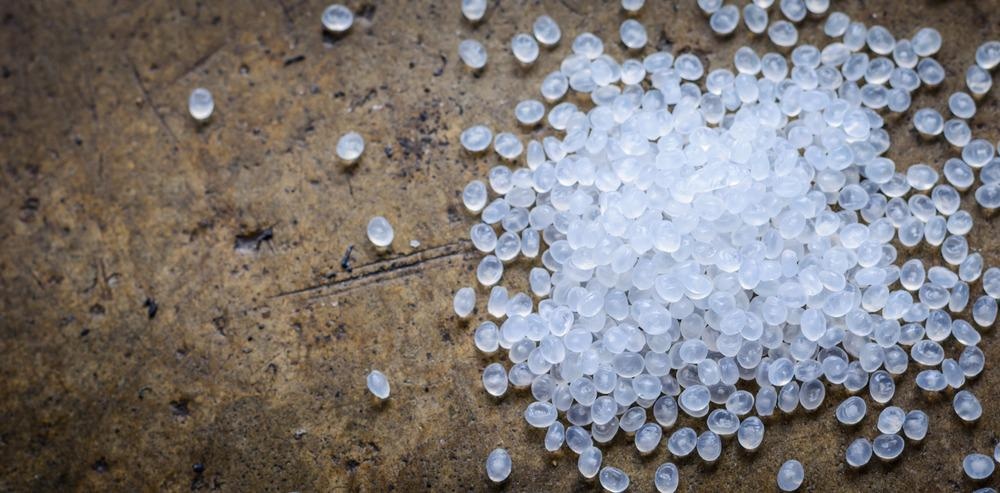
Image Credit: phidsanu suriyawong/Shutterstock.com
Knowing the physical and chemical properties of polymeric materials is essential for developing efficient material processing methods for the manufacturing and recycling of plastic products. This information is vital when predicting material performance during a product's lifetime or troubleshooting when a material does not perform as expected.
Thermal properties or how the material's temperature affects its physical and chemical properties are particularly important for polymers' industrial applications. These are crucial when establishing the optimal processing temperatures for curing, injection molding, and extrusion or heat welding.
Furthermore, polymers' thermal properties can provide valuable information when conducting failure analysis, determining the thermal stability, or the aging properties of plastic products.
According to their thermo-mechanical properties, the polymers can be classified into thermoplastics, thermosets, and elastomers.
Thermoplastics are amorphous or semi-crystalline polymers that soften (or melt) when heated and become solid when cooled down. The heating and cooling cycle can be repeated without discernible changes in the thermoplastics' thermal and mechanical properties.
Thermosets undergo irreversible chemical crosslinking upon heating, while the elastomers can be weakly crosslinked (usually by a heat-assisted vulcanization process), making them reversibly stretchable for relatively small deformations.
Thermo-Mechanical Properties of Advanced Polymeric Materials
Most modern plastics are complex compounds consisting of different polymers and additives. The final products' overall properties depend on the chemical and physical properties of the components and the processing methods used during fabrication.
For such complex polymeric materials, accurate analysis of the thermal properties can help identify the material's composition, measure crystallinity or degree of crosslinking, and estimate the additives’ (such as plasticizers, fillers, and processing aids) effects.
Thermal analysis is an analytical method where the physical properties are measured as a function of temperature. Amongst the wide range of thermal analysis techniques, the differential scanning calorimetry (DSC) technique is probably the most widely used thermal analysis technique in polymer science.
Basic Principles of DSC Analysis
DSC quantitatively determines the amount of heat absorbed or released by a sample, compared to a reference, during a specific thermal transition in the tested polymeric material. The changes occurring in the samples' thermal properties can be measured isothermally as a function of time or at a constant heating or cooling rate as a function of temperature.
These changes in the thermal properties of the material under investigation may be of chemical or physical origin. Thus, the DSC technique is beneficial when studying polymers because the polymers' long macromolecules' structural changes are almost always accompanied by variations in the molecules' thermal energy. This means that fundamental processes, such as polymerization, crystallization, melting, glass transition, and crosslinking, show characteristic patterns in the DSC data.
Variants of the DSC Technique
There are two widely used variants of the DSC technique: the heat flux DSC and the power compensated DSC.
Power Compensation DSC
The power compensation analytical instruments consist of two separate adiabatic ovens where a few milligrams of the sample material and reference material are placed within sealed aluminum pans. The typical reference material is air (an empty pan) or another material with well-known thermal properties, such as platinum. Each oven is equipped with a resistance heater and a thermocouple. Power is supplied to both ovens at the same time to increase the temperature linearly with time.
The thermocouples monitor the temperatures of the sample and the reference. During measurement, the DSC instrument identifies the power (heat energy per unit time) differential between the sample and the reference while maintaining zero temperature difference between the two during programmed heating and cooling temperature scans. While the sample undergoes a phase change or a thermal transition, the power needed to compensate for the temperature difference is directly proportional to the amount of heat absorbed or released from the sample.
Heat Flux DSC
In the heat flux DSC setup, the pans containing the reference and the sample are placed inside a single oven. Each pan's temperatures are carefully measured as power is supplied to produce a linear temperature increase at a constant heating rate.
In this case, the temperature difference resulting from the sample's thermal transition is proportional to the heat transferred to or from the sample.
Due to their high sensitivity, the power compensation calorimeters are an excellent academic and industrial research study tool. However, they are not easy to calibrate and often present baseline stability problems.
