In a recent study published in the journal Polymers, researchers analyzed several reinforcement materials for toughening recycled devulcanized rubber. These materials include glass bubbles, glass fiber, alumina spheres, alumina fiber, aluminum chips, and boron nitride.
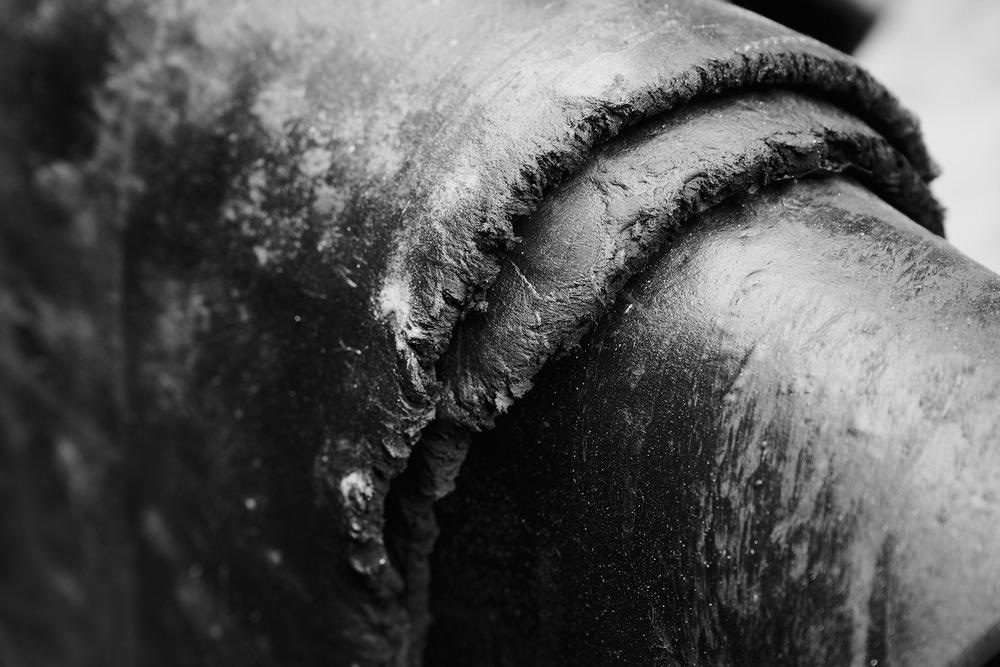
Study: Toughening Mechanism Analysis of Recycled Rubber-Based Composites Reinforced with Glass Bubbles, Glass Fibers, and Alumina Fibers. Image Credit: Akimov Igor
Despite the difficulty in completely devulcanizing recycled rubber, these reinforcements significantly enhance its mechanical properties, thus paving a way for a sustainable circular economy for the rubber-based manufacturing industry.
Why Should Rubber-Based Composites be Part of Rubber Recycling?
Rubber is a versatile material in many industries such as aeronautic, automotive, electric insulation, apparel, and transportation owing to high toughness, high resistance to impact, low cost, and lightweight. Tons of waste rubbers come out of these industries every year. Devulcanization of these waste rubbers during recycling adversely affects their mechanical properties.
Consequently, different fillers are added to these recycled rubber to restore their properties. Glass bubbles with perfect spherical shape are efficient volume fillers, which provide significant weight reduction, performance, and dimensional and processing stability.
Alumina fibers and nano-silica particles enhance wear resistance, fracture toughness, and resin stiffness. Additionally, alumina has high absorption capacity, electrical insulation, thermal stability, high thermal conductivity, high compressive strength, and inertness to most chemicals.
About the Study
In this study, recycled rubber of average particle size 50 µm, modulus of elasticity of 10 MPa, breaking elongation of 80–100%, ‘Shore A’ hardness of 37 to 40, and density of 1 g/cm3 is used as the matrix material for the composite.
