Dec 4 2019
UNSW Sydney researchers have successfully merged 3D/4D printing with a chemical process to produce “living” resin, which has huge potential for fields as diverse as recycling and biomedicine.
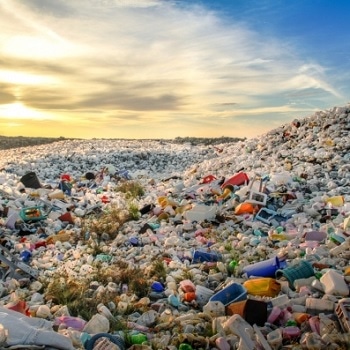
The researchers have revealed the successful merging of 3D/4D printing and photo-controlled/living polymerization. Repairing and reusing plastics and delivering cancer drugs more effectively are only two of the many potential applications of the new 3D/4D printing technology, thanks to the pioneering work of a research collaboration between UNSW Sydney and The University of Auckland.
Environmentally Friendly “Living” Plastic
The new controlled polymerization method, where the researchers used visible light to create an environmentally friendly “living” plastic or polymer, opens a new world of possibilities for the manufacture of advanced solid materials.
Applicable to Both Synthetic and Biological Polymers
Polymers can be synthetic, such as plastic, as well as biological, for example, DNA. Such polymers can be reactivated for further growth, unlike traditional polymers which are “dead” after being made.
Since this development, the technology has expanded and has proven useful for making well-controlled molecules for many applications, including drug delivery and other biomaterials.
New 3D Printing System Using PET-RAFT Polymerization
Lead author Cyrille Boyer said his team’s latest breakthrough was a world first in the development of a new 3D printing system using PET-RAFT polymerization, to allow 3D printed materials to be easily modified after printing.
“Controlled polymerization has never been used in 3D and 4D printing before, because the rates of typical controlled polymerization processes are too slow for 3D/4D printing, where the reaction must be fast for practical printing speeds,” said Prof Boyer. “After two years of research and hundreds of experiments, we developed a rapid process compatible with 3D printing.
“In contrast to conventional 3D printing, our new method of using visible light allows us to control the architecture of the polymers and tune the mechanical properties of the materials prepared by our process.
“This new process also gives us access to 4D printing and allows the material to be transformed or functionalized, which was not previously possible.”
Ability to Control All Molecules in the 3D Printed Material
A bonus advantage of this new system was the ability to finely control all molecules in the 3D-printed material. “4D printing is a subset of 3D printing. But with 4D printing, the 3D-printed object can change its shape and chemical or physical properties and adapt to its environment,” Dr Corrigan said.
“In our work, the 3D-printed material could reversibly change its shape when it was exposed to water and then dried.
“For example, the 3D object starts as a flat plane and when exposed to certain conditions, it will start to fold, which is a 4D material. So, the fourth dimension is time.” “Current 3D printing approaches are typically limited by the harsh conditions required, such as strong UV light and toxic chemicals, which limits their use in making biomaterials,” he said. “But with the application of PET-RAFT polymerization to 3D printing, we can produce long polymer molecules using visible light rather than heat, which is the typical polymerization method.
“Using heat above 40 degrees kills cells, but for visible light polymerization we can use room temperature, so the viability of the cells is much higher.”
Many Applications for Several Problems
Dehydration induced actuation
The researchers are hopeful that their new 3D/4D printing process will lead to the production of functional materials to solve many of the problems facing society. Prof Boyer said the new method had a multitude of applications for everyday items, particularly, if a deformed or broken object needed to be repaired or modified.
Main Application Recycling
“The main application is of course recycling, because instead of using a plastic object once, it can be repaired and reused,” he said. “For ordinary recycling you take the materials away and have to reconstruct them, but for the new ‘living’ material it will be able to repair itself.
“For example, if you want to put the UNSW logo on a mug, you can modify the surface of the object and grow the polymers to show UNSW because the object is not dead. It’s a living object and can continue to grow and expand.”
Compatible with Biomedicine
Dr Corrigan said another major benefit of the new process was its compatibility with biomedicine, because extreme conditions were unnecessary.
Prof Boyer said objects made through this new process could more easily be used in advanced bio-applications, such as tissue engineering, for example, where a tissue structure is used to form new, viable tissue for medical purposes.
“Our new method targets small scale, niche applications in fields like microelectronics and biomedicine, a huge area for us, that require very advanced polymers,” he said.
For Both Commercial and Non-Expert Operators
Prof Boyer said their new technique would allow commercial and non-expert operators to produce materials with seemingly endless properties and applications. “We want to explore our system to find and address any limitations to allow for better uptake and implementation of this technology,” he said.
“There is so much we can do by combining 3D and 4D printing with controlled polymerization to make advanced and functional materials for many applications to benefit society.”