A team of researchers from Spain has published new research in the journal Materials analyzing the properties of waste product-filled sustainable mortars. The study has implications for valorizing waste streams and improving the circularity and sustainability of the construction industry.
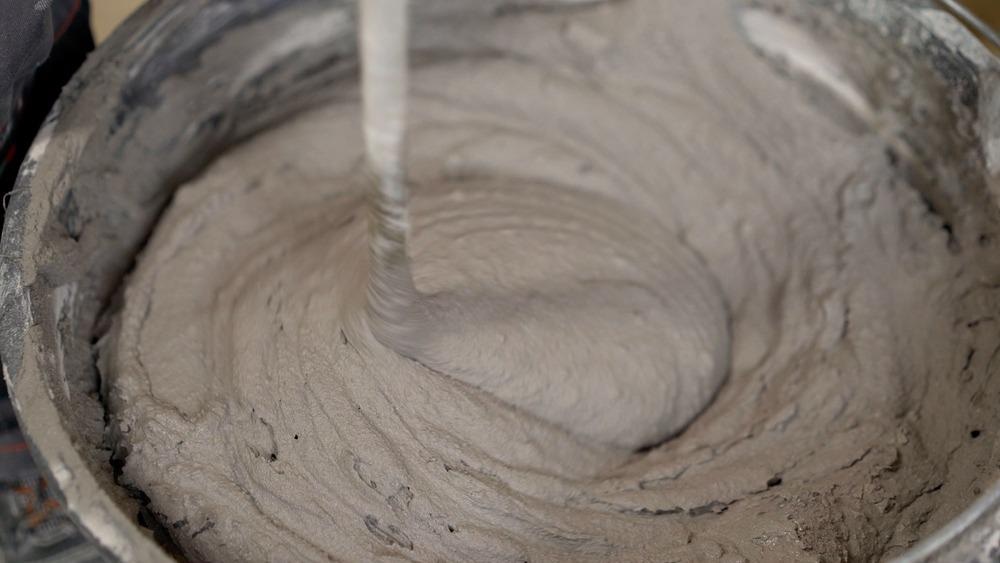
Study: Performance of Sustainable Mortars Made with Filler from Different Construction By-Products. Image Credit: Sidorov_Ruslan/Shutterstock.com
The Construction Industry, Mortar, and Sustainability
Waste is a critical issue in the construction industry. Several materials are used in building projects, including concrete, glass, steel, and aggregate materials, and the production of these critical construction materials causes vast amounts of greenhouse gas emissions. Taken together, the construction industry’s emissions and waste cause huge environmental issues and present issues with sustainability that have facilitated the need to develop new processes for manufacturing construction materials.
Mortar is a critical material in the construction industry. It is used for applications such as repairing, binding, and coating. The additional solid surface of filler’s powdery particles acts as a site of nucleation and hydrate growth. Most mortars are composed of varying amounts of sand, cement, and water.
Recent figures have highlighted that the amount of waste generated by the construction industry is accelerating as the world rapidly urbanizes and industrializes. The utilization of waste materials has been a focus of materials science research and the construction industry. Doing so vastly improves the circularity of the industry and reduces harmful emissions from the production of traditional construction materials such as Portland cement.
Correlation between fresh density in mortars and specific gravity of the fillers used in mortars. Image Credit: López-Uceda, A et al., Materials
Utilizing Waste Products
Over the past few years, the idea of using waste materials as aggregates and in cementitious materials has facilitated increased research focus. Studies have demonstrated that construction waste and industrial by-products can improve properties such as compressive and flexural strength in mortars. Scientists have evaluated numerous materials.
For instance, a 20% replacement ratio of sanitary ware as a cementitious filler in mortars can improve the compressive and flexural strength of the materials, as well as reduce shrinkage. Hot-mix asphalt aggregate waste reduces shrinkage and improves the mechanical properties of self-compacting cement compared to silicious fillers. Ornamental rock increases the compressive strength in mortars, and this increase is related to the incorporation ratio.
Replacing natural sand with powdered granite increases both the adhesive strength and drying shrinkage of mortars. Other studies have investigated by-products such as non-conforming fly ash and recycled masonry waste sand.
