By Susha Cheriyedath, M.Sc.Reviewed by Skyla BailyNov 18 2021
Researchers recently used oil as an ‘entrance door’ for loading rubber with carbon fillers of various sizes and dimensionalities, including 1D carbon nanotubes (CNTs), 2D graphene nanoplatelets (GNPs), and 3D graphite. In an article published in the journal Nanomaterials, they explored this approach as a proof of concept in the production of tire tread.
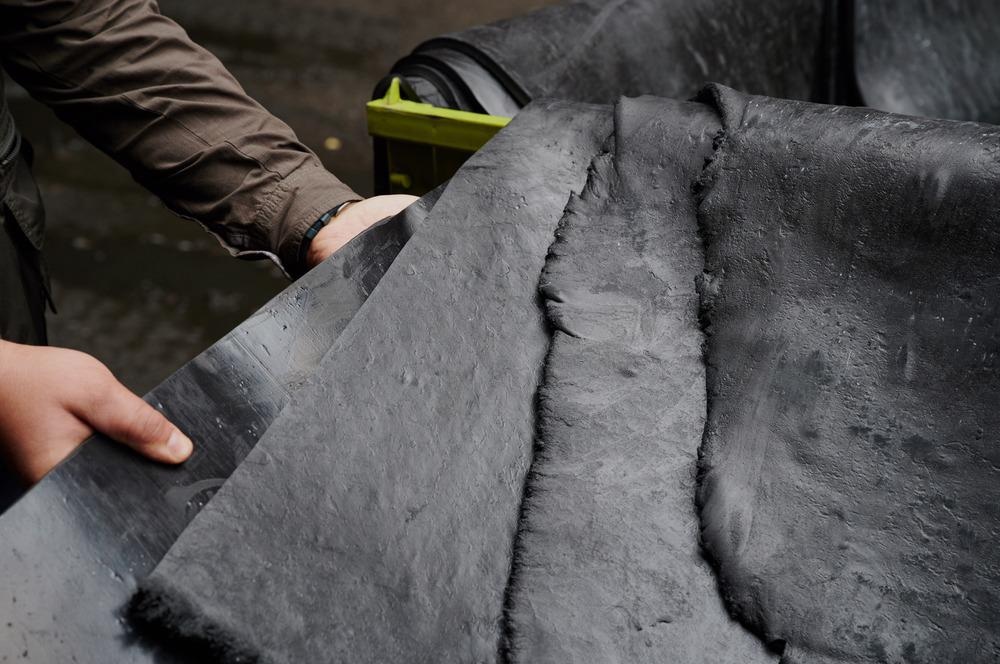
Study: Disperse-and-Mix: Oil as an ‘Entrance Door’ of Carbon-Based Fillers to Rubber Composites. Image Credit: Akimov Igor/Shutterstock.com
Carbon Fillers
In tires/tires manufacturing, the tread performance depends on the mechanical and thermodynamic properties of composite rubber. The compound comprises synthetic rubber, sulfur (for vulcanization), and additives such as carbon fillers, antioxidants, and oil as binders.
The carbon fillers play a key role in tread extrusion for they reduce the viscosity of the rubber for molding. They are critical to the enhancement of Young's modulus for elasticity, thermal conductivity (TC) for heat dissipation due to friction, tensile strength for tread endurance, elongation at break to withstand impact deformations, and abrasion resistance that increases the life of the tread.
