The newest research in Materials looked at the thermo-mechanical performance of additively made Carbon Fiber Reinforced Polymer (CFRP) with incorporated Fiber Bragg Grating (FBG) sensors and their suitability for use under thermal stress.
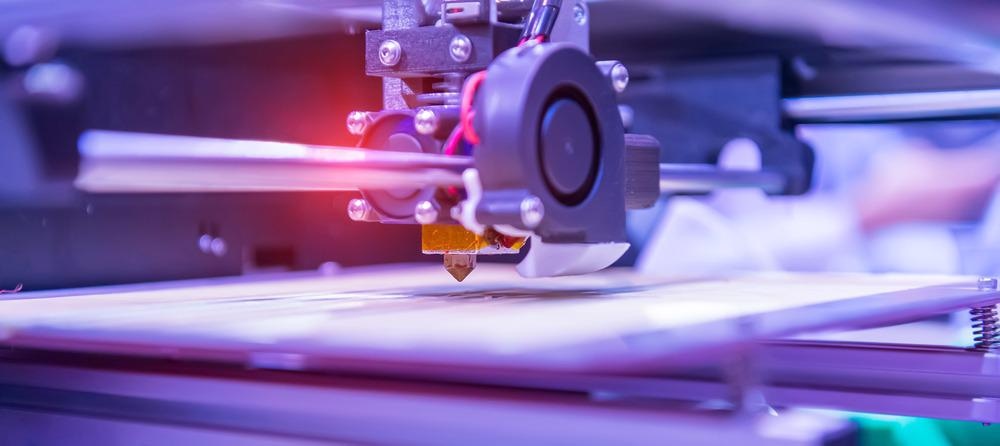
Study: Model of the Temperature Influence on Additively Manufactured Carbon Fibre Reinforced Polymer Samples with Embedded Fibre Bragg Grating Sensors. Materials, 15(1). 222. Available at: https://www.mdpi.com/1996-1944/15/1/222 (registering DOI) Image Credit: asharkyu/ Shutterstock.com
Introduction to Additive Manufacturing
Additive Manufacturing (AM), also known as 3D printing, is a layer-by-layer manufacturing technique in which subsequent sheets of materials are accumulated above one another to achieve the complete item using a computer-aided design.
Because of recent technological advancements and the recent trend toward a more green lifestyle, it has been commonly used in industrial implementations such as aerospace, automobiles, orthodontic, structural, and healthcare industries for the manufacture of functional designs, especially with complicated geometrical topologies, because it offers outstanding design freedom when compared to traditional fabrication techniques.
Image Credit: Shafighfard, T. & Mieloszyk, M., Materials
As a result, it is expected that additive manufacturing (AM) will be the 3rd industrial transformation, supplementing the production line assembly that ruled manufacturing beginning in the previous century.
Improvements in Composites
The advancement of technology was not restricted to production processes. Connecting with manufacturing methods, one of the primary objectives of scientific innovation has been to make materials more productive, e.g., smart materials.
As a result of its high rigidity proportion, as well as corrosion protection, decorativeness, and heat resistance, polymer nanocomposites have seen a tremendous increase over the last decade. Their inherent sensing capabilities, on the other hand, make them excellent for Structural Health Monitoring (SHM) in aeronautical and industrial engineering disciplines.
Advantages of Fiber Bragg Grating (FBG) Sensor
Surface-mounted photodetectors have received a lot of importance in the study of stress analysis and composites condition monitoring. Fibre Bragg grating (FBG) sensors have been favored over other types of sensors for incorporation into composites constructions due to their compact size and lightweight, resistance to corrosion, combinatorial capabilities, and fast response.
An FBG sensor is a sort of dispersed Bragg reflection built into a short section of optical fiber that reflects specific wavelengths while transmitting all others. The lack of trustable dependable in-situ surveillance for attempting to control the construction process and quality of the final product has stifled the development of AM innovation, so integrating FBG detectors within laminated composites is required for legitimate surveillance of temperature variations and measurement techniques of induced residual strains.
Embedding Techniques of FMG Sensors
During the production process, conventional techniques might be used to implant FBG detectors into composite samples. FBG sensors might be added to additively created pure polymer samples using processes such as multi-jet printing or Fused Deposition Modelling (FDM). It was demonstrated that by merging pure polymers with short and/or continuous fiber when 3D printing with the FDM process, the structural capacity of the polymeric materials may be greatly enhanced.
Limitations of FMG Sensor Embedding
Despite the benefits of the FDM technique for fabricating composite structures, it is not without flaws. The potential faults associated with the FDM process have a detrimental impact on the quality and durability of real applications. Temperature variations are the most common type of defect that generates errors in the sample throughout the production process because it experiences consecutive melting and quick chilling phases of the substrate material. It can provide harmful stress distribution, which can lead to debonding breakdown. As a result, the thermal record of the created object should be investigated using the FDM process.
Research Findings
There were discrepancies in the characteristics of the PLA material and the earlier described M3 crystal, which was also made using a 3D printer. Instead of a linear model, a second-degree polynomial was used to represent the connection between strain and temperature in M3 crystal. The observed disparities across materials can be attributed not just to material attributes but also to the production process utilized. The M3 crystal samples were created using the multi-jet printing (MJP) technology, whilst the PLA was created using FDM.
The material behavior corresponding to the effect of the temperature on the CFRP samples was modeled using the Finite Element Method (FEM).
The mean strain fluctuation measured for all detectors was 5 × 10−6, but the interrogator's measurements were 2 × 10−6. All strain gauge graphs have the same form as the temperature curve.

Total strain: (a) Embedded sensors, (b) sensors on the surfaces, (c) free sensor, and (d) temperature; S1, S2, S3—CFRP samples. Image Credit: Shafighfard, T. & Mieloszyk, M., Materials
The quadratic link was obvious. The error for a CFRP 3D-printed sample used in this investigation was determined to be 2%. This inaccuracy may be regarded as statistically insignificant and hence removed from statistical analysis.
In a nutshell, a 4-layer composites omnidirectional lamination was created using the AM, FDM process. The numerical findings were compared to the mean strain rates for three samples taken twice. The findings of this work might be used to motivate additional research into AM methods for composite constructions with embedded FBG sensors.
Further Reading
Shafighfard, T. & Mieloszyk, M., 2022. Model of the Temperature Influence on Additively Manufactured Carbon Fibre Reinforced Polymer Samples with Embedded Fibre Bragg Grating Sensors. Materials, 15(1). 222. Available at: https://www.mdpi.com/1996-1944/15/1/222
Disclaimer: The views expressed here are those of the author expressed in their private capacity and do not necessarily represent the views of AZoM.com Limited T/A AZoNetwork the owner and operator of this website. This disclaimer forms part of the Terms and conditions of use of this website.