Researchers from China recently developed a new very high cycle fatigue chromium-nickel-molybdenum-based gear steel alloy with gradient carburized hardness that can withstand cyclic fatigue above 109 cycles under low-stress conditions.
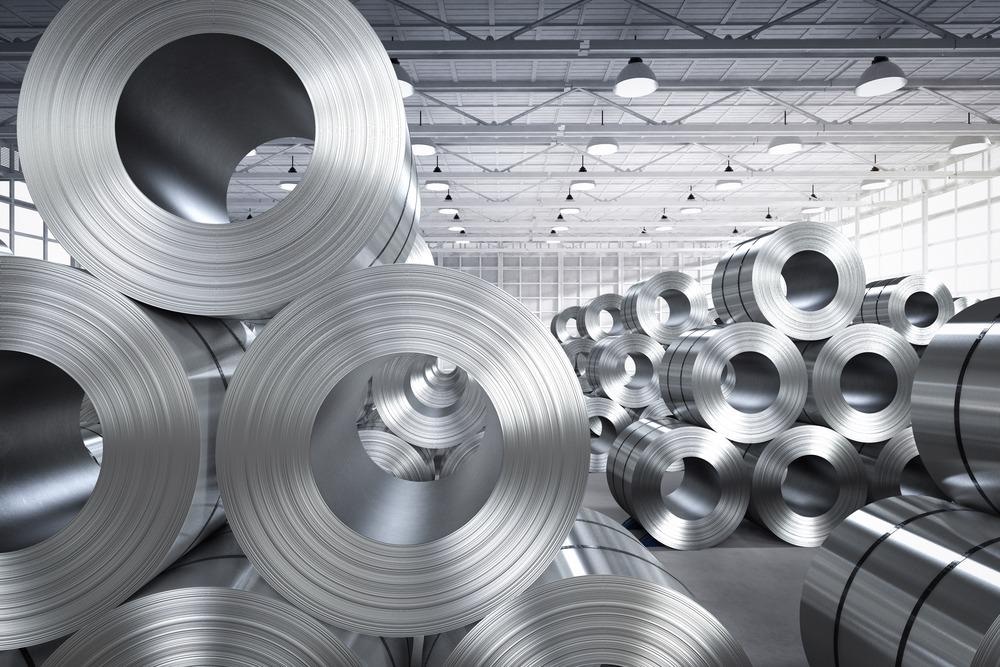
Image Credit: Very High Cycle Fatigue Properties of 18CrNiMo7-6 Carburized Steel with Gradient Hardness Distribution. Image Credit: Phonlamai Photo/Shutterstock.com
The alloy exhibits a surface hardness of 705 HV with a fine microstructure at granular bright facet and a core hardness of 530 HV. This study is available in the journal Coatings.
What is Very High Cycle Fatigue Steels?
Very high cycle fatigue (VHCF) steels can withstand a cycling loading above 108 cycles before fatigue failure. This type of steel is essential for reliable and long-life mechanical components which are subjected to both mean residual stress and alternating cycling stress such as, gears, bearings, springs, and shafts.
Fatigue failures are intergranular brittle fractures, which occur due to the weakening of grain boundaries under prolonged cyclic loading even though the induced stresses are well below the tensile and/or compressive strength of the material.
OM and SEM of the carburizing layer: (a) optical microscope microstructure of the carburizing layer and (b) electron microscope microstructure of the carburizing layer. Image Credit: Yang, S et al., Coatings
Under high stress, cracks are initiated on the surface of VHCFs, whereas under low-stress conditions, cracks are formed below the surface. The fatigue failure mechanism begins with the formation of granular bright facet (GBF) region around the internal nonmetallic inclusion beyond 106 cycles and extends into a fisheye zone, called crack initiation characteristic zones, which consume the majority of total fatigue failures. In the case of VHCFs, the GBF region has a very fine granular microstructure.