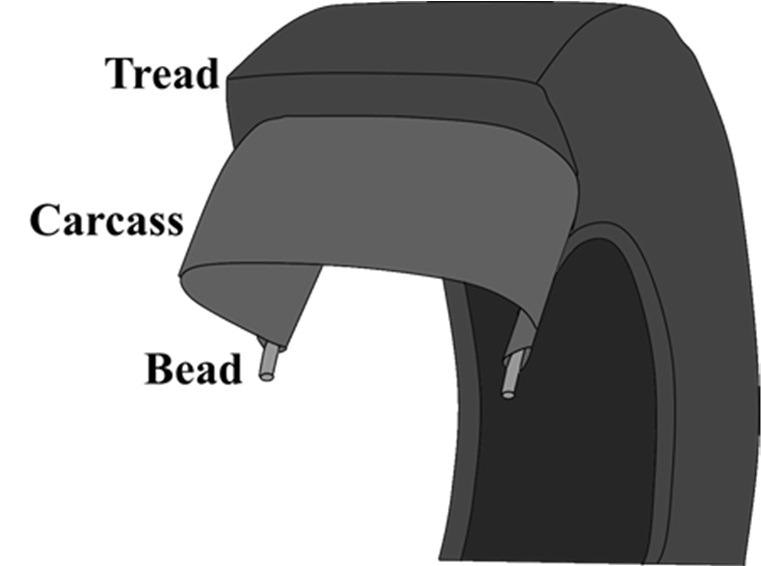
The major components of a tire include bead, carcass, and tread. Image Credit: Gal Shachar Michaely et al., Nanomaterials
Traditional fillers utilized in tread making are carbon black (CB) in combination with silica mixed into the synthetic rubber mix. Structurally, CB atom bonds comprise of sp2 & sp3 hybridization that often causes pores on surfaces.
As a result, only a limited surface is available for bonding with the long-chain polymers that rubber comprises. To alleviate this shortcoming, more CB needs to be added, which results in increased weight of the product. Weight increase leads to the compromise of mechanical properties of the rubber compound that result in fatigue failures.
The Study
The present study revealed that nano-sized fillers such as carbon nanotubes (CNT), graphene nanoplatelets (GNP), and micron size graphite are better fillers in comparison to CB. All the 3 have similar atomic bonding through sp2 hybridization.
This enables them to react with synthetic rubber more effectively due to the complete availability of the reactive surface for bonding. Thus, the total fill can be achieved without bottles, pores, or dead-ends with long polymer chains (in rubber) with the right orientation unlike in CB. This was verified using scanned electron microscopy to study the composite rubber mix.
All three carbon fillers (CNT, GNP, and graphite) were added individually or in combined forms and then pressure bonded to the synthetic rubber after a blending process using oil.
A comparative study of the mixture of either individual nanosize fillers (NF such as CNT and GNP) or in a combination of two or more mixtures was done as part of the research. The material with an ideal total filler weight fraction was identified as CNT (NF). As a result, a lesser quantity of material is required with lower product weight and greater mechanical property advantages.