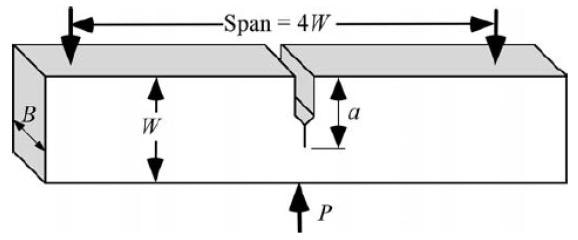
Three-Point single edge notch bending (SENB) test for fracture toughness, KIC and fracture energy, GIC characterization. Image Credit: Kabakci, G et al., Polymers
Seven samples are prepared using reinforcement materials viz. hollow glass bubble, glass fiber, alumina (γ-Al2O3) fiber, alumina sphere, Al-chips, nano-silica (SiO2), and boron nitride (BN). Epoxy resin is used as a binder between the rubber matrix and reinforcements.
Cured scrap rubber does not have any free links to form new bonding with epoxy resin. Thus, it is first devulcanized by heating it in a microwave oven for 4 minutes. During devulcanization, sulfur links break, and new links are generated. These links increase the interaction capacity of recycled rubber with epoxy and reinforcements.
In this study, only 10-12% devulcanization was achieved. To further improve the liaison between recycled rubber matrix and different reinforcements, silanization of rubber was performed. Silanization facilitates chemical bonding diffusion with different reinforcements.
After that, the prepared blended samples are milled for 4 hours by adding zinc stearate as a lubricant for homogenous mixing followed by hot compaction at 180-200 ℃ for 20 minutes under 6 tons of pressure. Finally, samples are cut into rectangular specimens for the three-point single edge notch bending (3PB-SENB) test.
Observations
The microstructure data from the scanning electron microscope (SEM) revealed a homogenous distribution of fillers in the rubber matrix with some small degree of agglomeration in case of glass bubbles. This agglomeration of particles reduced the strain efficiency of composites and showed the presence of a few micro-cracks that disappear after weekly propagation due to crack pinning.
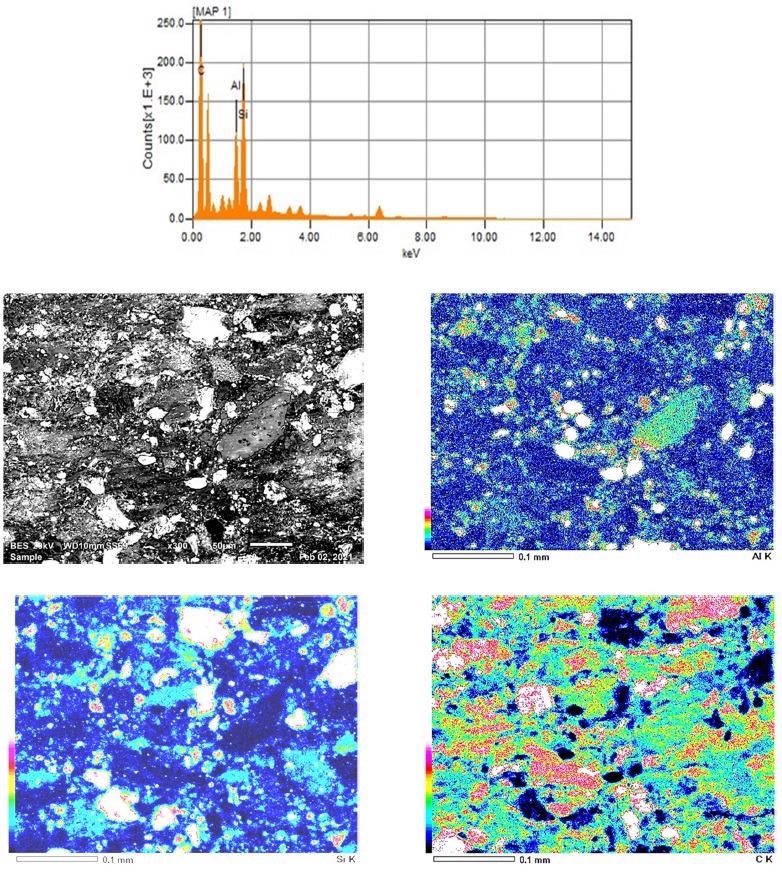
Energy Dispersive Spectroscopy (EDS) Chemical and Mapping for Specimen 6. Image Credit: Kabakci, G et al., Polymers
From the Shore-D hardness test, it is evident that the reinforcement fillers enhance the surface hardness. The aluminum chips and BN increased the surface hardness significantly, whereas the presence of glass bubbles and ceramic fibers had a very small effect on the surface hardness.
