In a recent study published in the journal Additive Manufacturing, researchers from China developed a post-fabrication polishing method for the interior of 3D printed metallic parts that incorporated a combination of electrochemical and mechanical polishing (EMCP) processes.
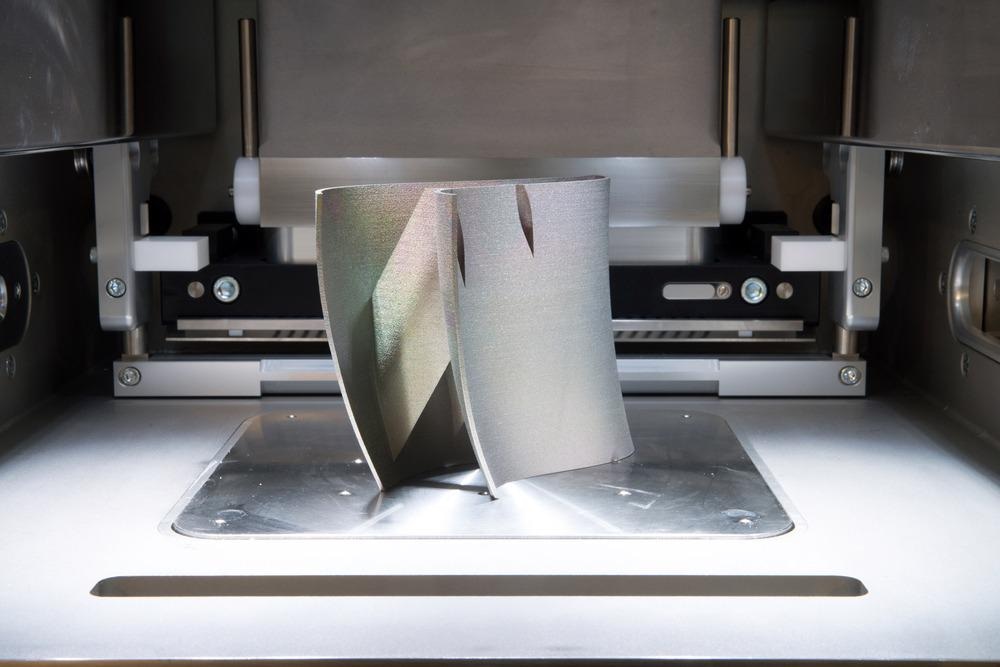
Study: Combined electrochemical and mechanical polishing of interior channels in parts made by additive manufacturing. Image Credit: Moreno Soppelsa/Shutterstock.com
One of the common issues with freshly prepared 3D printed metal parts is their relatively poor surface qualities due to band protrusions, staircases, power adhesion, and balling that make them unsuitable for high-performance applications.
The purposed EMCP with electrochemical dissolution, and coarse and fine mechanical grinding, effectively removed the band protrusions, the passivation film and residue products generated during electrochemical machining, and the adhesive powders. With the highest contribution of 72.2% from the electrochemical machining, the roughness values Sa and Sq were reduced by approximately 71.2% and 68%, respectively.
Post-Fabrication Polishing of 3D Printed Metal Parts
3D printing of metal parts belongs to a class of metal additive manufacturing (MAM), which is used for rapid prototyping and integration of complex components. One such application is complex fluid channels of automobiles, aircraft, and rocket engines, in which interior surface morphology of the flow channels affects the desired streamline flow of fuel and air, causes attrition and influences combustion. Hence, post-fabrication polishing of these intricate fluid channels significantly improves the reliability and stability of the associated equipment.
Several methods to enhance the surface quality of interior channels include electrochemical polishing, mechanical grinding, and abrasive flow polishing. Mechanical grinding of deep, narrow, and curved fluid channels is almost impossible.
Other than that, non-uniformity, high surface irregularities, and low material removal rate are some of the major fundamental issues associated with mechanical grinding. Even though abrasive flow polishing gives more improved surface quality than mechanical grinding, the non-uniform material removal reduces the dimensional accuracy of the curved surfaces. Meanwhile, due to the absence of mechanical force and tool wear, electrochemical polishing is suitable for finishing inner surfaces of curved channels.
About the Study
In this study, researchers used a novel EMCP method consisting of a fine grinding wheel (FGW), a coarse grinding wheel (CGW), a fine grinding wheel (FGW), and a cathode for electrochemical machining of interior channels of narrow straight and curved 316LSS workpiece.
More from AZoM: Producing Bioprinting Material with Microbes
The CGW and FGW were made up of tough nylon fiber wire with a heat-resistant binder and sharp abrasives of granularity 180# and 300#, respectively. The cathode was placed in a flowing 20 wt% NaNO3 electrolytic solution at 25 ℃ along the axis between CGW and FGW to ensure a constant electrode gap and uniform dissolution of the acting anode workpiece.
The workpiece was further subjected to a rotational motion and a reciprocating feed motion along the axial direction to improve the uniform machining along the circumferential and axial direction, respectively. Initially, the CGW removed the adhesive powders, the electrochemical machining incorporating high current density removed the band-protrusions, and the FGW removed the residue electrolytic products and passivation film, respectively.
Observations
Analyzing three feed rates viz. 0.5, 0.1, and 0.02 mm/min, successively, the surface roughness of the 316LSS workpiece decreased with the decrease in the feed rate. However, the feed rate of 0.02 mm/min resulted in an out-of-tolerance limit interior channel diameter of 31.1 mm compared to the initial aperture diameter of 30 mm at the machining location of the straight workpiece.
Hence, 0.1mm/min was considered as the optimal feed rate. Moreover, both CGW and FGW individually demonstrated roughness reduction ratios of 10% and 15%, respectively. The electrochemical machining process contributed to more than 72.2% of the total surface roughness reduction, which was expressed in terms of percentage weight loss.
In the case of the curved 316LSS workpiece, the roughness values were the highest (Sa = 5.49vμm, Sq = 8.82 μm) at the curvature in the middle of the channel. Further, the tests were carried out for narrow specimens of diameter 5 mm and 9 mm, respectively. In this case, Sa of straight and curved channels significantly decreased from 15.92 and 18.18 μm to 5.06 and 6.02 μm, i.e. 71.2% and 68% decrease, respectively.
Conclusions
In summary, the researchers of this study prepared both narrow and wider straight and curved fluid channels of 3D printed 316LSS stainless steel to analyzed the effectiveness of the EMCP polishing method. The purposed EMCP comprised four main components viz. an FGW, a CGW, a cathode along the axial direction, and the acting anode workpiece.
As evidenced from the weight loss and surface roughness measurement, it effectively removed adhesive powders, band protrusions, electrochemical residue products, and the passivation film. Also, the electrochemical machining contributed to maximum surface polishing than the other two mechanical grinding methods. Hence, EMCP is a promising combined method to polish the interiors of 3D printed metal parts.
Disclaimer: The views expressed here are those of the author expressed in their private capacity and do not necessarily represent the views of AZoM.com Limited T/A AZoNetwork the owner and operator of this website. This disclaimer forms part of the Terms and conditions of use of this website.
Sources:
An, L., Wang, D., Zhu, D., Combined electrochemical and mechanical polishing of interior channels in parts made by additive manufacturing, Additive Manufacturing, 2022, 102638, ISSN 2214-8604
https://www.sciencedirect.com/science/article/pii/S2214860422000446