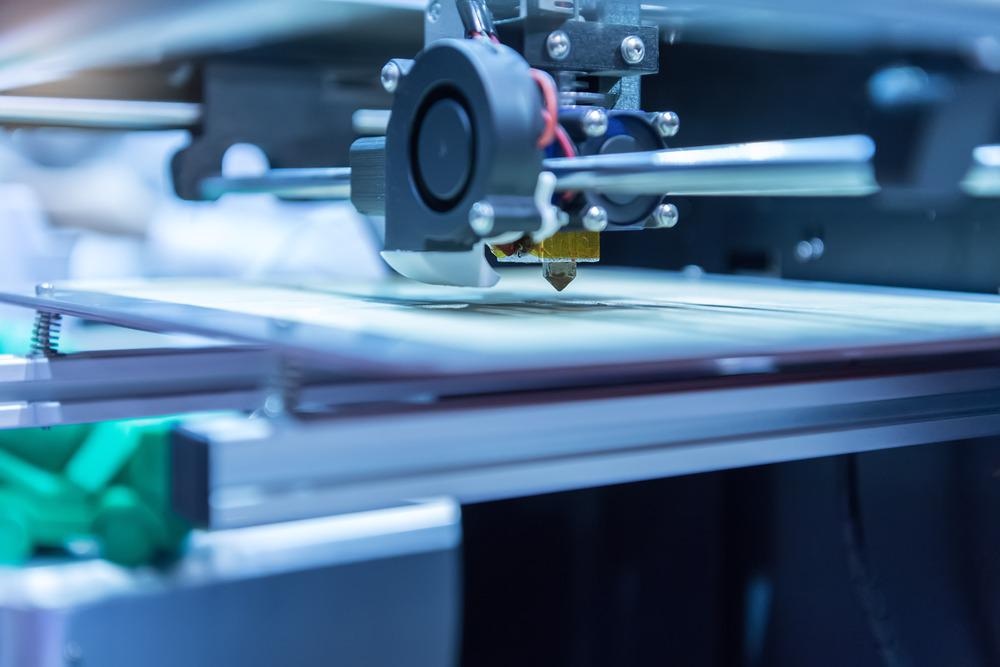
Image Credit: asharkyu/Shutterstock.com
Transparent materials with high-impact resistance are needed for a wide range of consumer products and safety-critical engineering applications. Many existing transparent impact-resistant materials have increased in toughness but often lack sufficient impact absorption properties. Using advanced additive manufacturing techniques, a research team at Polytechnique Montréal in Canada has created a transparent impact-absorbing composite material inspired by spider silk. The new composite material absorbs up to 96% of the energy under impact without losing integrity.
Spider silk is one of the toughest known biomaterials. It has evolved to dissipate enormous amounts of kinetic energy when arresting and retaining flying insects.
Spider webs dissipate up to 70% of the impact energy through molecular bond breaking within the silk threads' fine structure.
The silk fibrils consist of alternating nanocrystals and semi-amorphous domains. Upon impact, the hydrogen bonds within the semi-amorphous domains start to break, absorbing the energy and allowing the protein chains to uncoil and dissipate energy.
A research team from the Department of Mechanical Engineering at Polytechnique Montréal, led by professors Frederick Gosselin and Daniel Therriault, has succeeded in scaling up the molecular-level processes responsible for the remarkable strength and toughness of spider silk and replicating them on a microscopic scale.
Weaved by a 3D Printer
The researchers employed a sophisticated 3D printing technique called instability-assisted fused filament fabrication (IFFF). The scientists created an intricate plastic web that mimics spider webs by heating polycarbonate (a high-performance tough, amorphous, and transparent thermoplastic polymer) to 290 °C and extruding it into a millimeter-thick viscous filament.
Careful tuning of the 3D printing parameters, such as the velocity of the filament coming out of the printing head and the velocity of the deposition platform of the 3D printer, causes the filament to become unstable and buckle and twist due to compressive stress. This instability is known as liquid rope coiling and leads to the formation of regular circular coils.
By controlling the printer platform's motion onto which the viscous polycarbonate thread is being deposited, the scientists created a precisely positioned series of loops along each of the printed polycarbonate fibers. The IFFF process is repeated multiple times to create a series of weaved fibers a few millimeters apart.