About the Study
In this study, low carbon gear steel (18CrNiMo7-6) specimens from 80-mm-diameter hot-rolled bars were machined into hour-glass shapes with finishing margins followed by a series of gradient carburizing heat treatment processes at 930 ℃ and 860 ℃.
Then, the specimens were tempered at 650 ℃ for 2 hours followed by air-cooling and again heating at 840 ℃ for 2 hours and oil-quenching with a carbon potential of 0.70% to avoid decarburization. Finally, two low-temperature temperings were performed at 180 ℃ for 6 hours.
Subsequently, the specimens were tested under axial ultrasonic loading at room temperature (25 ℃), stress ratio (R) of -1, and the frequency of 20 kHz in the VHCF regime.
The fracture morphology and the chemical composition of non-metallic inclusions were analyzed by scanning electron microscopy (SEM) and energy dispersive X-ray spectrometer (EDS), and the distribution and size of the FIE and GBF regions were measured. Transmission electron microscopy (TEM) and electron backscatter diffraction (EBSD) was used to analyze the fracture surface of the GBF area.
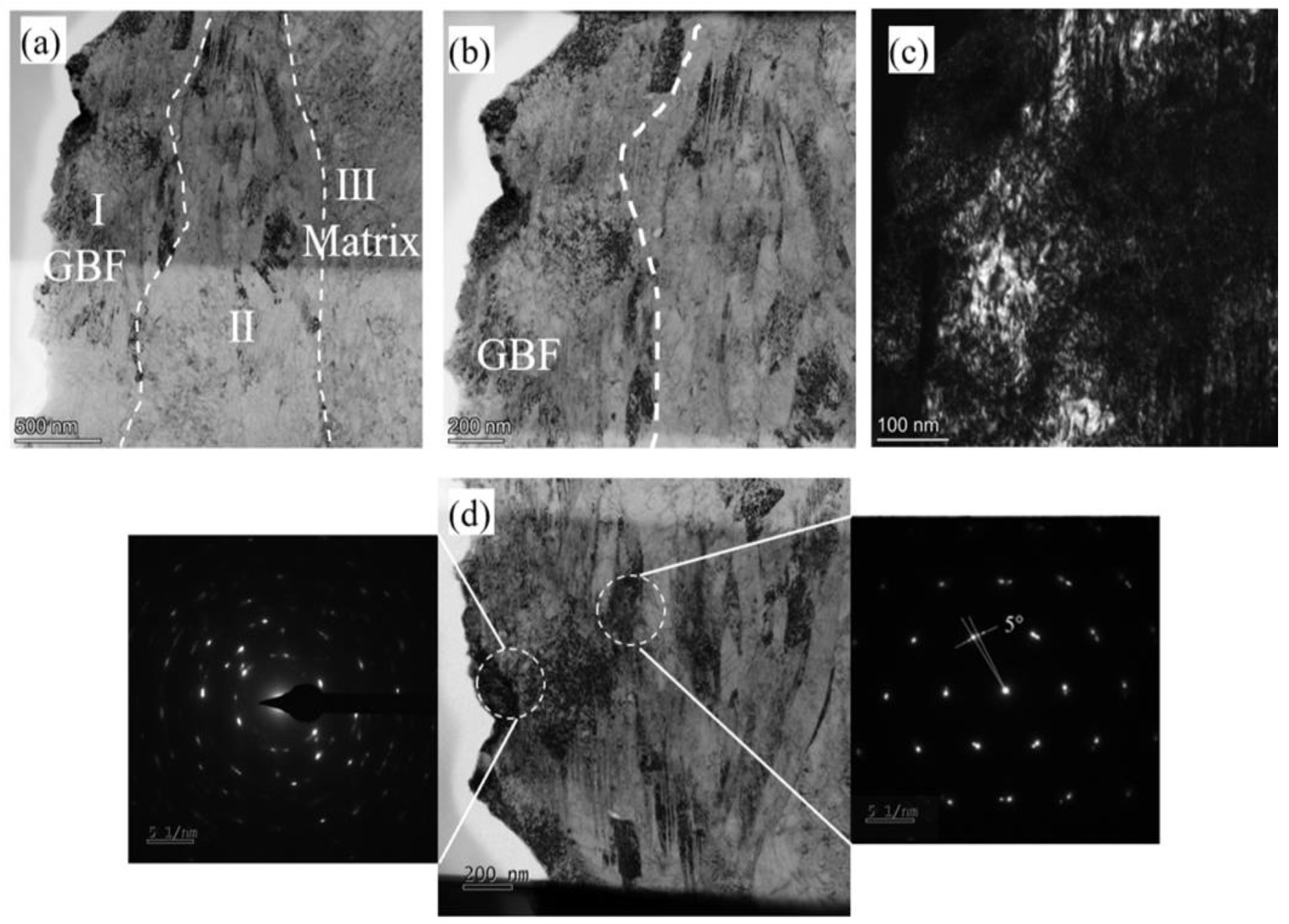
TEM bright field image together with the SAD patterns in the GBF area of the carburized specimen after the VHCF tests at σa = 590 MPa for Nf = 6.66 × 107. (a) is transmission morphology of GBF region, transition region and matrix, (b) is transmission morphology of GBF region, (c) is GBF region transmission amplification morphology, (d) is the location of the selected area diffraction. Image Credit: Yang, S et al., Coatings
