In recent years, the use of Phase Change Materials (PCMs) in thermal management systems (TMS) has garnered increased interest due to their high latent heat storage capacity, which enables effective thermal energy management. The combination of Phase Change Materials (PCMs) with Metal Foam (MF) offers a viable alternative for enhanced thermal profitability in heat sink operations.
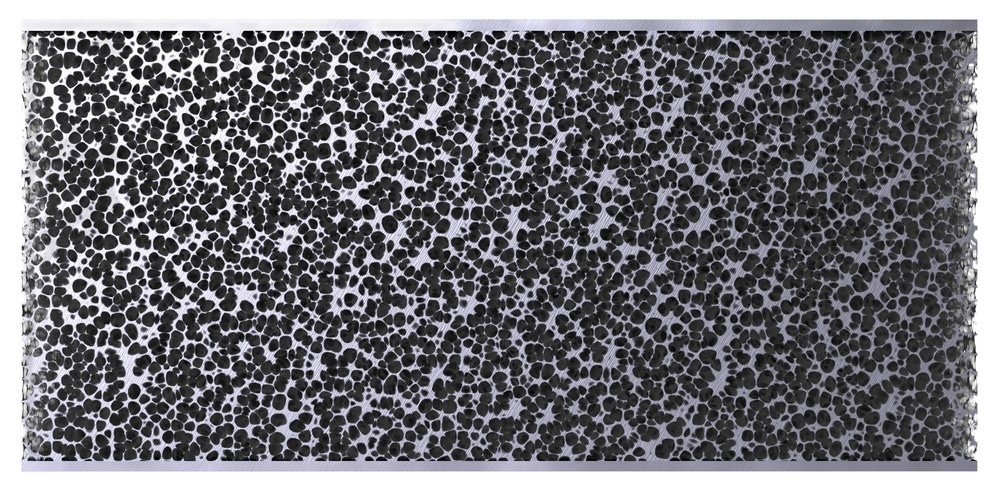
Image Credit: Peter Sobolev/Shutterstock.com
Phase change materials (PCMs) are a family of thermo-responsive materials that may be used to induce a phase shift, therefore storing thermal energy. Phase change materials (PCMs) possess the capacity to absorb and release thermal energy throughout the phase change process. During the phase transition process, the material changes from a solid to a liquid or from a liquid to a solid state, releasing or absorbing latent heat. This means that PCMs can store thermal energy as latent heat, allowing for efficient thermal control.
The continuous miniaturization of electronic equipment without compromising performance has rendered the challenge of hot spot mitigation increasingly difficult. Excessive heat output shortens the lifespan of electrical equipment. Hence, efficient thermal management solutions are essential to increase the dependability and safety of this equipment. Passive cooling solutions do not require external electricity to work and have no moving parts, therefore minimizing the system's complexity. Phase change material (PCM) cooling is one of these potential passive cooling techniques.
Importance and Industrial Utilization
High heat capacity, chemical stability, non-corrosive nature, non-toxicity, minor volume fluctuations, and a low melting point are characteristics that favor the use of PCM. PCM is further distinguished by its weak thermal conductivity, which results in a sluggish heating and cooling process.
PCMs are essential for a range of industrial applications, including heat energy storage and management, thermoregulation, and cooling equipment. PCMs are beneficial in instances where the temperature of a system or component must be regulated without the need for active cooling, such as in electrical devices, structural insulation, and conditioning systems. PCMs are also utilized to store thermal energy for later use in energy storage technologies, such as solar thermal power plants.
A Brief Introduction to Metal Foam (MF)-Phase Change Materials (PCM)
Typical approaches for increasing the thermal conductivity of PCM include composite PCM, micro-capsulation, nanomaterial augmentation, and fins. Metal foams and metal matrixes are examples of organic-inorganic (metal) materials. Many studies have been performed to assess the cooling efficiency of a variety of heat sink layouts. According to reports, metal foam/PCM-based heat sinks are better suited for a broad spectrum of heat flux operating situations.
