By Susha Cheriyedath, M.Sc.Reviewed by Skyla BailyNov 19 2021
A team of researchers from Brazil recently reviewed the extraction of valuable metals from electronic wastes using the chemical leaching process. This study has been published in the Journal of Environmental Chemical Engineering.
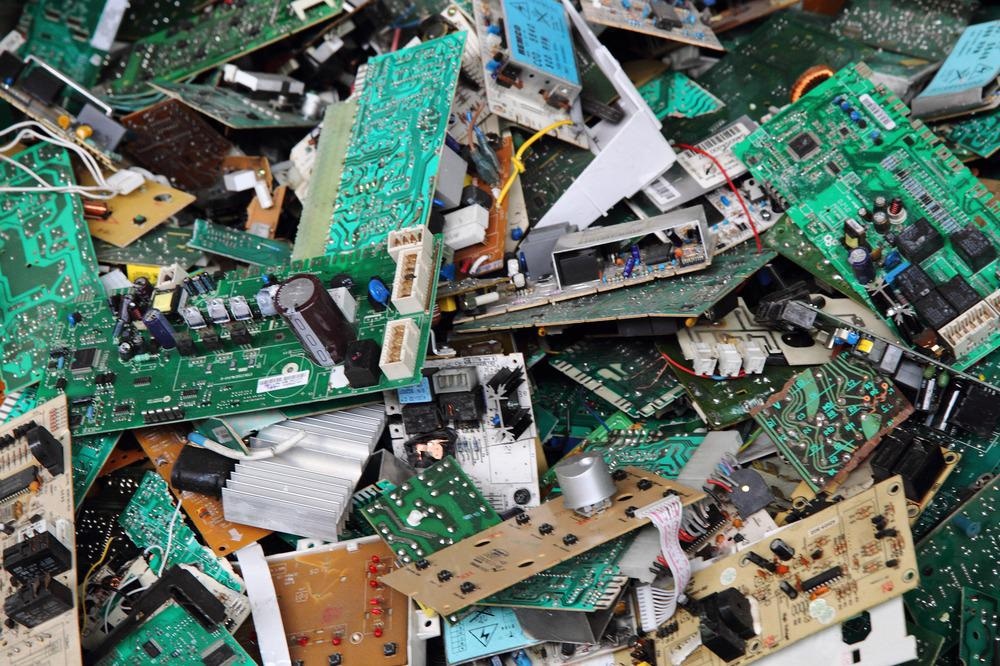
Study: Recovering metals from motherboard and memory board waste through sulfuric leaching. Image Credit: Jirik V/Shutterstock.com
Why the Extraction of Metals from E-wastes is an All-Round Profit?
Urban mining is a necessity for current and future generations to complement the consumption of natural resources by recovering materials from post-consumer products, transforming them into raw materials, and adding value to these wastes.
The recovery of metals from the wastes of electrical and electronic equipment (WEEE) can be a solution to environmental as well as economic problems that arise from managing these materials for a large population.
Printed circuit boards (PCBs) are the major components of electronic equipment; they represent 3-4% by weight of these scraps, and, in advanced consumer electronics, their waste can be responsible for 80% of the total metal recovery value. They can be made up of about 40% metals (such as Al, Fe, Ni, Cu, Zn, Sn, Ag, and Au), 30% polymeric materials, and 30% ceramics.
The recycling of waste PCBs involves existing techniques similar to conventional extractive metallurgy which is composed of different stages of extraction, purification, and recovery of metals from ores. These processes include pyrometallurgical, bio-hydrometallurgical, and hydrometallurgical. These processes can be performed separately or simultaneously, depending on the metals, the available technology, and the purity of interest.
Generally, two types of PCBs are used in small equipment and electronic appliances which are FR-2 and FR-4. The abbreviation FR means flame retardant. The major difference between these two types of PCBs is that FR-2 is composed of cellulose paper and coated with phenolic resin whereas FR-4 is composed of reinforced glass fibers coated with epoxy resin.
What are the Challenges?
The WEEE also contains hazardous materials (such as Cd, Hg, Pb, and Cr). Thus, the improper disposal or treatment (including informal recycling of these materials) of these wastes can lead to environmental pollution and risks to human and animal lives.
Many studies have used magnetic separation in scrap PCB recycling. Iron is the most retained element in the magnetic fraction, followed by nickel, but lead and copper (non-ferrous metals) were also found in this fraction.
The slow material release during bulk extraction in the comminution process dragged the nonmagnetic particles along with it. Physical separation has been used to recover metals from scrap PCBs; however, it can cause metal losses of 10 to 35% owing to the insufficient release of metals in the fine fractions of plastics.
More on Recycling Industry Waste - Using Denim Waste to Produce a 3D Needled Composite
The hydrometallurgical process allows the recovery and purification of specific metals in multi-element solutions using techniques such as selective leaching, solvent extraction, electrowinning, the use of chelating resins, and precipitation.
Moreover, when compared to pyrometallurgy, hydrometallurgy has a more selective metal recovery ability with additional benefits of reduction in the emission of gases emitted into the environment and without any significant investments and operating costs.
What are the Steps?
The recycling of the scraps is initiated by the pretreatment stage which includes the dismantling of the parts containing possible metals. After that, physical separation and/or comminution can be performed using methods such as magnetic, electrostatic, pneumatic, and density separation. All these steps are performed chronologically to completely release the specific metals of interest from the PCBs.
What Does the Experiment Say?
The team pretreated, processed, and characterized the recovered metals from the scraped motherboards and memory boards. They performed three leaching steps: the first in a sulfuric acid medium for 18 hours; the second in an oxidizing acid medium for 6 hours at 95 °C and acid concentration of 2 M; and the third in 10 M nitric medium for 2 hours at room temperature.
They concluded that the primary leaching in a sulfuric medium is a suitable alternative to replace the magnetic separation for the iron extraction and subsequent hydrometallurgical processing of other metals.
Out of two acid leaching steps, one was able to extract iron, aluminum, and the highest percentage of tin, while the other acid leaching step in oxidizing medium extracted silver, copper, and the highest percentage of nickel and zinc.
Thus, a combination of these two methodologies can be used for the separation of iron from copper.
The hydrometallurgical study showed all the metals present in the memory board sample were solubilized, while on the motherboard only about 73 wt% of the metals were leached. However, after increasing the solid/liquid ratio of the motherboards, the leaching percentage of these samples increased to about 98 wt%, indicating that the metal extraction does not depend on the residue-acid ratio but the metal-acid ratio.
Reference
T. Auxiliadora, G. Martins, M. Caldas, V. Moraes, J. Tenório, D. Crocce, R. Espinosa, Recovering metals from motherboard and memory board waste through sulfuric leaching. Journal of Environmental Chemical Engineering, 106789. https://www.sciencedirect.com/science/article/pii/S2213343721017668?via%3Dihub
Disclaimer: The views expressed here are those of the author expressed in their private capacity and do not necessarily represent the views of AZoM.com Limited T/A AZoNetwork the owner and operator of this website. This disclaimer forms part of the Terms and conditions of use of this website.