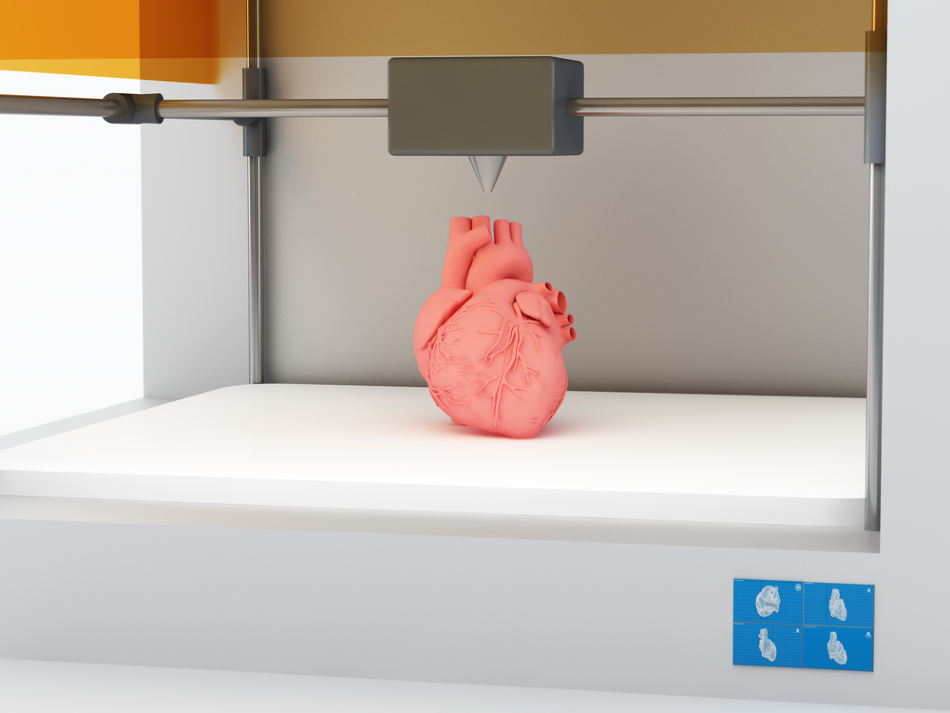
Image Credit: belekekin/Shutterstock.com
3D (three-dimensional) printing techniques have been in development since 1974, when pioneering British chemist and author David E. H. Jones proposed a concept for 3D printing in his regular New Scientist column, “Ariadne”. There, Jones fantasized about laser-based polymerization techniques with which “any type of solid object at all could be made up: even complex interlocking and re-entrant shapes quite impossible to mold”.
Perhaps inspired by the potential applications in research and development, engineering, manufacturing, and a plethora of other fields more so than by Jones’s lighthearted article, researchers in academia and industry have spent recent decades realizing what was mere fantasy 40 years ago.
Additive Manufacturing
Modern 3D printing is also known as additive manufacturing and includes a wide variety of techniques. In all of them, components, devices, and so on are “printed” layer by layer from the desired material or materials. These layers are printed using various material depositors, guided along x and y axes by computer-assisted design (CAD) software. The z height axis profile is given by the successive build-up of layers over one another.
The benefits of additive manufacturing are wide-ranging. Multiple design iterations can be tried out in relatively cheap materials to test compatibility with existing systems, measure mechanical properties, and visualize dimensions more easily. Further, unlike classic subtractive manufacturing, 3D printing techniques do not waste excessive material by cutting it out, profiling it, and grading it.
Functional Elements
Additive manufacturing is no longer only suited to simple mechanical or structural elements and components made of single materials, and its uses are extending far beyond the research and development phase of the manufacturing process.
Now, the complex interlocking and re-entrant shapes that Jones fantasized about are possible. As well as this, multi-material 3D printers have been developed, as well as advanced lithographic techniques.
These developments have resulted in additive manufacturing’s increasing ability to create numerous advanced and functional elements, and further progress in this area can be expected. Below are a few of the functional elements that 3D printing can create.
Super Titanium Tailpipe
Koenigsegg, the Swedish supercar manufacturer, produced One:1 supercar in 2014. Research and development for this superfast vehicle was heavily reliant on the rapid prototyping design process made possible by 3D printing, but the final product itself also featured 3D-printed functional elements. The tailpipe printed entirely in one piece of titanium was the largest 3D-printed titanium object at the time, taking three days of continual printing to produce.
Totally Personalized Human Body Implants
3D printing saw some of its first non-research applications in medicine. It can be used to create totally personalized implants that match patients’ unique individual bodies. These functional elements of the human body – and additions to it – represent a growth area for additive manufacturing, especially with aging populations around the world requiring hearing aids and dental implants to be produced at a much higher rate in future years.
Automated Circuit Board Assembly
In computing manufacture, 3D printing can be used to remove the need for lengthy and tedious processes of imaging, drilling, plating, solder mask coating, nomenclature printing, and surface finishing to produce circuit boards. All of these steps must be completed in meticulous detail, allowing for not inconsiderable margins of error in the process.
Additive manufacturing could replace these steps by starting from a final product in the CAD software, and building up to it in the required materials to make a single-component circuit board effectively.
Click here to have a look at different types of 3D printers
Future Integration of Functional Elements into 3D Printing
In the future, advances in additive manufacturing techniques will allow for a greater range of materials, scales of size, and complexities of design to be completed with a 3D printer. These advances could enable numerous functional elements to be produced, such as batteries, nanotechnology, engine parts, and more.
This future revolution in additive manufacturing is now the source of another scientific fantasy topic – one which could very well become a reality in decades to come. Advanced 3D printing would enable computers to rapidly prototype and test iterations of robots, machines, medicines and so on, enabling an automated system of work and support for the planet’s inhabitants.
A world in which robots can produce and repair robots automatically while continually developing their functionality could lead to technological utopia, and it may not be as unrealistic as it sounds. Jones’s readers in 1974 may have dismissed his laser-guided 3D polymerization “bath” as the fantasy of a lighthearted columnist, but we have already surpassed his vision.
References and Further Reading
Ellam, R. (2016). Editor’s pick: 3D printing: you read it here first. [online] New Scientist. Available at: https://www.newscientist.com/letter/mg23230991-100-1-editors-pick-3d-printing-you-read-it-here-first/.
ISO - International Organization for Standardization (2015). ISO/ASTM 52900:2015. [online] ISO. Available at: https://www.iso.org/standard/69669.html.
Taufik, M. and Jain, P.K. (2013). Role of build orientation in layered manufacturing: a review. International Journal of Manufacturing Technology and Management, 27(1/2/3), p.47. DOI:10.1504/IJMTM.2013.058637
Disclaimer: The views expressed here are those of the author expressed in their private capacity and do not necessarily represent the views of AZoM.com Limited T/A AZoNetwork the owner and operator of this website. This disclaimer forms part of the Terms and conditions of use of this website.