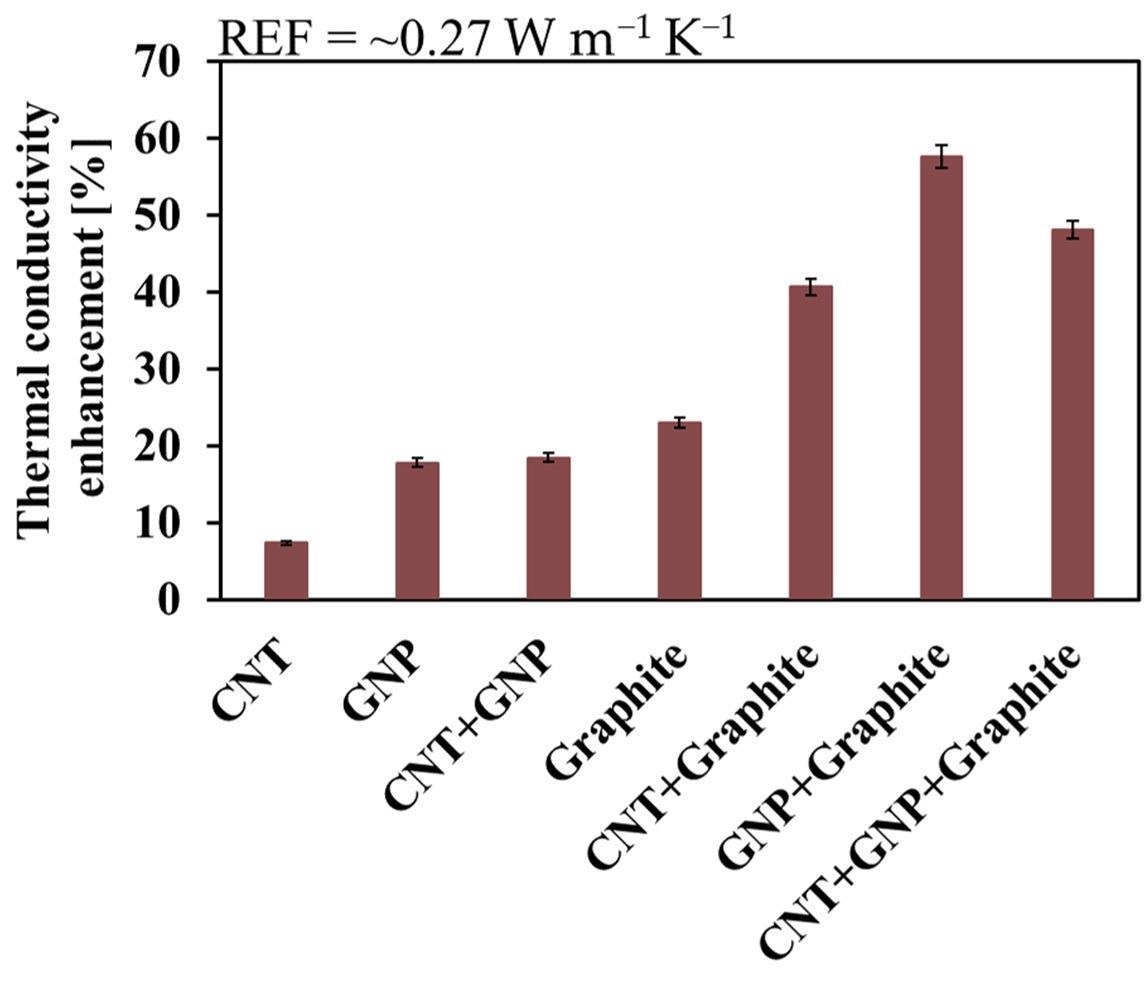
Thermal conductivity enhancement of the various systems. Image Credit: Gal Shachar Michaely et al., Nanomaterials
Comparison of the Three Carbon Fillers
Although graphene (GNP) + graphite (3D) offers high tensile strength to rubber composites with a modulus value of 1.2 Tpa (Tera pascals), CNT enhances the mechanical properties more than its fellow carbon fillers on most parameters.
Multiwalled graphene (GNP) is known to be the strongest material that gives the filler thermodynamic and mechanical strength. Graphene (MWCNT) is known for its elasticity and is more than 40 times stronger than diamond and 200 times stronger than steel as per the ASTM E1820 for durability in extreme temperatures.
The higher thermal conductivity of the material allows for better heat dissipation caused by an enormous amount of friction during surface contact. Among the three nanosize fillers, the CNT had the best overall relative efficiency (ORE) score followed by GNP and graphite. The combination of GNP with graphite yielded the best TC enhancement up to 58%, however when added in combination with graphite the enhanced mechanical properties were limited.
A defect-free single sheet of graphene is impermeable to gases thereby enhancing its insulating property. It not only offers enhanced thermal conduction but when combined with graphite it also exhibited very high tensile strength and abrasion resistance. Tensile elasticity is the highest when all three fillers - CNT, GNP, and graphite - are blended.
However, the presence of graphite reduces the mechanical enhancements owing to its micron size and a higher total filler-weight fraction (TFF).
