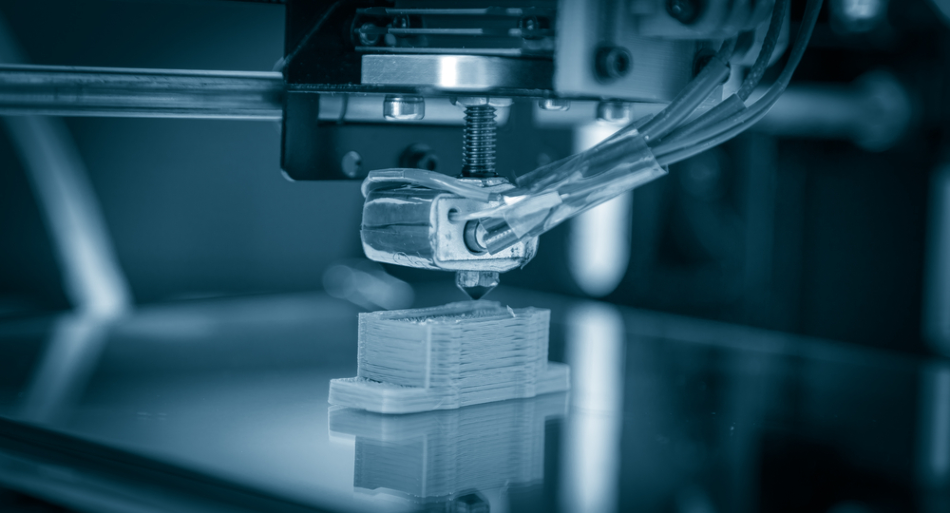
Image Credit: Alex_Traksel/Shutterstock.com
Although 3D printing technology has opened up countless possibilities, there is one large drawback to the conventional indoor 3D systems: they can only produce items smaller than the printers.
To address this drawback, engineers at the University of Chile have developed a 3D printing technology that is one part 3D printer, and one part climbing robot. The "Koala 3D" printer combines these technologies to print and scale along the object as it goes, enabling the additive manufacturing of objects without any size limitations.
How Does the Climbing 3D Printer Work?
The Chilean researchers developed their additive manufacturing system after realizing that a 3D printer capable of moving freely can produce items much bigger than the system itself. Therefore, the Koala 3D printer can horizontally and vertically navigate the object that it is fabricating during production.
To achieve this capability, the research team designed a robot that has a 3D printer head and a climbing system. Its climbing ability comes through the use of two actuated clamps. A bottom clamp is situated underneath the printer's body, while a top clamp has a range of motion that enables it to move between the top and the bottom of the printer head.
The team was able to create a complete range of motion for Koala 3D by having one clamp that is always attached to a support beam while the second clamp can be used to connect to a new anchoring point. The entire system fabricates using a "print-re-anchor" cycle.
The Koala 3D printer includes a positioning stage that moves an extruder and holds the raw 3D printing materials. The Chilean team said they had to develop a more sophisticated positioning system than the one commonly used in additive manufacturing. The extruder has a 45 mm x 45 mm range of motion on the horizontal plane. It is also able to produce vertical beams with an area of 30 mm x 30 mm.
Click here to find out more about 3D printing equipment
To test the viability of their system, the engineers conducted several tests and experiments. These evaluations were affectively able to show the 3D printing system is capable of achieving the essential 'printing-re-anchoring' cycle they had envisioned. The tests involved fabricating 11 test beams of various sizes, from 350 mm to 850 mm long. The team said they also use their additive manufacturing system to fabricate smaller parts conventional 3D printer are capable of making.
The Challenges of Creating a Climbing 3D Printer
While their system appears to be quite successful, the Chilean team mentioned three primary issues in the development of their 3D printer. First, there is an issue with dropping after re-anchoring. Second, a structural oscillation occurs at high aspect ratios. Third, there is an issue with the starting alignment between the part in the base. The engineers said fixing these issues is critical to developing 3D printers that are capable of climbing along the structures that they fabricate.