The process is repeated by printing a new series of fibers perpendicularly to the original ones. The IFFF process is carried out rapidly, allowing the crossover regions of the perpendicular fibers and the loops to fuse as the polycarbonate solidifies.
The resulting continuous plastic web is then encased in a soft elastomer resin to obtain a transparent composite structure where the elastomer matrix further contributes to the mechanical and optical properties of the material.
Man-Made Web with Stunning Properties
The Canadian researchers' innovative concept was recently published in the Cell Reports Physical Science journal, together with detailed mechanical and optical testing of the novel impact-resistant composite. The results were impressive.
Impact tests and failure analysis demonstrated that 95.6% of the total impact energy is absorbed and dissipated. Only 4.4% is released as elastic energy, largely preserving the composite structure with minimal deformation.
Mimicking Nature with Polymer Fibers
The secret of the material's toughness is within its structure and is known as the sacrificial bonds and hidden lengths (SBHL) mechanism.
As professor Gosselin explains, the loops along the polycarbonate fibers act as sacrificial links that offer additional fiber strength. When an impact occurs, sacrificial links absorb energy by breaking and deforming and permit to maintain the fiber's overall integrity. The breakage of a sacrificial bond releases a so-called hidden length that unfolds and carries the load.
This happens in the same way as the sacrificial chemical bonds break within the spider silk strands, contributing to the energy required for the stretching and fracture of the molecular chain structure.
In the new composite material, the energy is further dissipated by fiber-matrix sliding, matrix cracking and segmentation, plastic deformation, and fracturing of the unfolding fiber. This ensures an efficient bidirectional SBHL toughening mechanism on a microscopic scale.
In addition to its mechanical toughness, the new composite exhibits excellent optical properties with a total optical transmittance of more than 90% averaged over the visible light spectrum. This is achieved by matching the refractive index of the polycarbonate fibers and the surrounding elastomeric matrix.
Promising High-Performance Fiber Composites for the Future
Professor Gosselin's team envisages a multitude of possible applications of the new transparent impact-absorbing composite. It can be used in laminated glasses and protective screens to improve energy dissipation under mechanical impact.
Other potential applications include bulletproof windows or aircraft and spacecraft windows.
Replacing the material components with other transparent or non-transparent high-performance engineering materials, such as polyether ether ketone (PEEK) and Kevlar fiber would pave the way for the creation of unbreakable plastic composites for the industry.
References and Further Reading
S. Zou, D. Therriault, F. P. Gosselin, (2020) Spiderweb-Inspired, Transparent, Impact-Absorbing Composite. Cell Reports Physical Science, 1, 100240. Available at: https://doi.org/10.1016/j.xcrp.2020.100240
R. Passieux, et al., (2015) Instability‐Assisted Direct Writing of Microstructured Fibers Featuring Sacrificial Bonds. Adv. Mater., 27, 3676-3680. Available at: https://doi.org/10.1002/adma.201500603
S. Chaudhari (2020) Researchers develop 3D printed spiderweb-inspired shatterproof material. [Online] www.3dprintingindustry.com Available at: https://3dprintingindustry.com/news/researchers-develop-3d-printed-spiderweb-inspired-shatterproof-material-179593/ (Accessed on 9 December 2020).
Polytechnique Montréal (2020) Printing plastic webs to protect the cellphone screens of the future. [Online] www.polymtl.ca Available at: https://www.polymtl.ca/carrefour-actualite/en/news/printing-plastic-webs-protect-cellphone-screens-future (Accessed on 9 December 2020).
Design Engineering (2020) Montreal engineers’ 3D printed webbing absorbs 96% of impact energy. [Online] www.design-engineering.com Available at: https://www.design-engineering.com/montreal-engineers-3d-printed-webbing-absorbs-96-of-impact-energy-1004035902/ (Accessed on 9 December 2020).
Disclaimer: The views expressed here are those of the author expressed in their private capacity and do not necessarily represent the views of AZoM.com Limited T/A AZoNetwork the owner and operator of this website. This disclaimer forms part of the Terms and conditions of use of this website.