Additive manufacturing (AM), often known as 3D printing, is gaining popularity as a feasible technology for prototyping and for components with highly customized complicated structures. The article discusses the thermal treatment of 3D-printed components.
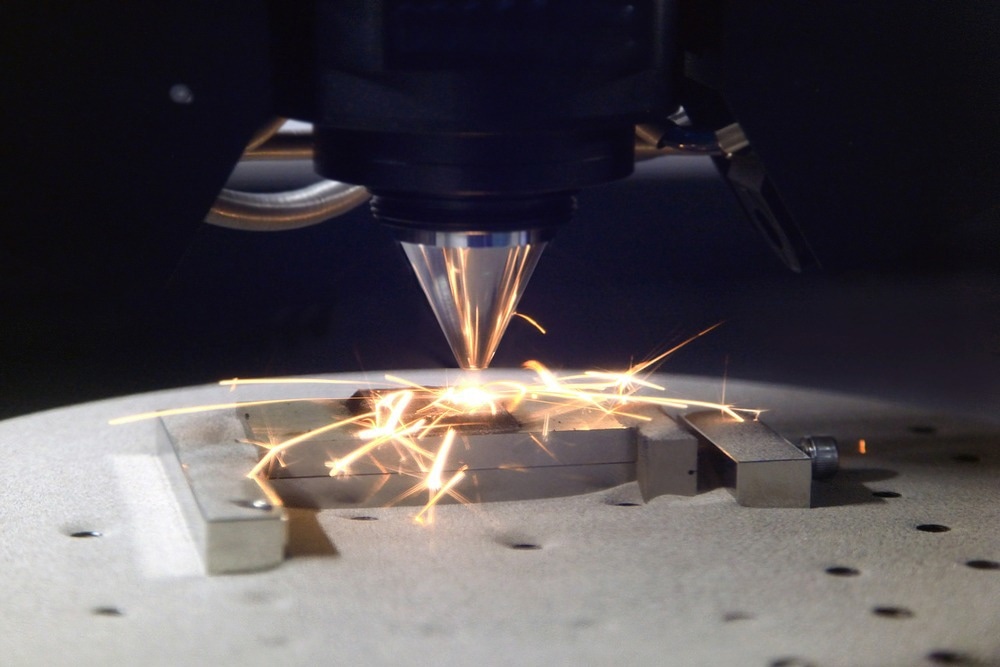
Image Credit: sspopov/Shutterstock.com
Effects of Thermally Treating 3D Metal Components
Metal 3D printed elements typically always undergo thermal treatment after their fabrication. It reduces the internal stresses formed during manufacturing and modifies the morphology of the element. This modification of the microstructure alters certain attributes such as toughness, hardness, etc.
The thorough densification of 3D-printed metal components to eliminate porosity leading to catastrophic failures requires a special thermal treatment called hot isostatic pressing (HIP).
The HIP procedure entails depositing the 3D fabricated item within a pressure vessel and then filling it with an inert gas, usually argon. Along with the pressure, very high temperatures are maintained concurrently, surpassing the component’s yield strength. Through fast quenching, an even more sophisticated variant of HIP employs adjustable cooling and heating speeds and pressure levels to accurately regulate the quality and tensile attributes of the processed components.
What Does Heat Treatment Do For Polymeric 3D Printed Parts?
Various complex geometries are accurately fabricated via 3D printing technologies; however, it has a major disadvantage which necessitates thermal post-treatment. These 3D printed parts have inferior mechanical properties as compared to those produced via injection molding. Insufficient adherence between coated filaments and stacked layers causes the poor mechanical characteristics of 3D-printed components.
The latest research published in the journal Polymers focuses on the enhancement of mechanical properties, specifically tensile and compressive strengths. The researchers utilized PETG undyed filament of diameter 1.75 mm. The results showed that a significant increase in tensile strength was observed for polymeric 3D-printed components.
Heat-treated components had considerably superior tensile strength, with completely treated parts having 41.1% more strength than the untreated specimen in a horizontal position and 143.9% greater strength than the control group in a vertical orientation. The thoroughly thermally processed horizontally aligned samples had a 13.3% increase in Young's modulus of elasticity and a 22.1% higher Young's modulus of elasticity.
Destructive compressive testing reveals a considerable escalation in the value of compressive strength, with heat-treated specimens attaining compressive stresses of up to 118 MPa.
In short, the study successfully revealed the positive effects of post-manufacturing thermal treatment of polymeric materials.
