Sep 23 2009
H+H UK's Rå Build method of construction was used to speed up the construction of 16 new affordable and retirement homes in West Sussex. The use of Jumbo Bloks, Celcon Foundation Blocks and the H+H Flooring System mean aircrete was used for the entire inner skin of the development.
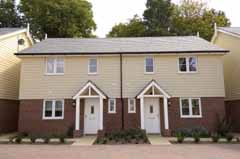
The Rå Build method of construction with a cavity wall was preferred as it is quick to install and because of the need to meet level three on the Code for Sustainable Homes. The excellent acoustic and thermal characteristics inherent with this type of construction helped to achieve this.
The completed first phase of the development achieves a U-Value of 0.21W/m2K. The external cavity walls were constructed with a Thin-Jointed aircrete inner leaf and brick outer-leaf topped with a pitched, tiled roof. The foundations and ground floors made use of the tongue and groove H+H Flooring System with Celcon Foundation Blocks. From laying the foundations to roof completion took approximately 16 weeks. Some 3,000 m2 of aircrete was laid with a further 900 m2 of flooring product.
With the majority of the development being made up of retirement homes, sound insulation was especially important. Telegraph Construction specified a minimum 50db sound reduction for separating walls to achieve 3 credits on the Code for Sustainable Homes. H+H UK partnered with Isover to devise a bespoke solution. Trial construction of a new wall building method was carried out and tested at H+H UK 's Borough Green Research Laboratories prior to any work beginning on site. The chosen approach was to fill the separating wall cavity with insulation tailored to enhance acoustic rather than thermal performance, something never done before with an aircrete construction. Once completed, sound tests have shown an average 56db sound reduction, far better than required, giving the development an extra credit on the Code for Sustainable Homes.