Observations
The SEM images showed that the carburized surface layer consisted of acicular martensite, retained austenite, and carbides. Moreover, the microstructure at 1.0 mm away from the surface of the carburized specimen mainly consisted of lath martensite and carbide with a small amount of little residual austenite and acicular martensite. Thus, gradient carburization from the surface towards the core was confirmed.
Furthermore, 99% of the life of the crack initiation was mainly consumed in the GBF region. The stress intensity factor (SIF) of GBF region ΔKGBF can be regarded as the threshold value for the crack initiation.
When the SIF at the crack edge was less than the threshold value, the fatigue short crack did not expand and directly formed a fisheye. Conversely, when the SIF was higher than the threshold value, the short crack formed a GBF nano grain layer. Similarly, when the SIF was less than the critical value required for crack growth, the fatigue long crack did not grow, and a fatigue fracture occurred suddenly.
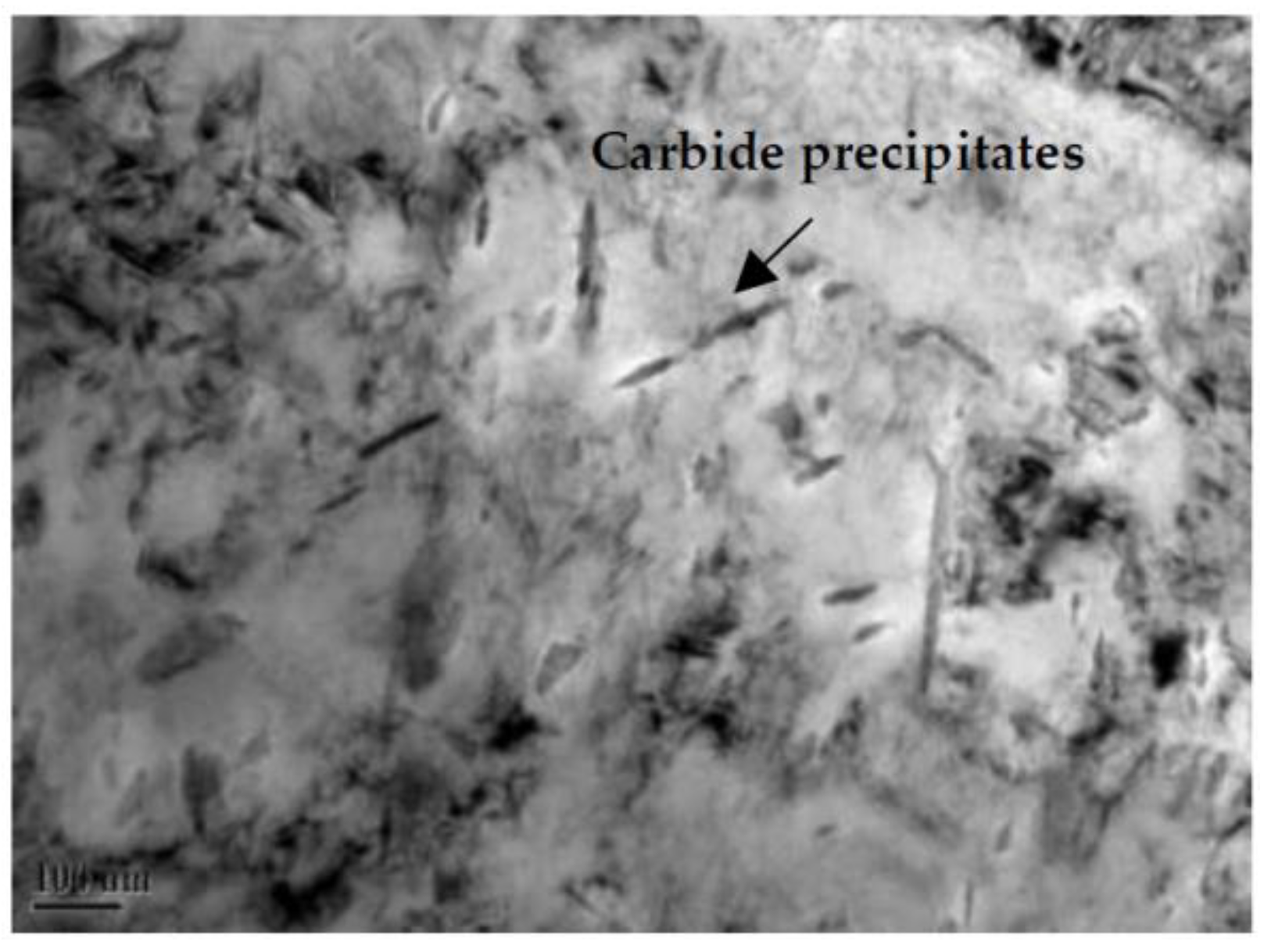
TEM characterization of the carbide precipitates. Image Credit: Yang, S et al., Coatings
Conclusions