Metal foams are porous, poor thermal transmittance materials with a high surface area-to-volume ratio. When coupled with PCMs, the resultant composite structures exhibit increased thermal energy storage capacity and thermal conductivity, making them perfect for heat sink applications.
Which Factors Affect the Performance of Metal Foam-PCM Composite Heat Sinks?
Several variables affect the thermal performance of the MF-PCM composite heat sink, such as the conductivity of the metal foam, the specific heat of the PCM, the melting and solidification temperatures of the PCM, the amount of PCM, and the operational parameters of the system.
The thermal conductivity of the metal foam influences the rate of heat movement inside the composite material, whereas the thermal conductivity and specific heat of the PCM dictate its energy storage capacity. The PCM's melting and solidification temperatures dictate the temperature range across which it can store and release thermal energy effectively. The amount of PCM in a composite material influences its thermal energy storage capacity and the pace at which thermal energy may be absorbed or released. The ambient temperature and other operational parameters play an essential role in determining performance. Consequently, it is essential to consider these elements while developing and improving the heat sink's performance.
The rate of heat transfer between the metal foam and PCM is an additional crucial aspect affecting the performance of the MF-PCM composite heat sink. This may be improved by increasing the ratio of surface area to volume of the composite material and enhancing the thermal contact between the metal foam and PCM. Using a PCM capable of entering the pores of the metal foam can increase the effective contact area and enhance the rate of heat transfer, hence enhancing the thermal contact.
Latest Research
Researchers have published a research article in the International Journal of Heat and Mass Transfer investigating the impact of ambient circumstances and phase change material (PCM) selection on the thermos-physical properties of a metal foam (MF)-PCM composite heat sink. The PCMs investigated are paraffin wax (PF), docosane (DOC), and eicosane (EIC), and their respective melting temperature ranges were 44.5 – 60.1 °C, 40.3 – 44.5 °C, and 36.3 – 38.1 °C.
Utilized as a cuboid-shaped, aluminum alloy heat sink with an interior hollow to hold the PCM-MF composite, up to 20 mm of metal foam (copper (Cu) and aluminum (Al)) soaked with PCM was inserted within the heat sink's hollow.
Compared to a heat sink filled with solely PCM (PF), the composite heat sinks (PF-MF-Al/Cu) reduced the peak temperature by a maximum of 15.1%. It was discovered that an increase in ambient temperature greatly increased the maximum temperature obtained by the heat sink.
In the absence of an auxiliary cooling system, at peak operating temperatures over 60 °C, PF-MF-Cu was chosen because of its similar peak temperature to DOC-MF-Cu and its adaptability for numerous charge-discharge cycles.
Future Perspective
The use of composite Metal Foam (MF)-Phase Change Material (PCM) heat sinks offers a viable alternative for increased thermal performance in several industrial applications. Metal Foam (MF)-Phase Change Materials (PCM) composite heat sinks will undergo additional development and use in the future. This may involve the use of innovative materials and processes to improve the heat transfer and energy storage capacity of composite materials, as well as the implementation of novel solutions for this technology in fields such as sustainable transportation and energy.
More from AZoM: Printing 3D Objects with Multiple Acoustic Holograms
References and Further Reading
Sreenath, V. R., & Chanda, S. (2023). Thermal performance evaluation of PCM-MF composite heat sinks under varying ambient conditions. International Journal of Heat and Mass Transfer, 206, 123927. Available at: https://doi.org/10.1016/j.ijheatmasstransfer.2023.123927
Croda (2023). Phase Change Materials. [Online] Available at: https://www.crodaenergytechnologies.com/en-gb/functions/phase-change-materials#:~:text=Phase%20change%20materials%20are%20substances,significant%20amount%20of%20heat%20energy.
Zare, M., & Mikkonen, K. S. (2023). Phase Change Materials for Life Science Applications. Advanced Functional Materials, 2213455. Available at: https://doi.org/10.1002/adfm.20221345
Disclaimer: The views expressed here are those of the author expressed in their private capacity and do not necessarily represent the views of AZoM.com Limited T/A AZoNetwork the owner and operator of this website. This disclaimer forms part of the Terms and conditions of use of this website.