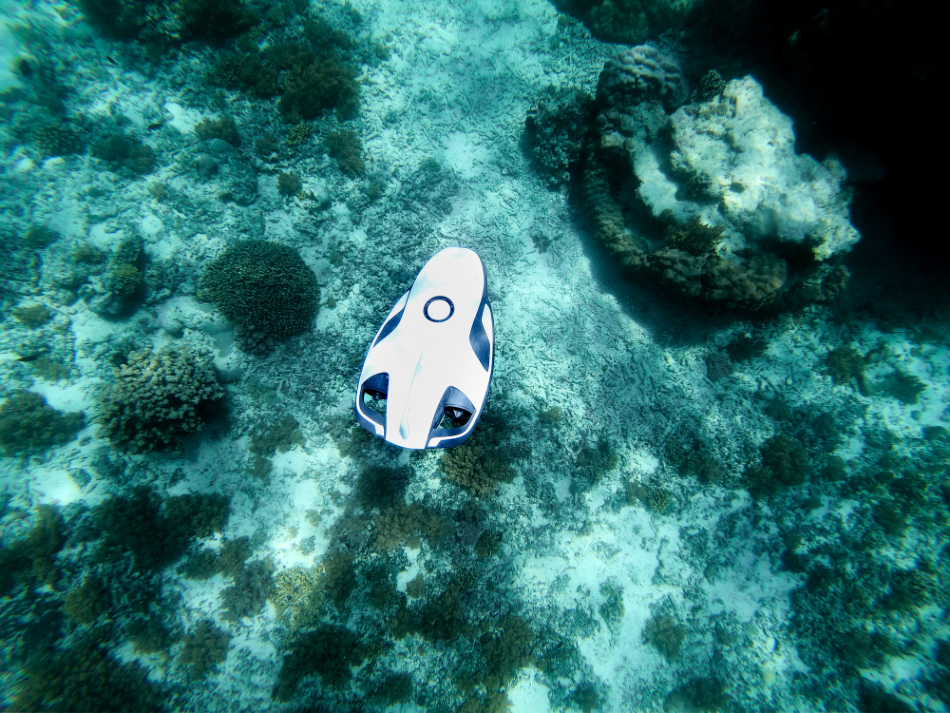
Image Credit: Kryvenok Anastasiia/Shutterstock.com
Autonomous unmanned underwater vehicles (UUVs) are used by the United States military as well as scientists gathering important data in the world’s oceans. However, these are often left in the sea when their mission is complete or retrieved from the ocean floor at significant expense. An innovative 3D-printable material can be used to make these vehicles biodegrade in marine environments at a predefined timescale.
Controlling the Rate of Degradation
Biopolymers do already exist and are used to create machines and devices that biodegrade in marine environments. However, there has been no way of controlling the rate at which these materials degrade until now.
The new 3D printable material solves this problem. Set lifespans of the final material can be finely tuned by adding a biological material (typically agar) in set ratios to a biodegradable polymer.
This means that devices such as UUVs can be designed to biodegrade in marine environments once their mission is complete. Not only does this eliminate the expense of retrieving equipment from the ocean floor – which is necessary if, for example, the machine incorporates classified technology – but it also helps to protect the delicate ecosystems in our planet’s oceans.
What is the New Material?
The new 3D-printable material builds on existing research into marine-biodegradable polymers. The inventors identify three ideal candidates for the biopolymer base: polycaprolactone (PCL), polyhydroxyalkanoate (PHA), or polybutylene succinate (PBS). The patent also notes that other materials could be used.
These polymers degrade for various reasons. For example, PCL degrades in water due to hydrolysis of ester bonds, while other materials attract microscopic marine life which eats away at the organic matter in the biopolymer.
How is the Rate of Degradation Controlled?
The three biopolymers identified as ideal candidates by the inventors of the new material cannot, by themselves, produce materials that biodegrade according to a set timeframe.
However, mixing an organic material – agar – in with the biopolymer at different ratios gives manufacturers control over the final material’s rate of degradation.
The table below indicates varying lifespans of the final material, based on the ratio of agar to biopolymer used:
Desired lifespan
|
Ratio of agar
|
Ratio of biopolymer (PCL)
|
Ratio of other biological materials
|
0-3 months
|
50-95%
|
5-50%
|
1%
|
3-6 months
|
25-50%
|
40-75%
|
0.1%
|
More than 6 months
|
5-25%
|
75-95%
|
Optional
|
How Do the Materials Included Affect the Final Product?
Agar is used in the new composite material as a gelling agent. In the ocean, the agar provides a structure from which enzymes and microorganisms can eat away at the biopolymer base. Because it is not digestible, controlling the ratio of agar to biopolymer material enables designers to control the final material’s rate of degradation.
In addition to agar and the base biopolymer, the inventors also experimented with the addition of other biological materials into the final composite. These can be a variety of materials selected for a variety of purposes.
For example, increasing the rate of degradation, providing a base structure upon which to grow organic structures, and even disabling explosive devices can be possible with the addition of various biological materials.
One candidate for inclusion in this way is synthetic hagfish slime, which was invented at the same US Navy laboratory.
How and Why is the New Material 3D-Printable?
The patent for the new material includes a suggested workflow for 3D printing. This makes it a more practical option for UUVs and other research machines, which are typically intended for single missions and produced with bespoke designs that fit the mission.
The process for 3D printing the new material begins with mixing the materials at the ratios desired and then extruding the composite material into filaments. 3D printing can then be performed using traditional additive manufacturing methods.
If the composite requires the addition of other biological materials (such as synthetic hagfish slime), then it must be 3D printed at relatively low temperatures to avoid killing the organic matter that has been added.
This is possible due to the low melting point of agar (approximately 85 °C), as well as the careful selection of biopolymer base material. Biopolymer materials such as polylactic acid (PLA) and polyhydroxybutyrate (PHN) only melt when heated to 173 °C and 175 °C respectively.
However, PCL and PHA can melt at much lower temperatures. PCL melts at 60 °C and PHA can be modified to melt at between 40 °C and 180 °C, depending on the starting monomer used. To demonstrate their method’s versatility, the researchers also experimented with PBS, which melts at 115 °C and is unsuitable for use with other biomaterials.
Find out more: 3D Printers and 3D Printing Equipment, Materials and Accessories
Military Applications and Beyond
As well as military and research applications, the new material could be used in a wide variety of commercial purposes. TechLink, a private organization that works with the US military to help companies commercialize military research, is offering licensing services to businesses at no cost.
The inventors of the new material – Josh Kogot, Ryan Kincer, and April Hirsch – are continuing their work at the Biotechnology Research and Development Lab in the Naval Surface Warfare Center (NSWC) in Panama City, Florida. The lab’s output will remain highly anticipated by the military, researchers and industry in years to come.
References and Further Reading
Kogot, Joshua M., Matthew R. Kincer, and April Hirsch. (2020) Review of Marine Biodegradable Composition for 3-D Printing. US Patent Office, issued August 25, 2020.
Techlink (2020) Disposable oceanic sensors, underwater vehicles? Biodegrading 3D printing material invented in Navy lab. Techlink. Available at: https://techlinkcenter.org/news/disposable-oceanic-sensors-underwater-vehicles-biodegrading-3d-printing-material-invented-in-navy-lab
Disclaimer: The views expressed here are those of the author expressed in their private capacity and do not necessarily represent the views of AZoM.com Limited T/A AZoNetwork the owner and operator of this website. This disclaimer forms part of the Terms and conditions of use of this website.