Sep 30 2013
NASCAR drivers rely on some of the world's most innovative, high-performance vehicles to maneuver around the racetrack at speeds of up to 230 kilometres per hour. While the fast-paced action can be thrilling, real precautions must be taken to protect the driver, crew, and spectators in the event of a collision.
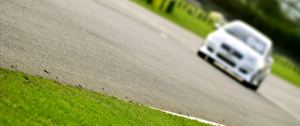
It may be surprising to learn that plastics play an integral role in the safety of NASCAR racing—and that these innovations in plastics can end up in the car you drive every day.
Protective safety gear is vital for both driver and crew during a race. A specially designed helmet—typically made with several different types of plastics—is the most obvious first line of defense for the driver. The hard outer shell of the helmet usually contains plastic fibres typically known as Kevlar® (a DuPont trademark), the super-strong, impact-resistant material that also is used to make body armour. Beneath the outer shell, a shock-absorbing layer of polystyrene or polypropylene plastic foam cushions the driver's head. Finally, the interior of the helmet is lined with a flame-resistant plastic fibre typically called Nomex® (also a DuPont trademark) that helps protect the driver in case of fire. Drivers usually wear a full-body Nomex® jumpsuit as well.
For further protection, NASCAR drivers often use a head and neck support (HANS) device, a strong but lightweight restraining collar made with carbon-fibre-reinforced plastic and Kevlar®. The collar attaches to a body harness, which prevents the driver's head from snapping forward or sideways during an impact and reduces the likelihood of head and neck injuries.
Plastic components in the racecar also help protect the driver and can enhance vehicle performance. For example, the interior of the racecar's fuel tank is lined with hard plastic to help prevent punctures and fuel leaks in the event of a crash. In addition, various spoilers and flaps that increase "downforce," which keeps the car closer to the ground to prevent flipping, often are made with plastics. And a windshield made with nearly unbreakable polycarbonate plastic and laminated with polyethylene terephthalate plastic helps protect the driver from airborne debris on the track. (Polycarbonate is significantly lighter than glass, so the plastic windshield also reduces the car's weight to improve performance).
Many venues that host NASCAR-sanctioned events use plastics to improve safety on their racetracks. Tracks in Indianapolis and Talladega are built with "soft walls." Made with plastic lumber, polystyrene plastic foam, and concrete, these walls absorb impact and cause far less damage to a vehicle than a solid concrete wall. In fact, NASCAR driver Jeff Gordon credited the soft wall with helping save his life when his car crashed in 2006.
So how do these racing innovations affect your daily commute? Inevitably, many breakthrough innovations in racecar technology trickle down to production cars, contributing to performance, design, and safety. For example, the same carbon-fibre-reinforced plastics used in racecars are now making their way into some production cars. Car manufacturers are also exploring increased use of polycarbonate as a lighter and more durable alternative for windshields, windows, and sunroofs. And researchers at the Midwest Roadside Safety Facility—the organization that developed the racing soft wall—are using similar plastics technology to design "soft" guardrails for highways across the country.