The researchers synthesized low carbon 18CrNiMo7-6 gear steel specimens using a gradient carburizing heat treatment process followed by ultrasonic fatigue tests. The GBF and fisheye regions were characterized thoroughly, and the formation mechanism was revealed.
The specimens showed VHCF behavior with a fatigue limit at 109 cycles under 500 MPa stress. The fatigue crack initiation sites of the gradient carburized specimens were mostly located
in the range of 0.9 to 1.4 mm below the surface, where the hardness was about 580 HV. It was because the core did not show VHCF phenomena, and the surface had a higher hardness. The GBF region had a fine nanograin layer formed by a small plastic deformation caused by long-time circulation under low stress. Thus, the new 18CrNiMo7-6 alloy is proven to be a suitable material for reliable and durable cyclically loaded mechanical components.
Reference
Yang, S., Cheng, P., Hu, F., Yu, W., Zhang, C., Wang, K., Wang, M., Very High Cycle Fatigue Properties of 18CrNiMo7-6 Carburized Steel with Gradient Hardness Distribution. Coatings 2021, 11, 1482. https://www.mdpi.com/2079-6412/11/12/1482
Disclaimer: The views expressed here are those of the author expressed in their private capacity and do not necessarily represent the views of AZoM.com Limited T/A AZoNetwork the owner and operator of this website. This disclaimer forms part of the Terms and conditions of use of this website.