Apr 1 2009
The innovative Varysoft slide-table mould developed by Georg Kaufmann Formenbau AG, Busslingen/Switzerland, enables the production of particularly comfortable passenger compartment parts: it is now possible, for the first time ever, to vary the thickness of the layer of soft-touch foam via the mould geometry. The Varysoft layer of foam is produced exactly where it is required in the part and also in the desired thickness. To this end, the slide-table mould is equipped with two cavities, one for the conventional injection moulding of the supporting structure and one for the preforming of the decorative material – film, fabric or imitation leather – and, later, the moulding of the Varysoft® layer of foam.
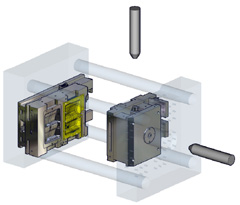
Suitable for TPE und PUR foam The mould necessitates the use of an injection moulding machine equipped with a sliding table. A standard injection unit injects the material – usually a polypropylene (PP) – for the supporting structure. For the production of the layer of foam, the machine may be equipped either with an additional injection unit for expandable thermoplastic elastomer (TPE) or with a polyurethane (PUR) processing unit with PUR mixing head.
In the two-stage Varysoft® process, the pre-cut decorative material is placed in the second cavity of the open mould and fixed in place. The mould then closes and the decorative material is preformed, while in the first cavity the PP supporting structure – for a door trim, for example – is moulded by a conventional injection moulding process and then cooled.
When the mould opens, the PP supporting structure remains in the moving mould half and the pre-formed decorative material remains in the stationary mould half.
The two halves of the open mould are then repositioned by means of the sliding table in such a way that the PP supporting structure and the preformed decorative material are opposite one another. When the mould closes, a gap remains between the supporting structure and the decorative material corresponding to the desired thickness of the Varysoft® layer of foam. This thickness is determined by the geometry of the second cavity of the stationary mould half. It is deeper than the geometry of the first cavity by a distance equal to the desired thickness of the foam.
This gap is now filled with foam by the second injection process. The expandable TPE is injected into the gap via a special gating system and diverter mounted on top of the mould, while in the case of PUR foam the mixing head is docked up against the underside of the mould. Upon completion of the foaming process, the finished Varysoft® door trim can be removed from the mould and any surplus decorative material trimmed either manually or automatically with a punching tool.
Posted April 1st. 2009