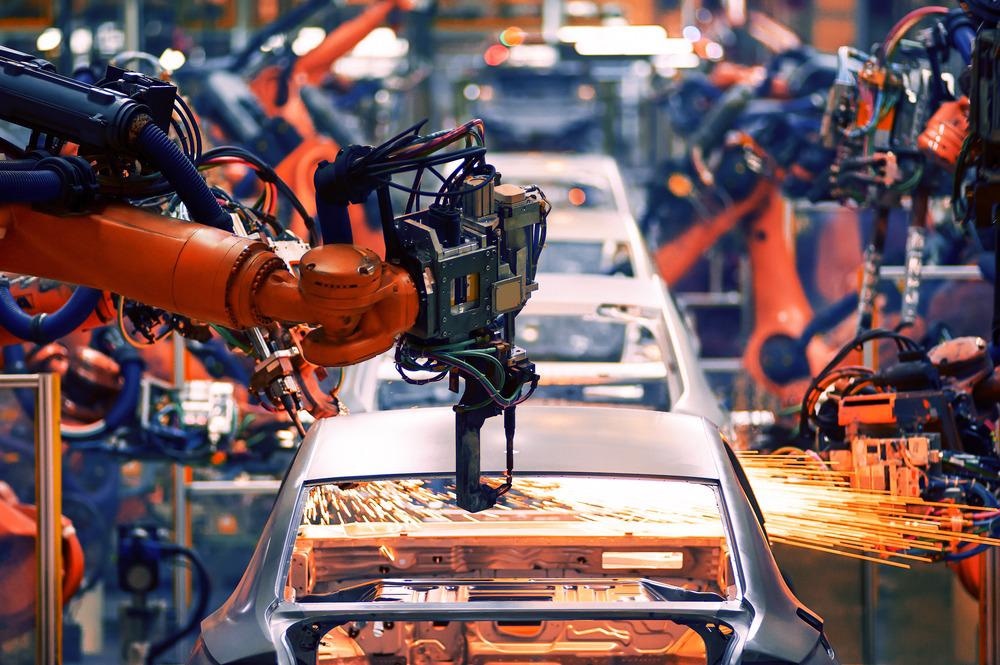
Image Credit: Jenson/Shutterstock.com
With support from the Baden-Würtemberg Think Tank project, the Karlsruhe Institute of Technology (KIT) and Audi have partnered to create a novel chemical recycling method for automatic plastic parts.
About the “Industrial Resource Strategies” Think Tank
The southwestern German state of Baden-Würtemberg has an exceptional potential for innovation due to its impressive technology production base, its history of efficiently using raw materials, and the significant investments that have been made in this region for research and development projects.
Some of the most notable institutions and universities that are located in Baden-Würtemberg include the Max Planck Institutes, the institutes of the Fraunhofer-Gesellschaft, and the universities of Stuttgart and Karlsruhe.
To support the potential for advancement in this area, the Baden-Würtemberg Council of Ministers set up a Think Tank for “Industrial Resource Strategies” in 2018. The Think Tank was initially developed to expand the efficient use of industrial resources, primarily raw materials, by creating a dialog between the region's industry and political entities.
To achieve this goal, the Think Tank strives to create a more holistic approach to each step of the raw material production process from extraction to use and finally ending with recycling any unused materials. Ultimately, the Think Tank will provide technological, economic, ecological, and social benefits to the residents of Baden-Würtemberg.
Automotive Plastics and Recycling
It is estimated that up to almost 40 different types of plastic materials will be used in automobiles due to their ability to reduce vehicles' weight by an average of 500 pounds.
In addition to resolving the need for lightweight and fuel-efficient vehicles, the advancement of thermoplastics such as polyamide, polyacetal and polycarbonate have also improved the tensile strength and heat resistance properties of certain automotive parts, especially when compared to traditional materials such as steel and aluminum.
Additional benefits associated with the use of plastic parts in automobiles include enhanced design freedom, better flexibility to integrate different components into the vehicle, corrosion and rust resistance, and improved safety and comfort for passengers.
Despite the fact that a modern automobile’s total volume is approximately 50% plastic, much of the auto recyclers' attention has been devoted to how the steel parts that are used in vehicles can be recycled. The lack of available recycling programs for automotive plastic and polymer composite components is mainly due to the high costs associated with recycling materials and the limited availability of adequate plastic recycling technologies. With over 27 million cars reaching the end of their useful lives each year, scientists must develop meaningful ways to recycle plastic automotive parts to reduce this industry's impact on the planet.
The KIT and Audi project
In late November of 2020, a joint effort between the Karlsruhe Institute for Technology (KIT), which is one of the largest research and educational institutions within Germany, and the German automobile manufacturer Audi has been announced for a chemical recycling program as part of the “Industrial Resource Strategies” Think Thank.
This pilot project, which has been titled the “Chemical Recycling of Plastics in Automotive Engineering,” aims to create smart circular systems for plastics and ensure that this method will complement the mechanical recycling and replacement of energetic recovery processes.
The initial steps of this joint effort will begin with a group of KIT scientists, led by Dr. Dieter Stapf at the Institute for Technical Chemistry (ITC) and Dr. Rebekka Volk at the Institute for Industrial Production (IIP), testing the technical feasibility of chemical recycling to determine the potential economic and environmental impacts of this method.
Audi will provide previously used automobile plastic components such as fuel tanks, wheel trim parts, and radiator grills, all of which will be converted into pyrolysis oil by chemical recycling.
High-quality pyrolysis oil can provide equally high-grade materials compared to when petroleum is used, demonstrating how perfecting this chemical recycling process can significantly reduce the automotive industry's dependence on fossil fuels.
Future Impact
Although plastic materials that are of the same type can easily be recycled, many of the plastic materials that are currently incorporated into automobiles are comprised of a mixture of plastic types. The chemical recycling of mixed plastic wastes has, therefore, remained a challenge for the automotive industry.
To improve the sustainability of their manufacturing processes, Audi’s joint project with KIT makes this automotive company the first to test this novel recycling method. The work that will be conducted during the course of the “Chemical Recycling of Plastics in Automotive Engineering” pilot project will allow Audi to gradually increase the proportion of secondary materials that are used in their models.
References and Further Reading
Technological diversity at a glance [Online] Available from: https://www.clusterportal-bw.de/en/cluster-data/technology-fields/.
Think Tank “Industrial Resource Strategies Inaugurated” [Online] Available from: http://www.kit.edu/kit/english/pi_2018_016_think-tank-industrial-resource-strategies-inaugurated.php.
Automotive Recycling Plastics Market Watch [Online] Available from: https://www.plasticsindustry.org/.
Audi and KIT are working on recycling for automotive plastics [Online] Available from: https://www.audi-mediacenter.com/en/press-releases/audi-and-kit-are-working-on-recycling-method-for-automotive-plastics-13358.
Disclaimer: The views expressed here are those of the author expressed in their private capacity and do not necessarily represent the views of AZoM.com Limited T/A AZoNetwork the owner and operator of this website. This disclaimer forms part of the Terms and conditions of use of this website.