Energy dispersive spectroscopy (EDS) analysis indicated a preferable cohesion between the rubber matrix and the fillers in the samples owing to the absence of microcracks between hard and soft particles.
The 3PB-SENB test was conducted to obtain ultimate flexural stress, strain at break, modulus of elasticity, critical stress intensity factor, and critical strain energy release rate. It confirmed that alumina fibers enhance fracture toughness, strain under quasi-static loading, and the ability to absorb mechanical energy under static loading.
Similarly, glass bubbles improved the tensile strength and short glass fibers enhanced the mechanical properties. Moreover, increasing crosshead speed during the 3PB test increased the critical stress intensity factor.
The Halpin-Tsai model was used to measure the elasticity of all specimens. It showed that, with an increase in the weight fraction of alumina fiber, glass fiber, and glass bubbles, the Halpin-Tsai modulus of elasticity also increases.
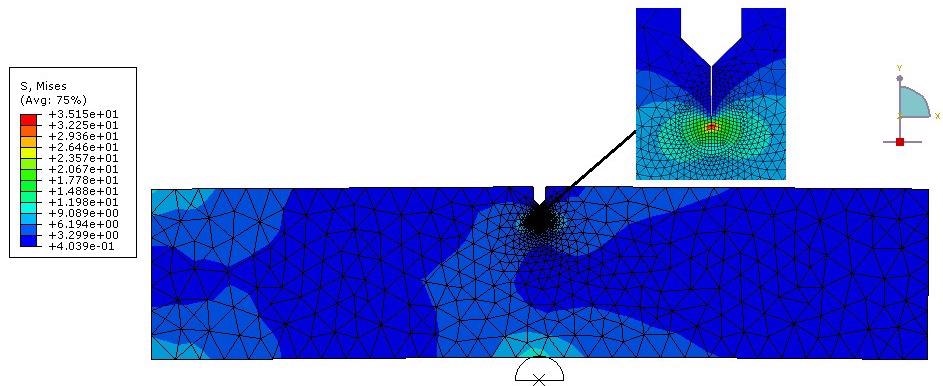
Numerical Model for 3P single edge notch bending ((SENB)) test for composite 4. Image Credit: Kabakci, G et al., Polymers
Conclusions
In this study, recycled devulcanized rubber was toughened by reinforcement with glass bubbles, short glass fibers, alumina fibers, alumina chips, nano SiO2 and BN. A rubber matrix to the epoxy ratio of 80:20 was used to bind these fillers effectively. The resulting composites showed effecting crack pinning, and improved mechanical and physical properties viz. fracture toughness, stress intensity factor, and critical energy release rate.
To conclude, effective recycling of waste rubber through the synthesis of reinforced rubber-based composites can be used in intermediate and advanced applications sustainably and cost-effectively, and contribute to a circular economy.
Reference
Kabakci, G., Aslan, O., Bayraktar, E., Toughening Mechanism Analysis of Recycled Rubber-Based Composites Reinforced with Glass Bubbles, Glass Fibers, and Alumina Fibers. Polymers, 2021, 13(23), 4215. https://www.mdpi.com/2073-4360/13/23/4215
Disclaimer: The views expressed here are those of the author expressed in their private capacity and do not necessarily represent the views of AZoM.com Limited T/A AZoNetwork the owner and operator of this website. This disclaimer forms part of the Terms and conditions of use of this website.