, all of which vary somewhat in composition. These compositions considerably help in establishing the material required for any specified project.
On the other hand, the steel can be additionally processed — through more heating and cooling treatments and/or the addition of alloys, for example, titanium, molybdenum, and chromium — to boost the hardness. These processes affect the overall brittleness, in most cases, rendering the ensuing material unsuitable for structural applications.
Structural Steel Composition
The following is the composition of two well-known grades of structural steel: ASTM 572 and ASTM A36. While other structural steel grades possess analogous compositions, they may also have extra alloys or have undergone additional processing.
Grade |
Carbon |
Manganese |
Phosphorus |
Sulfur |
Silicone |
A36 |
0.25-0.29% |
1.03% |
0.04% |
0.05% |
0.28% |
A572 |
0.18-0.23% |
0.5-0.7% |
0.035% max |
0.04% max |
0.150-0.3% |
A514* |
0.12-0.21% |
0.85% |
Not specified |
Not specified |
0.28% |
*A514 also contains 0.2% molybdenum, 0.48% chromium, 0.05% vanadium, 0.02% titanium, and 0.003% boron.
The presence of additional alloys that boost both hardness and brittleness is the main difference in composition between non-structural and structural steel. In certain cases, the additional alloys are still able to create structural-grade steel; however, in other cases, the steel produced is extremely brittle for use in structural capacities.
Yield and Tensile Strength
Beyond chemical composition, tensile and yield strengths help in establishing the steel grade as well as the overall application.
The highest point of stress is yield strength, at which material will change shape permanently. For instance, when someone jumps off a diving board, the board naturally bends to absorb the energy and weight, but after that person leaps from the board, the board will return back to its original shape. The yield strength of the board would be the point where it bends under energy and weight, and stays permanently bent even after the diver launches.
A vital characteristic of structural steel, yield must have some give to absorb weight. For instance, the yield strength in bridges is the maximum weight that can be tolerated by the bridge before experiencing permanent damage.
Tensile strength refers to the point at which the bent material will break. In the above diving board example, this is the energy and weight it would take to break the board.
The following is a chart that demonstrates the tensile and yield points of three common types of structural steel. These points are either calculated in kilopounds per square inch (“ksi”) or in pounds per square inch (“psi”), as indicated below. At times, they are also referenced in megapascals.
Grade |
Yield Point |
Tensile Point |
A36 |
36 ksi |
58-80 ksi |
A572 |
42-65 ksi* |
0.5-0.7% |
A514 |
100 ksi |
110-130 ksi |
*Yield depends on thickness, but the most common grade is 50 ksi.
These two metrics are very important to engineers as they plan the required material for a specific project.
Charpy Impact Test
What is particularly significant in structures is their potential to absorb energy. Brittle materials are only capable of absorbing a low amount of energy prior to failing or fracturing. Structural steel integrates ductility with strength, enabling it to absorb large amounts of energy prior to failing.
The Charpy impact test — termed after Georges Charpy, who was responsible for standardizing impact testing — employs a heavy hammer pendulum to calculate the amount of energy that can be absorbed by a specific type of steel. The Charpy impact test goes a step further and tests impacts at different temperatures. This is vital for steel-based structures that are outdoors in adverse temperatures.
For structural steel projects, Charpy tests are relatively common. A small sample of the steel — called a coupon — is cut out of the master plate and then taken to an independent laboratory for testing. The outcomes tell engineers whether the material is sufficient for their project.
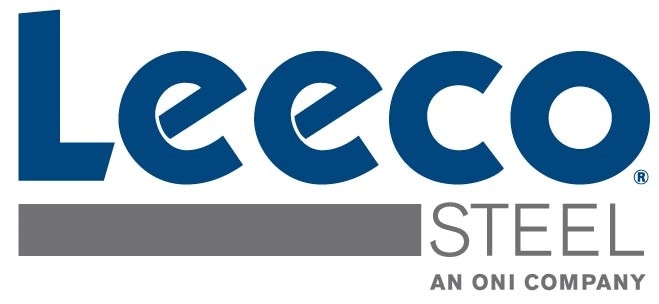
This information has been sourced, reviewed and adapted from materials provided by Leeco Steel, LLC.
For more information on this source, please visit Leeco Steel, LLC.