Additive manufacturing, more commonly known as 3D printing, has seen increasing application in multiple industries in the past couple of decades for multiple uses. A research paper currently in the pre-proof stage of publication in the journal Additive Manufacturing has investigated the 3D printing of silica glass components.
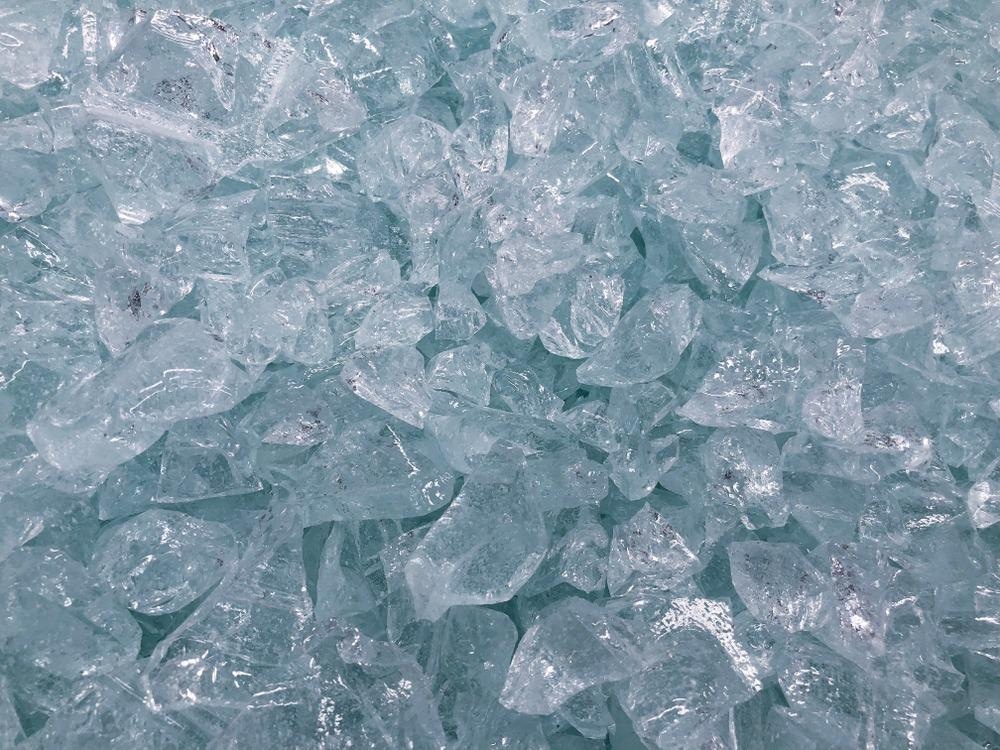
Study: Hybrid additive manufacturing for the fabrication of freeform transparent silica glass components. Image Credit: Mitzxxz/Shutterstock.com
3D Printing Ceramic and Glass Materials
Additive manufacturing techniques for printing ceramic and glass materials have been extensively developed in recent years. Each 3D printing technology has proven best suited to specific feedstocks, component designs, and dimensional scales. Each technique possesses specific requirements for successful printing, limiting their wider applicability for printing ceramic and glass materials.
Direct ink writing is a commonly used 3D printing technique in multiple industries. In this technique, ceramic powder suspensions are used to produce a shear-thinning ink that is extruded from a nozzle in accordance with a pre-set digital design. Proper ink design is fundamental for the final product’s shape retention. A major drawback of this technique is the absence of support and the extruded material’s viscoelectric character, which limits the complexity of printed designs.
Stereolithography and digital light processing are vat polymerization techniques that use selective curing of photosensitive resins which contain dispersed ceramic particles to fabricate a 3D component. Slurries used in these technologies require low viscosity and photosensitivity. However, suspended particles can increase the slurry’s viscosity and increase light scattering and absorption of photons, decreasing curing depth, resolution, and printed part’s rigidity.
Hybrid Techniques
Recently, hybrid techniques have been proposed to overcome the limitations of each specific technique and improve the fabrication of ceramic and glass materials using additive manufacturing. One method proposed is a hybrid UV-assisted direct ink writing technique. This hybrid technique combines the advantages of both processes.
The filament shape is controlled by the nozzle, removing the influence of scattering and adsorption phenomena on the printing process’s resolution. Photopolymerization of the extruded filament facilitates the fabrication of solid green bodies and more complex architectures with fewer rheological constraints. Freedom of form can be better realized, with overhangs, undercuts, and filigreed patterns which are self-supporting able to be manufactured. Extremely fast solidification can be facilitated.
The Study
So far, there have been few examples of conventional structures printed with this hybrid additive manufacturing process, focusing on generating more severe overhangs and better print stability. To the author’s knowledge, studies have been limited to proof-of-concept simple coils for exploring the freeform capabilities of the technique using ceramic and polymeric feedstocks.
In the pre-proof paper in Additive Manufacturing, the authors have explored the fabrication of honeycomb-structured 3D architectures made from transparent silica glass feedstocks. They have explored the full capabilities and limitations of the hybrid UV-assisted direct ink writing technique in the research.
A main advantage of this hybrid technique for this purpose is the ability to manufacture structures where the transparency is not limited by traditional conventional layer-by-layer deposition techniques. Conventional techniques produce numerous interfaces in the multiple layers printed. By solidifying the structures using photopolymerization, these interfaces are removed, and continuous extrusion using nozzles aid the fabrication of complex architectures.
Traditional additive manufacturing processes have been used to print transparent silica glass devices, with the inks employing single silica sources, either silica nanoparticles or silicon alkoxides. The former source creates more stable inks that possess higher ceramic yield and less shrinkage, whereas the latter creates a more homogenous ink that can be sintered at lower temperatures.
The proposed technique in the study makes use of both fumed silica and silicon alkoxides. In doing so, the benefits of both are exploited. The printed inks possess appropriate rheology and high homogeneity. Additionally, the printed components possess higher transparency and density. Additionally, the technique does not require the high temperature and lasers during printing that are necessary for other 3D printing techniques for producing glass structures, and printed architectures with sparse structures can be produced with better dimensional accuracy.
Rheological properties were controlled by tailoring particle-liquid interactions with blends of acrylates and the addition of TEOS. Faster debinding and sintering treatments were achieved despite the ink’s low particle loading.
The final printed components possessed superior mechanical properties, and agreed with the CAD design, with a homogenous, amorphous structure. Furthermore, the honeycomb-like structure was lighter than convention 2D extruded alternatives. This facilitates their use as scaffolding and metrology frames for devices that require lightweight, transparent components. Moreover, as there are no excess materials that need cleaning to remove after printing, the use of solvents and the risk of part damage are avoided.
As noted by the authors, further opportunities exist for exploring the use of robotic arms for extrusion head carriers to expand the hybrid technology’s spatial capabilities, and the use of coaxial nozzles to allow extrusion of multi-material filaments where only the outer layer needs curing. The interior could be composed of inks that can be removed to create a complex, hollow, tubular shape. There exist exciting possibilities for the technology in fields such as optics and sensors.
Further Reading
De Marzi, A et al. (2022) Hybrid additive manufacturing for the fabrication of freeform transparent silica glass components [pre-proof] Additive Manufacturing 102727 | sciencedirect.com. Available at: https://www.sciencedirect.com/science/article/pii/S2214860422001312
Disclaimer: The views expressed here are those of the author expressed in their private capacity and do not necessarily represent the views of AZoM.com Limited T/A AZoNetwork the owner and operator of this website. This disclaimer forms part of the Terms and conditions of use of this website.