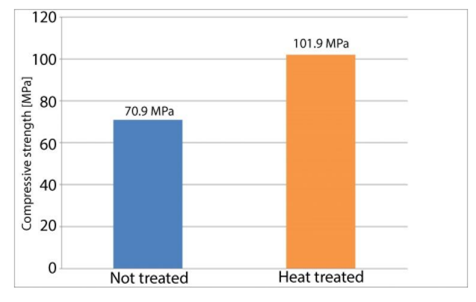
Sample Averages of Compressive Strengths. Study: Enhancing Mechanical Properties of Polymer 3D Printed Parts
Heat Treating 3D-Printed Polypropylene Parts for Vacuum Systems
The latest research in the Journal of Manufacturing and Materials Processing investigates the feasibility of applying a post-processing heat treatment process to encapsulate 3D-printed polypropylene in vacuum conditions. Heat treatment was found to be very effective for the encapsulation process.
Thermal processing reduced the minimum pressure attained by each overlap by more than half. The maximum overlap and thermal treatment yielded the best performance. The average for the 15 iterations of parts printed with 98% infill overlap and sealed after heat treatment was 0.4 m Torr, with a 95% confidence interval of 0.2 m Torr.
It was discovered that using a heat gun set to 400 degrees Celsius for 55 seconds to seal the surface susceptible to vacuum was successful and improved the minimal vacuum pressure achieved. These results confirmed the suitability of 3D-printed parts for vacuum systems.
Does Heat Treatment Affect the Dimensional Stability of 3-D Printed Components?
Researchers have published a study in Composites Part A exploring the impact of thermal processing on the stability and tensile performance of 3D-printed continuous carbon fiber (CCF) reinforced composites. The morphological alterations and dispersion of printed layers were used to assess the dimensional stability of samples. The 3D-printing technology is founded on the fused filament fabrication (FFF) approach, referred to as continuous filament manufacturing (CFF).
C-CCFRC and S-CCFRC, respectively, were the designations used for samples reinforced with concentrated CCF layers and separated CCF layers. After thermal processing at 100°C and 150°C, the CCFRCs had superior tensile properties, although dimensional stability was superior at 100°C, notably for S-CCFRC. Matrix crystallinity rose by 30.65% from 17.42% in the untreated samples to 22.76% in the samples after 100 C thermal treatment.
Thermal treatment at 100°C and 200°C decreased the permeability of the specimen. Matrix's lower permeability tendency following thermal processing was commensurate with its dimensional shift. Hence, thermal treatment up to 100°C increased the dimensional stability of the samples.
Effects of Thermal Treatment on Poly Lactic Acid Parts
Fused deposition modeling (FDM) is a popular additive manufacturing technology, with polylactic acid (PLA) being the most widely used material. The researchers assessed the properties of PLA parts via 3 points bending test after heat treatment and by varying the build orientation, layer thickness, and speed in the latest study published in Polymers.
1.75 mm diameter PLA filament was used for 3D printing. An x-z manufacturing configuration, a nozzle temperature of 190°C to prevent specimen breakage, a manufacturing speed of 90 mm/s, and a coating thickness of 0.3 mm were the best of the evaluated parameters.
Heat post-treatment at 75°C was applied to specimens manufactured with these settings, resulting in a slightly enhanced maximum force at bending. Finally, the results showed that elastic deformation and recovery during thermal processing did not considerably limit maximum forces.
This allows for the flat 3D printing of orthoses and then twisting them to match the desired area of the human body.
To summarize, heat treatment is useful for enhancing mechanical characteristics and improving the dimensional stability and optical characteristics of 3D-printed parts.
More from AZoM: What Raw Materials are Used to Make Mobile Phones?
References and Further Reading
Mayville, P.J et. al. (2022). Thermal Post-Processing of 3D Printed Polypropylene Parts for Vacuum Systems. J. Manuf. Mater. Process. 6. 98. Available at: https://doi.org/10.3390/jmmp6050098
Chalgham, A. et. al. (2021). Mechanical Properties of FDM Printed PLA Parts before and after Thermal Treatment. Polymers 13. 1239. Available at: https://doi.org/10.3390/polym13081239
Wang, K. et. al. (2021). Heat-treatment effects on dimensional stability and mechanical properties of 3D printed continuous carbon fiber-reinforced composites. Composites Part A: Applied Science and Manufacturing. 147. 106460. Available at: https://doi.org/10.1016/j.compositesa.2021.106460
Amza, C.G. et. al. (2021). Enhancing Mechanical Properties of Polymer 3D Printed Parts. Polymers. 13. 562. Available at: https://doi.org/10.3390/polym13040562
Disclaimer: The views expressed here are those of the author expressed in their private capacity and do not necessarily represent the views of AZoM.com Limited T/A AZoNetwork the owner and operator of this website. This disclaimer forms part of the Terms and conditions of use of this website.