Heat flux calorimeters are more robust and offer improved baseline stability. Such instruments are suitable for quality control and high throughput routine measurements.
Typically, the scanning calorimeters operate at heating/cooling rates of 50-100 °C per minute (with samples of a few tens of milligrams).
In recent years, significant developments enabled the production of scanning calorimeters to perform analysis at heating or cooling rates in the range of 500-30,000 °C per minute. Such fast heating/cooling rates can be achieved with specially designed fast chip calorimeters, where the mass of the sample is reduced to the micrograms or even the picograms range to facilitate heat transfer.
DSC Enables Comprehensive Characterization of Polymeric Materials
In both configurations, with suitable calibration, DSC measurements at constant scanning rates can be employed to determine first- and second-order thermodynamic quantities of amorphous or semi-crystalline polymers.
Thermal Properties of Polymeric Materials
The changes in the material's thermal properties usually arise from first- and second-order transitions.
Melting and Crystallization
First-order thermodynamic transitions can absorb (melting) or release energy (crystallization, polymerization reactions) and give rise to endothermic or exothermic peaks.
The peaks' position determines the melting (Tm) or crystallization (Tc) temperature of the sample. The area under the endothermic or exothermic peaks represents the enthalpy change (the amount of heat evolved or absorbed at constant pressure) associated with melting or crystallization.
The higher the enthalpy change value is, the more crystalline the polymer is. Therefore, it is possible to estimate the degree of crystallinity present in the polymeric material.
Heat Capacity and Glass Transition
Conversely, the second-order thermodynamic transitions do not cause changes in the enthalpy and do not give origin to endothermic or exothermic events. The second-order transitions (glass transition, for example) only alter the sample heat capacity (and the DSC scan baseline position).
The heat capacity (Cp) of material at constant pressure represents the amount of heat needed to raise its temperature by one degree Celsius per unit weight. It can be derived from the heating rate and the amount of heat supplied to the sample.
If the Cp of material is constant over a temperature range, then the DSC scan (supplied heat versus temperature) will be a line with a zero slope.
If a polymer in a molten state is cooled below its glass transition temperature (Tg), the polymer changes mechanical properties (from elastic to brittle) due to the reduced macromolecular chain mobility. The polymer's heat capacity is different below and above Tg, making DSC a valuable method for the determination of Tg. The glass transition usually occurs over a range of temperatures, and the temperature in the middle of the range is considered as Tg.
Polymer Blends Composition Studied by DSC
Polymer blends are mixtures of two or more polymers combined to produce new materials with enhanced properties.
Thermal analysis is an essential tool for developing polymer blends, particularly when assessing the miscibility of the blend's components. A polymer blend is considered miscible if it exhibits only a single Tg lying in a temperature range intermediate to the Tg of the blend's original components.
If the blend exhibits two or more Tg values (but displaced relative to the Tg of the pure components), it is considered to be partially miscible. In this case, each Tg corresponds to a mixture containing different amounts of each element.
Finally, immiscible polymer blends exhibit the same glass transition temperatures as the pure components.
For semi-crystalline polymer blends, the blend's melting temperature and the melting enthalpy may also be employed to study the miscibility of the components and the phase separation of the blend.
Thermal Characterization of Advanced Composite Materials
Composites are materials formed of two or more components with different physical or chemical properties. These remain separate and distinct within the final structure. Composite materials usually offer improved mechanical properties compared to the source materials and are widely used in diverse industrial applications.
Studying the thermal properties and the thermodynamic transitions in the composite materials determines the material's morphology. For example, melting endotherms can be employed to estimate the crystallization of the binding (resin) phase of the composite material.
Crystallization exotherms can reveal possible structural changes in the polymer phase after the fabrication of the composite material. The mechanical properties of the composites are usually directly related to the crystallinity of the polymer phase. Parameters such as melting point, glass transition, and melting enthalpy can be employed to determine the interaction between the constituent phases of the composite materials and to predict their properties.
Designing polymeric materials with optimal thermal and mechanical properties is critical for cost-efficient production and long product life. The ability to correlate polymeric material's thermal properties to its morphology and mechanical properties makes DSC an essential tool for the development and characterization of industrial plastics, polymer blends, and composites.
References and Further Reading
G.S. Martins (2020) Differential Scanning Thermal Analysis of Shape-Memory Polymers, Polymer Blends and Composites, in Shape Memory Polymers, Blends and Composites. Advanced Structured Materials, vol 115, J. Parameswaranpillai, S. Siengchin, J. George, S. Jose (Eds) Springer, Singapore. Available at: https://doi.org/10.1007/978-981-13-8574-2_7
A. J. Müller and R. M. Michell (2016) Differential Scanning Calorimetry of Polymers, in Polymer Morphology: Principles, Characterization, and Processing, pp 72-99, Q. Guo (Ed.), John Wiley & Sons Inc. Available at: https://doi.org/10.1002/9781118892756.ch5
M. J. Richardson (1989) Thermal Analysis, in Comprehensive Polymer Science and Supplements, 1, 867-901, G. Allen, J. C. Bevington (Eds), Pergamon, Available at: https://doi.org/10.1016/B978-0-08-096701-1.00036-7
Disclaimer: The views expressed here are those of the author expressed in their private capacity and do not necessarily represent the views of AZoM.com Limited T/A AZoNetwork the owner and operator of this website. This disclaimer forms part of the Terms and conditions of use of this website.