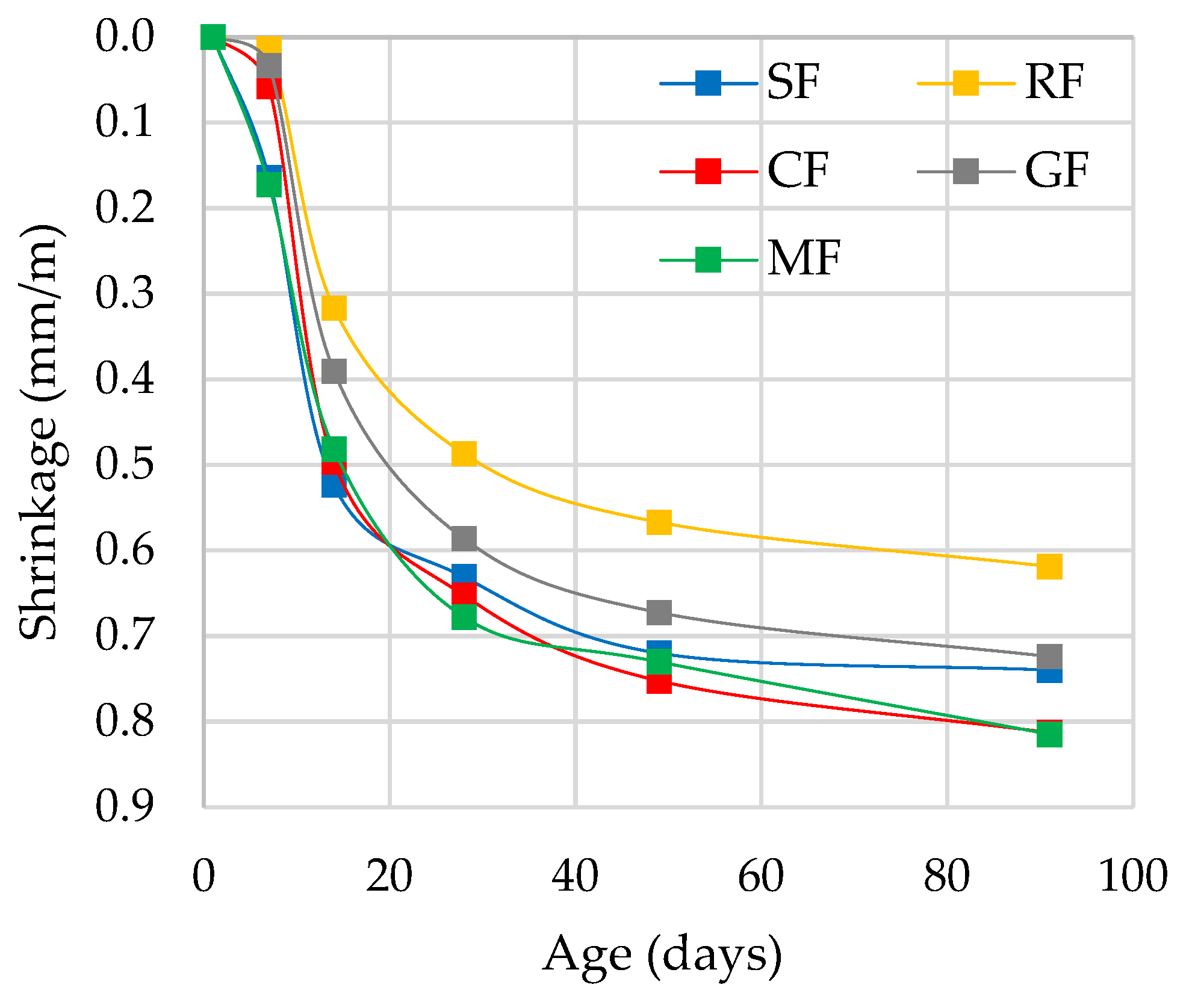
Shrinkage of mortars over time. Image Credit: López-Uceda, A et al., Materials
The Study
The authors have investigated the effect of incorporating four different construction wastes to produce sustainable mortars. As stated by the authors, most of the current studies in the literature have investigated no more than two wastes, meaning that this study improves the current knowledge base.
The research used a silicious filler as a reference mix. Waste materials studied by the researchers were ceramic waste from construction and demolition waste treatment plants, ornamental rocks, granite, and waste from hot-mix asphalt drying processes. All four wastes are generated in significant quantities globally, making their reuse important for the construction industry in order to reduce the amount of waste entering landfill sites.
Properties of both fresh and hardened mortars after waste product incorporation were evaluated in the research. Important properties of fresh mortars studied included workability, density, and air content. Dried properties investigated included shrinkage, permeability to water vapor, water absorption, and strength (compressive, flexural, adhesive.) Various properties were tested over periods of 91 days and 180 days.