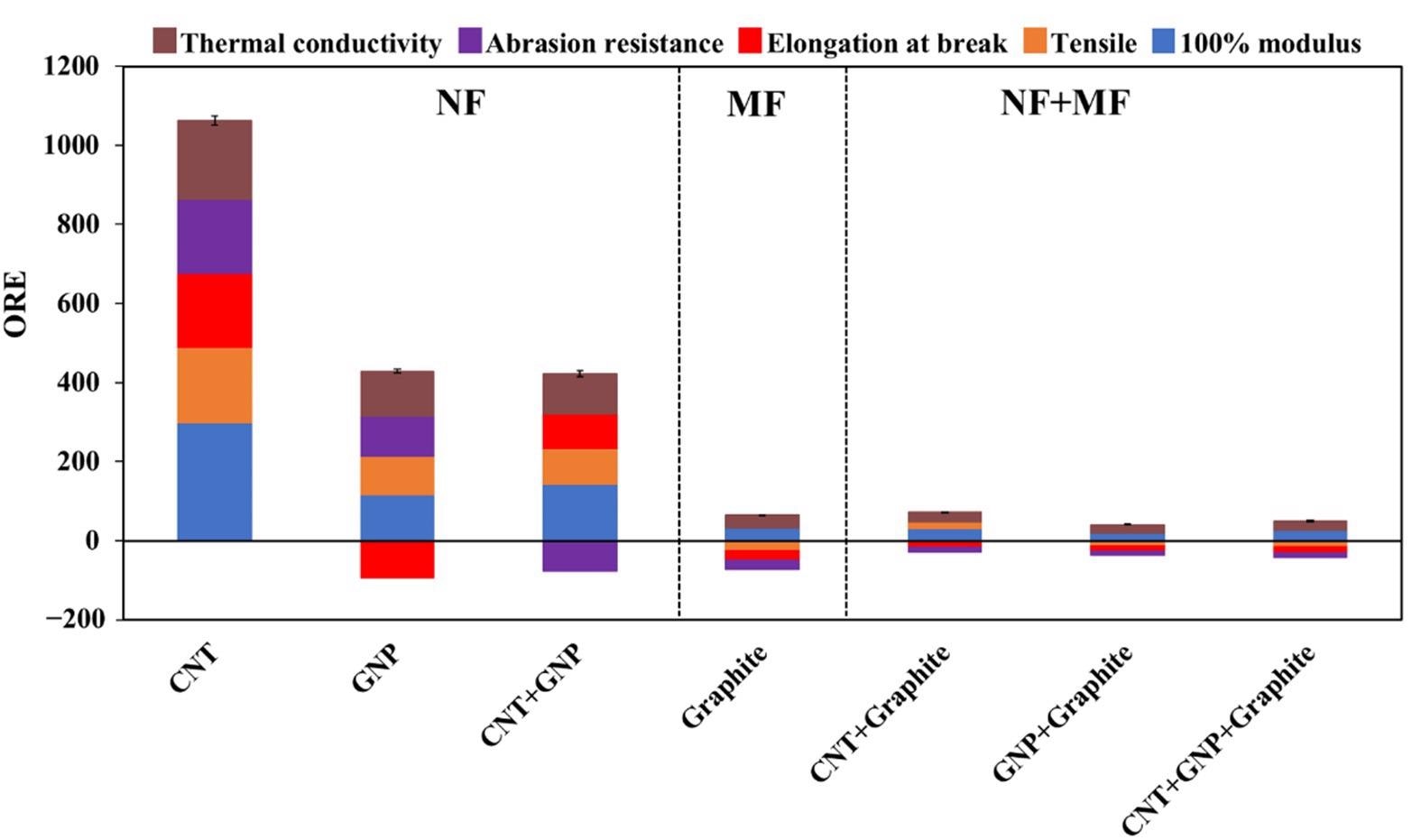
The overall Rnrelative Enefficiency (ORE) values of the various studied combination of fillers (see composition in Table 3). The color code indicates the contribution of the different properties (as in Figures 3–5). The dashed lines separate the nano-size filler (NF), micron-size filler (MF), and their combination (NF + MF). Image Credit: Gal Shachar Michaely et al., Nanomaterials
To conclude, using oil as an ‘entrance door’ to the fillers in rubber-based composites is a convenient as well as efficient approach.
An environment-friendly soya bean oil is an alternative for green minders. A rough estimate suggests that it requires 7 gallons of crude oil to manufacture one tire, as the purpose of crude oil is to decrease the viscosity of the rubber mixture with the fillers. The authors recommended the use of oil along with CNT with higher ORE scores to ensure that the mechanical and thermodynamic properties are conserved to enhance the tread performance.
Disclaimer: The views expressed here are those of the author expressed in their private capacity and do not necessarily represent the views of AZoM.com Limited T/A AZoNetwork the owner and operator of this website. This disclaimer forms part of the Terms and conditions of use of this website.
Source:
Disperse-and-Mix: Oil as an ‘Entrance Door’ of Carbon-Based Fillers to Rubber Composites Gal Shachar Michaely, Dimitry Alhazov, Michael Genkin, Matat Buzaglo, Oren Regev Nanomaterials 2021;11(11),3048; https://doi.org/10.3390/nano11113048 https://www.mdpi.com/2079-4991/11/11/3048