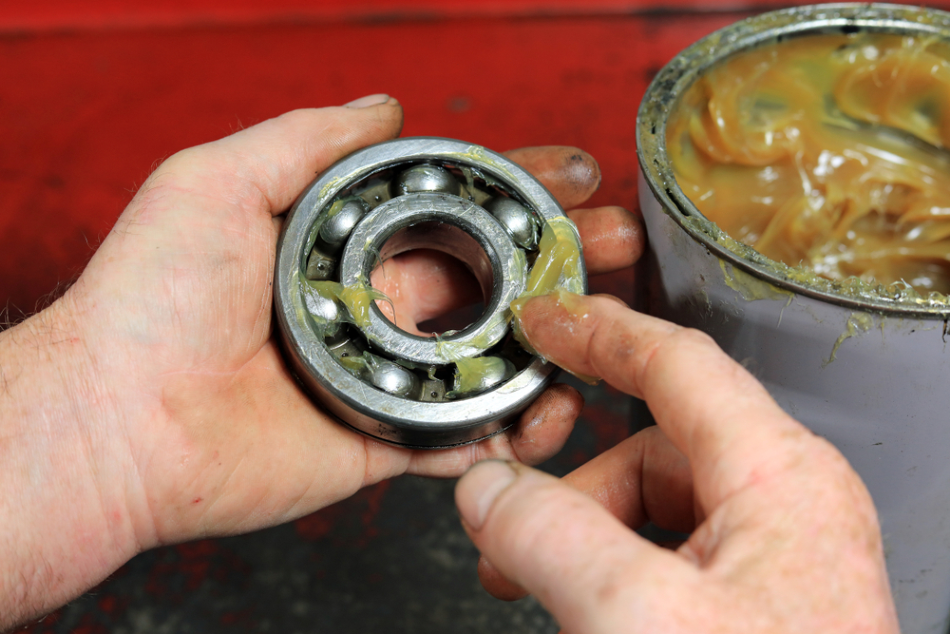
Image Credit: Dean Clarke/Shutterstock.com
Grease application is a necessary component to ensure product friction and less deterioration from surfaces rubbing together. There are a variety of grease additives, including but not limited to anti-foaming agents, detergents, rust inhibitors, extreme pressure additives, viscosity index improvers, and antioxidants.
These additives help limit the likeliness of corrosion and rusting, as well as improve the fluidity of product molding. Oxidation most commonly destroys parts of base oils, due to circulating oxygen in the air.
What is Anti-Galling?
It is easier to understand galling, before anti-galling. In other words, galling is a type of corrosion between surfaces. Typically, galling forms when surfaces are sliding together and there is a significant amount of compression or pressure between the two materials. Galling will pull with the contacting surface, creating folds in its connecting part. Both adhesion and friction stimulate galling, causing balled-up and sticky material to lump together on the object’s surface. Galling also causes the deconstruction of crystal compositions below the targeted area; the surface area is not the only part of the object to experience a slip and tear.
Therefore, anti-galling additives are those that inhibit this type of wear and corrosion of surface area. These specific additives seek to eliminate short-term performance, as well as material wear and tear.
Effects of Grease Additives
Various grease additives will be joined with their designated function. These helpful lubricants are typically quite expensive to retrieve - not to mention the detailed science of processing and mixing the right formulas. In light of this, grease additives can make up to almost thirty percent of the oil used in an application.
Additives can be used for strictly surface erosion or just the oil combination molding the product. All in all, grease additives are chosen because they mix easily with other base oils; and in return, can be added to less costly oils, which creates an affordable and apt final product.
Anti-foaming agents are implemented to reduce surface foaming. The additive’s effects reduce oil’s bubble wall and catalyze bubble bursting, which ultimately minimizes the chances of product foaming. However, the amount of anti-foaming agents used in any given time must be closely monitored because like other grease additives, too much of them can cause a reverse effect.
With an additive such as detergents, multiple functions can be performed. They are most commonly used for neutralizing acidic growth in oils. Dispersant and detergent additives are usually combined to mediate detergent flaws and secure optimal neutralizing power.
Extreme pressure additives create a pool of chemical additives that shape a barrier around vulnerable surface space. If the material’s oil film starts to deconstruct, the additive does not give way to high pressures and prevents the wearing of the surface.
In some cases, the effects of certain grease additives are plainly stated in their names. Rust inhibitors are used with metal materials and avert rusting between the metal and grease additive. Viscosity index improvers limit the speed of fluidity change that occurs with varying temperatures and different external pressures on materials.
As said before, these are only a few examples of the many grease additives being made and implemented for anti-galling techniques.
The Downfall of Grease Additives
Unfortunately, grease additives and their effects are not invincible. Additives typically have an expiration date - the more times oil is used, the more and more of that additive is also used, thus either separating from the product or decaying along with the material.
Several telling processes occur once an additive has reached the end of its life. Wear starts becoming more rampant, viscosity is unregulated, and destructive acids begin showing noticeable wear.
Using too much or too little of a particular additive can prove to be ineffective and useless. As well as this, mixing some additives can also cancel each lubricant’s benefits; thus, targeting a specific function for a grease additive is only the first step to a much longer process.
References and Further Reading
Disclaimer: The views expressed here are those of the author expressed in their private capacity and do not necessarily represent the views of AZoM.com Limited T/A AZoNetwork the owner and operator of this website. This disclaimer forms part of the Terms and conditions of use of this website.