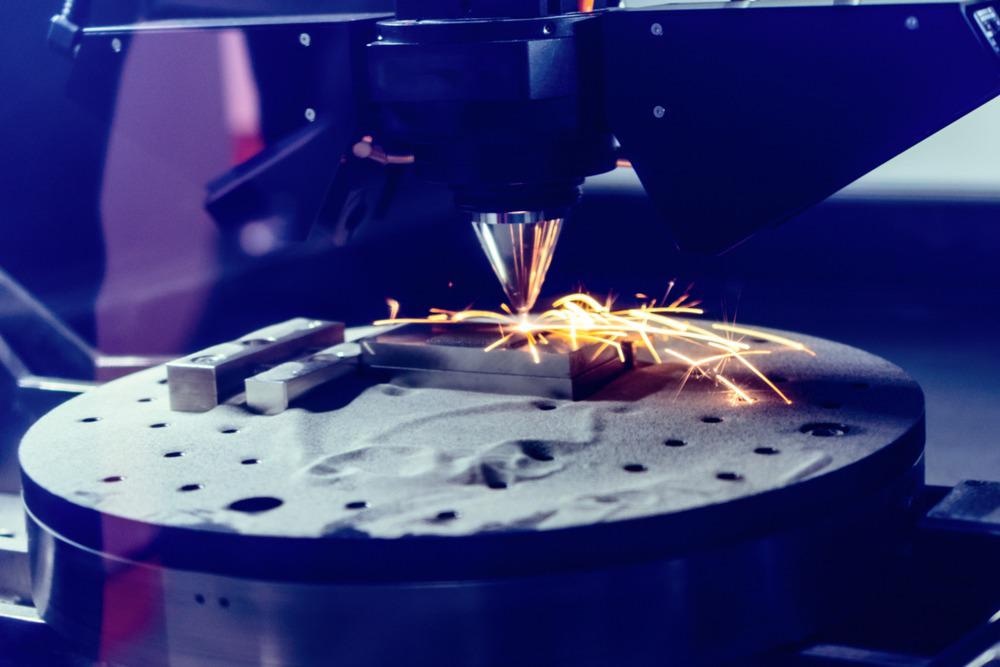
Image Credit: Nordroden/Shutterstock.com
Additive manufacturing has become increasingly popular in recent years as the technology has evolved and its applications in various industries have grown. A critical factor in ensuring the strength and reliability of components produced via additive manufacturing is each added layer's surface topography. Due to the increasing need for effective and reliable methods to evaluate surface metrologies, researchers have focused on developing non-contact methodologies of 3D surface metrology. One significant area of development has been strategies using optical probes. Here, we discuss the recent developments in this field.
The Advancement of Optical Probe Technology
The measurement of surface topography is vital in manufacturing. It has a significant impact on the look and function of the final products and informs quality control. Over the decades, many methodologies using various instruments have been developed to conduct surface topography measurements. However, they have varied in capabilities and limitations.
With the advent of additive manufacturing, a strong need for non-contact methodologies has developed. These methods prevent potential damage caused by the products being measured via contact with a measuring device.
Structured light techniques offer non-contact methods of 3D imaging surfaces. They use light to “probe” the visible surface of an object with illuminations that have recalculated spatiotemporal structures. As technology has advanced, computing devices and cloud sources have become more powerful and affordable. This has increased the demand and the development of these non-contact methods.
This article will review the most recent developments in non-contact methods of 3D surface metrology that utilize optical probes.
Microscale 3D Surface Profilometry
Labs worldwide use microscale optical interferometry to measure microscale structures. However, this technique is susceptible to external environmental factors such as air turbulence, temperature, and vibrations caused by the equipment. To overcome this, recent developments have focused on enhancing optical interferometry technology by updating the mechanisms to produce less noise in the results.
One methodology rapidly acquires the measurement data via the use of a high-speed camera in conjunction with fast phase-shifting. Another method creates a completely common-path arrangement with the two interference arms.
Time-of-Flight Surface Measurement
While time-of-flight (ToF) cameras have been around for several years, they have recently been a research focus, with projects succeeding to enhance their performance and expand their capabilities.
The light source used in ToF cameras sends multiple propagation paths (MPI) to the receiving pixel, causing a measurement error that has limited the use of traditional ToF cameras. In recent years, researchers have attempted to overcome this problem.
Scientists proposed the modeling of multiple paths as a direct and global return. The sampling of the received signal was then increased via modulation frequencies for signal separation. Finally, the concept known as phasor imaging was established. For frequencies higher than a certain scene-dependent threshold, no global effects are recorded. This concept allowed the recovering of depth even with multiple propagation paths. More recent work has expanded on this, obtaining the depth in the presence of fog and other scattering media.
Computational Imaging with Structured Light Techniques
Although established several decades ago, computational imaging (CI) has only recently been combined with other imaging techniques to produce enhanced measurement capabilities.
Artificial Intelligence for Structured Light Techniques
Machine learning (ML) has seen a surge of interest over recent years. Almost every scientific field is leveraging the technology, including the surface metrology sector. Recently, a new approach has been developed that enhances the quality of measurements far beyond that which is achievable with conventional methods.
ML has been successfully leveraged in methods of 3D surface measurement, improving the quality of phase unwrapping, high-speed profilometry, residual lens distortion correction, single-shot profilometry, robust ToF 3D imaging, and sensor fusion.
Automation
Skilled individuals are required to operate measurement instruments so that optimal exposures can be obtained. Recent developments have been made in automating this system so that cameras can be automatically adjusted to capture the correct exposures in a similar way that 2D cameras can be automated. While significant advances have been made, work continues to improve the automation of 3D surface measurement instruments.
Towards Large-Range Measurement
Several factors, including the arrangement of components, depth of field, power of the light source, speed of electronics, and type of projected pattern, can limit the depth of measurement range of almost all optical probe methodologies.
Research is currently underway to overcome these challenges. Notably, microscopic systems and triangulation-based techniques are being developed to reduce the impact of these limitations.
Conclusion
3D surface metrology methods that utilize optical probes are the most reliable techniques for obtaining non-contact 3D measurements. While there are many challenges to these techniques, many significant advancements help overcome these limitations and expand the capabilities of these measurement techniques.
References and Further Reading
Hocken, R., Chakraborty, N. and Brown, C., 2005. Optical Metrology of Surfaces. CIRP Annals, 54(2), pp.169-183. https://doi.org/10.1016/S0007-8506(07)60025-0
Marrugo, A., Gao, F. and Zhang, S., 2020. State-of-the-art active optical techniques for three-dimensional surface metrology: a review [Invited]. Journal of the Optical Society of America A, 37(9), p.B60. https://doi.org/10.1364/JOSAA.398644
Zhang, S., 2018. Absolute phase retrieval methods for digital fringe projection profilometry: A review. Optics and Lasers in Engineering, 107, pp.28-37. https://doi.org/10.1016/j.optlaseng.2018.03.003
Disclaimer: The views expressed here are those of the author expressed in their private capacity and do not necessarily represent the views of AZoM.com Limited T/A AZoNetwork the owner and operator of this website. This disclaimer forms part of the Terms and conditions of use of this website.