Oct 10 2012
DTC Dutch Thermoplastic Components, Kok & Van Engelen, NLR National Aerospace Laboratory of the Netherlands, TenCate Advanced Composites and VIRO have decided to collaborate in the European Thermoplastic Automotive Composites consortium (eTAC). These companies, each in their own area of expertise, play a leading role in the production and processing of fibre-reinforced thermoplastic composites. Their aim is to promote the use of these advanced materials in the automotive sector.
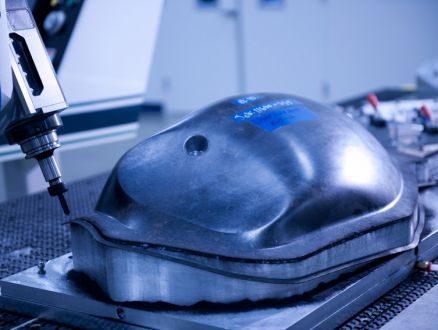
The partners in the eTAC consortium have built up an impressive track record in the aviation industry in the past few decades. The same technological development is currently to be seen in the automotive sector to produce light, energy-efficient and thus cleaner solutions. This requires innovations in the field of materials, design, manufacture, processing and automation. The new eTAC partnership will officially come into being in October 2012.
Automotive industry
The automotive industry is showing greatly increased interest in the industrial applications of light materials. Thanks to current developments, thermoplastic composites can in many cases provide a solution to achieve the desired weight reduction. The composites that have been used in the automotive sector until now, primarily in sports cars and exclusive models, are proving not to be entirely satisfactory. Their processing capability does not yet meet the required industrial production rates, particularly in the automobile industry, in part due to the number of units to be produced, environmental standards, etc.
The initiators of eTAC have already proved that in close collaboration they are able to successfully develop innovative concepts for the aviation industry, including Airbus Industries. There has already been project-based collaboration in the automotive sector. In an eTAC context this collaboration will take on a more structural form and content, in order to speed up industrial solutions.
eTAC objectives
The current rapidly growing interest in composites will have to be translated into specific business cases. The creation of industrial processing capability will encourage the use of such materials in the automobile sector. Knowledge relating to the application of thermoplastic composite technology is not widely available in the market, in part because this technology is still relatively new outside the aviation sector. The eTAC consortium will provide potential users with this knowledge when defining their applications. It will involve the entire production chain in this, since this is a new technology both in the field of materials and in the processing of these materials into end products.
Solution-oriented
eTAC is primarily solution-oriented, which will also involve applied research. It is a project-driven partnership that will provide solutions requested by car manufacturers and their supply chain. The customer will decide what knowledge and skills are required for each project in order to achieve the desired result.
In doing so, eTAC can link up with existing networks, research centres and knowledge institutions, such as TPRC (ThermoPlastic composite Research Center). This fits in neatly with Dutch innovation policy on High-Tech Materials & Systems, one of the recognized leading sectors. The NLR National Aerospace Laboratory of the Netherlands will provide considerable added value by testing production processes and validating pilot installations and demonstrators. The partnership possesses all the necessary knowledge to make an essential contribution to the current development issues relating to composite use in innovative mobility concepts, such as hybrid and electric cars or - in a broader sense - 'individual mobility'.
The international presence of the various partners in eTAC will enable these services to be offered locally. This will also involve integration with local networks, thus enabling eTAC to have offices in several countries, including the Netherlands, the UK and Germany. New players will be able to participate in eTAC either on a project basis or as a permanent partner.
Advantages of thermoplastic composites
Fibre-reinforced composites have been developed in close collaboration with fibre producers (carbon fibre, glass fibre, etc.), companies in the field of technical textiles (like TenCate), and the chemical industry (including synthetic resins). The combining of the various material components has resulted in composite materials with specific optimized characteristics. The first generation of materials (thermoset composites) can only be deformed during the final processing at the customer's premises. This usually involves a high labour cost component and relatively low processing speeds in industrial manufacturing processes, which is the main reason why such composite materials are rarely used in mass production.
Thermoplastic composites were developed - initially mainly for the aviation sector - to meet the requirements of industrial processing, especially as a replacement for aluminium (with a similar process for pressed parts). An additional aspect of this type of composite material is that material interconnections can be made relatively simply, thus enabling structural parts to be manufactured. The use of thermoplastic composites (such as TenCate Cetex®) has consequently increased greatly in the aviation sector.
The Technical University of Delft, the Netherlands, and TenCate are the foremost pioneers of such materials for the aviation sector. In the Netherlands a strong industrial sector has developed around this innovative material development and its processing. This has also resulted in the establishment of TPRC (ThermoPlastic composite Research Center) and TAPAS (Thermoplastic Affordable Primary Aircraft Structure consortium).
Application of the knowledge available within the eTAC consortium can make a significant contribution to the current issues existing in the automotive sector. The demand for sustainable solutions has increased rapidly. In addition to the intrinsic technological advantages of the material, thermoplastic composites also satisfy recycling requirements.
Royal Ten Cate
Almelo, the Netherlands, Monday, 8 October 2012