Mar 26 2009
Anyone expecting to hear the engine roar into life when the "Antares DLR-H2" motor glider takes off, will be in for a surprise: the aircraft rises almost soundlessly from the runway. And there's no smell of fuel either. Because the Antares is the first manned aircraft to be powered exclusively with hydrogen (H2). The fuel cell system that makes this possible is hidden in the underwing pods. This is where the electricity for the on-board electronics and electric motor is generated. The heart of the system is a membrane electrode assembly, MEA for short, developed by BASF Fuel Cell (BFC). In the MEA, chemical energy generated by the reaction between oxygen and hydrogen is converted directly into electricity and heat (see Graphic and Info box).
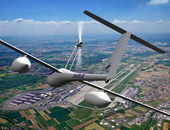
The Antares DLR-H2 was built by the German Aerospace Center (DLR) and the Lange Aviation company to test the fuel cell's potential for aviation applications. "BASF is participating in the pilot project to promote an innovative energy technology which will really be taking off in the near future, and not just on board aircraft," emphasizes Dr. Carsten Henschel of BFC. "In times of scarce energy resources the fuel cell can, for example, help maintain security of supply because hydrogen can be obtained from a wide variety of sources: from wind or solar energy and from natural gas or diesel. Moreover, it is much more efficient than conventional energy technologies and the only waste gas it emits is water vapor."
The challenge now facing the developers is to keep the fuel cell system as small and lightweight as possible for practical applications. The key factor in achieving this is for the system to have as few components as possible. Conventional low temperature fuel cell systems operate at a maximum of 80 degrees Celsius. They need a large number of ancillary units and a complex control system to function in airplanes both on the ground and at high altitudes. The MEA developed by BASF is now opening up new horizons for system builders: it contains the world's first commercially available membrane for fuel cells which allows operating temperatures of up to 180 degrees Celcius. The innovative systems are marketed under the brand name Celtec®. Fuel cells equipped with this material can be cooled by the air and don't have to be moistened with water. This eliminates the need for air humidifiers, water pumps, tanks, valves and cleaning systems.
The outstanding efficiency of the Celtec® membrane isn't obvious at first glance: the approximately hand-sized, super-thin rectangle looks like any conventional plastic film. BASF's research scientists, however, have succeeded in developing a membrane based on the temperature stable polymer polybenzimidazole. This plastic, which is also used for firefighters' suits, endows the BFC membrane with outstanding resistance to heat. A high operating temperature also prevents impurities in the hydrogen from building up on the platinum coated electrode (anode). In the MEA, platinum acts as a catalyst initiating the electrochemical reaction. Impurities would block its catalytic activity. Because high-temperature fuel cells tolerate higher levels of impurities in the hydrogen than low-temperature systems, hydrogen purification becomes easier – making the fuel cell system even more robust, simple and cheaper to manufacture. "Thanks to Celtec®, fuel cell systems now need a third fewer components. This reduces the costs by up to 40 percent. The development of the high-temperature membrane has finally made the fuel cell interesting as a commercial sales product," explains BFC expert Henschel.
To make a fuel cell capable of producing sufficient electricity for practical applications such as powering the Antares motor glider, several cells are combined into a fuel cell stack. This is because a single cell can only deliver a voltage of about 600 to 700 millivolts. Specially for the Antares, the Danish company Serenergy has developed a particularly lightweight, air-cooled stack system consisting of many hundreds of cells with Celtec® MEAs. Each of the MEAs is enclosed in a matrix of electrically conductive graphite plates. The plates connect the individual cells together, conduct the electricity onwards and supply the MEAs with hydrogen and oxygen through special ducts. With these combined forces, the fuel cell is capable of lifting the Antares into the skies.
"Following the test flights in the Antares, we intend to install the fuel cell in our Airbus A320, where it will be optimized for use in wide-bodied aircraft to make the on-board electricity supply more efficient in future," explains Dr. Josef Kallo of the DLR in Stuttgart. Installed in a wide-bodied aircraft, the fuel cell would be a real all-rounder: not only can the electricity it generates be used to supply energy, the by-products heat and water could also serve as "antifreeze" for the wings and to supply the washrooms. The DLR test series with the Antares are scheduled for completion in 2010 and the fuel cell will take then off for the first time in DLR's "A320 ATRA".