The study team noted that Koala 3D addresses a primary flaw with popular 3D systems: an inability to make objects larger than the printer itself. They said that their Koala 3D printer opens the door to greater design freedom and solving logistical challenges related to moving massive additive manufacturing equipment that is commonly used to create large outdoor structures. The researchers added that their technology could possibly be used in large-scale construction projects.
The Start of an Entire 3D-Printed Community
The technology to fabricate homes via additive manufacturing has been with us for many years now, and recently it was announced that an entire community of 3D-printed homes had begun construction using a 3D printing technology called Vulcan II.
Located in Tabasco, Mexico, the new construction project is a partnership between Texas-based construction tech company ICON and a non-profit housing organization called New Story.
The new project is just one of many construction projects featuring 3D systems that are currently underway to provide affordable housing in economically disadvantaged areas. In 2018, ICON and New Story fabricated a proof of concept dwelling that required 48 hours to build and came at a price tag of less than $4000.
ICON 3D Printing for the Homeless in Austin
Video Credit: ICON - 3D Tech/Youtube.com
The organizations have partnered closely with people in low-income communities In Latin America to understand best what their community and culture requires with respect to affordable housing. The goal is not just to provide affordable housing; it is to make sure that the fabricated housing suits their community's habits, objectives and needs.
According to recent reports, the project in Tabasco has fabricated two houses so far. The planning stage of this project took 18 months, but the actual construction of each home took around 24 hours. Each home is 500 ft2 and Includes two bedrooms, a kitchen, living room and a bathroom.
The partnership said it plans to build a 50-home community. As Tabasco is located in a seismic zone, the homes have been designed to surpass existing safety standards. Each structure features a reinforced foundation intended to last for many decades.
In addition to the current project, New Story is currently in negotiations with the local government to build even more homes after the initial 50 have been completed. These communities are designed to include utilities, green spaces and various amenities.
The Largest 3D Home to Date
With a footprint of 1900 ft2, the largest 3D-printed home to date was recently completed over an 8-day timeframe. The Autonomous Robotic Construction System (ARCS) used to make it required only 48 hours of actual print time, according to SQ4D, the company behind the system.
Fabricated and constructed completely on-site, the record-setting home cost just $6000 in materials. The robotic system also significantly reduced the labor to three people needed to build the home. With labor costs usually comprising around 40% of total construction costs for a home, the ARCS system has the potential to produce housing with substantial savings quickly. The additive manufacturing process is also much more efficient. Processes such as framing and siding are completely eliminated, while, according to SQ4D, the new structure is fire- and mold-resistant.
The company also announced that it expects to be able to cut the print time in half within the near future through refinements to the ARCS.
References and Further Reading
Essop, A. (2020) KOALA 3D: CHILEAN RESEARCHERS INVESTIGATE CLIMBING 3D PRINTER. [Online] 3D Printing Industry. Available at: https://3dprintingindustry.com/news/koala-3d-chilean-researchers-investigate-climbing-3d-printer-170424/ (Accessed on 24 April 2020).
Essop, A. (2020) THE FIRST HOMES HAVE BEEN BUILT IN NEW STORY’S 3D PRINTED COMMUNITY FOR LOW-INCOME FAMILIES IN MEXICO. [Online] 3D Printing Industry. Available at: https://3dprintingindustry.com/news/the-first-homes-have-been-built-in-new-storys-3d-printed-community-for-low-income-families-in-mexico-166830/ (Accessed on 24 April 2020).
Essop, A. (2020) SQ4D 3D PRINTS 1,900 SQ FT HOME IN 48 HOURS. [Online] 3D Printing Industry. Available at: https://3dprintingindustry.com/news/sq4d-3d-prints-1900-sq-ft-home-in-48-hours-167141/ (Accessed on 24 April 2020).
Disclaimer: The views expressed here are those of the author expressed in their private capacity and do not necessarily represent the views of AZoM.com Limited T/A AZoNetwork the owner and operator of this website. This disclaimer forms part of the Terms and conditions of use of this website.