Mar 31 2008
Despite being one of the driest countries on Earth, many people are surprised to learn that Australians are among the highest per capita users of water in the world. As world population has tripled, and water use has increased six-fold over the last century, we in Australian have overdrawn our water resources to the extent that we are taxing major river systems beyond sustainable extraction limits - while also using more ground water than ever before.
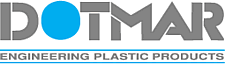
Australia's water use has in fact increased 65 per cent since the early 1980s, according to the Federal Government's National Land and Water Resources Audit.
Small wonder then that the spotlight is being thrown on the efficiency of our water and waste water infrastructures - not only of our potable water supply and sewerage systems, but also the performance of systems that re-use effluent in this sunburnt country (particularly in sectors such as mining, agriculture, recreational facility, electricity and gas, metals, forestry and water supply).
Engineering thermoplastics have an increasingly important role to play in enhancing the efficiency and reliability of such infrastructures. Any engineer who has ever seen the havoc wrought on metals and other decay-prone materials used near water, waste water and recycling process solutions needs no introduction to the challenges of these aggressive environments.
The potent cocktail of liquid and chemicals poses an ongoing challenge to government and private industry engineers alike charged with the responsibility of maintaining infrastructure and machinery in top condition – without incurring massive maintenance budgets to do so (or suffering the political backlash when something breaks down).
The problem is not only the major plant involved – the big ticket items in primary and secondary treatment plants – but also the myriad of ancillary items involved in each stage, in settling, feeding, filtering, screening, pumping and conveying solutions and sludges from one point to the next. After all, any chain is only as strong as its weakest link.
Answers to many of these problems are being provided by advanced technology engineering plastics, such as the versatile families of Polystone, Ertalon and Nylatron plastics. Apart from their obvious advantage of resistance to corrosion and fouling, their low friction, low weight and low wear characteristics help produce high reliability and long operational life. These attributes - combined with non-toxicity, excellent strength, dimensional stability and cost-efficiency - are among the primary reasons why they are replacing metals, old-generation plastics and more expensive products that have been used for decades.
These super plastics are finding expanding uses in such areas as pumping stations, sewage treatment plants; primary, secondary and tertiary treatment processes; conveyors; filters; and river and ocean discharges, including underground and underwater. Recent examples include:
• DAF (Dissolved Air Flotation) clarifiers, where Polystone 7000SR has been used to fabricate sprockets and wear shoes. Differently formulated Polystone 7000 has been applied to under-chain wear strips, while the ubiquitous Nylon has demonstrated its value in sprockets. Bar and step screens have also employed Polystone 7000SR vanes.
• Sedimentation tanks. Here Polystone 7000SR sprockets appeal because of their light weight, ease of installation, corrosion resistance, lubricity and economical replacement benefits. Ertalon 6PLA side tracking wheels offer similarly excellent corrosion protection in this application, as well as UV resistance, noise and weight reduction (and they don’t require lubrication either)
• Centreless screw conveyor linings. These have employed dual layer/dual colour Ultra High Molecular Weight Polyethylene (UHMWPE). The dual layer acts as a wear indicator, with the 9mm top layer in brown or black and a 3mm bottom layer in yellow or green. Apart from the non corrosion benefits, the UHMPWE offered noise suppression, wear resistance and was easy to manufacture and install. Similarly, Nylatron MC901 was used for hangar bearings in screw conveyors, where its non-lubrication qualities were valued - and it was kind to the counter face of the screw.
• Belt dewatering equipment. Polystone Ultra has been selected here because it is non-corrosive, kind to the belt and highly resistant to abrasion (qualities which also were employed in a scraper for removing dewatered sludge from the belt).
• Blue metal filtering sprinklers. Ertalyte TX thrust washers were employed because – in addition to self-lubrication and wear resistance – they offered no moisture absorption and outstanding strength and creep resistance.
• Fine Screen drum filters. These have benefited from Ertalon 6PLA and Nylatron MC 901 being used as strong, impact and wear resistant sacrificial components (which also don’t need lubrication and don’t corrode). Ertalon 6XAU has also been used in drum support rollers.
• Tertiary Treatment Chemical Dosing Ponds. Slide strips for gate and Penstock valves have been fabricated from Polystone 7000, which has a low coefficient of friction and offers economical service with high resistance to wear and abrasion. The material is used in this application by OEMs.
Engineered from stock shapes from Dotmar EPP's national network, long-life plastics such as Polystone, Ertalon and Nylatron are extreme plastics for extreme performance.