Mar 15 2005
The challenge of getting the various parts of the A380 to Toulouse, where the aircraft is assembled, has led Airbus to develop its own logistics. Until now, it has mainly used the voluminous A300-600ST, known as the Beluga because of its whale-like appearance, to transport components by air. However, the Beluga is not spacious enough for the largest parts of the A380, and Airbus has developed its own “road-river-sea-river-road” transport link.
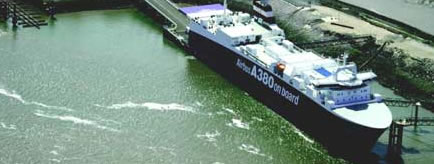
The largest elements of the A380 are its wings. The skins are made at the Alcoa plant in Davenport, Iowa – the only plant in the world able to produce 35-meter aluminum plates. The plates are transported on a special telescopic truck to Baltimore where they board a ship for the BAE Systems factory in Broughton, Wales, where the wings are assembled. Each completed wing, now 45 meters long, is mounted on a special jig on which it will remain until it reaches Toulouse. For the first stage of the journey, it is carried on a 96-wheel trailer to a terminal on the River Dee.
There, the wing is loaded onto a powered barge. Although the barge was specially designed for the route, it must wait for low tide to be able to pass under the bridges along the way. At the port of Mostyn, 24 kilometers downriver, the wing is loaded aboard Airbus’s own Shanghai-built RoRo ferry, the “Ville de Bordeaux,” which takes it to Pauillac, near Bordeaux. There, it is transferred via a Polish-built pontoon onto another barge.
This makes its way a hundred kilometers up the River Garonne to Langon. There it waits for a second wing and a fuselage to arrive, and then a long, slow nighttime convoy travels 240 kilometers along country roads, resting during the day to avoid the traffic. Airbus has had to strengthen the roads and build by-passes to avoid villages along the route. Three days later, the convoy finally reaches the Toulouse plant.
Trelleborg provided fenders, under the brands Fentek and Seaward, for many of the transfer points along the route taken by the wings. The company also supplied modified donuts and pads for the special berth trestles at Broughton and Mostyn.
In Mostyn, Airbus’s RoRo ferry berths against Trelleborg parallel motion fenders, which provide a high level of energy absorption and allow a much lighter support structure. To ensure the barge does not strike land too forcefully when reaching Langon, three-part trapezoidal fenders and a donut are used to berth the barge at the quay. It then slides along polyethylene fenders into a v-shaped wet-dock where vertical arch fenders buffer its arrival.
http://www.trelleborg.com/
Posted 15th March 2005