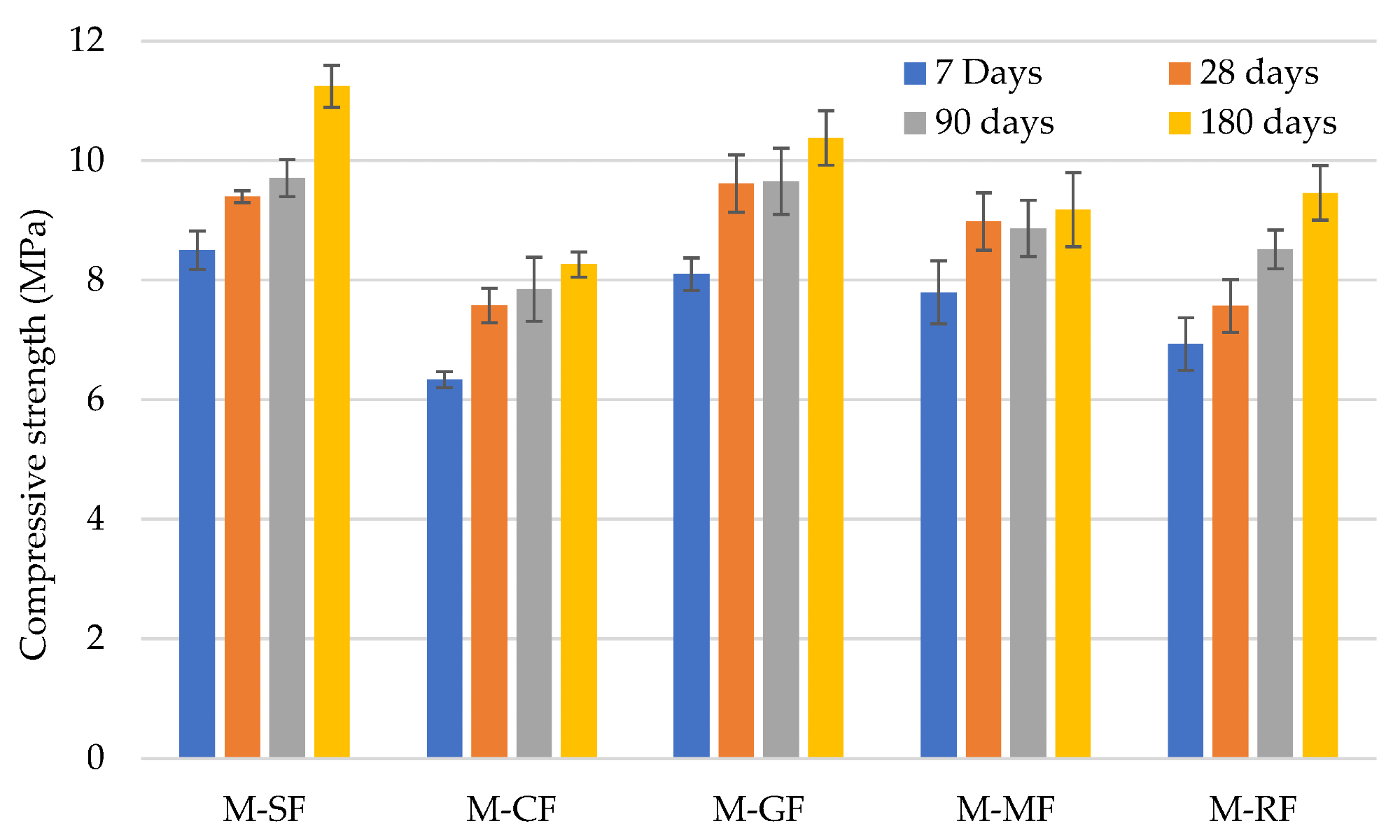
Compressive strength of mortars over time. Image Credit: López-Uceda, A et al., Materials
Conclusions of the Study
Several conclusions were highlighted in the research. The conclusions demonstrated the viability of using the four waste materials as sustainable fillers for mortar.
The incorporation of the waste by-products did not substantially affect the fresh properties of studied mortars compared to silicious filler materials. An exception was the use of granite filler, which had effects on workability and air content.
No significant difference in durability was observed between the reference mortar and the waste by-product modified mortars. Observed shrinkage in the sustainable mortars was less than 1mm/m, which is comparable to Ordinary Portland Cement. Compared to the reference mortar, the mortars in the experiment displayed differences in water absorption of ±23%. The mortars produced in the study display reduced water vapor permeability compared to the reference mortar.
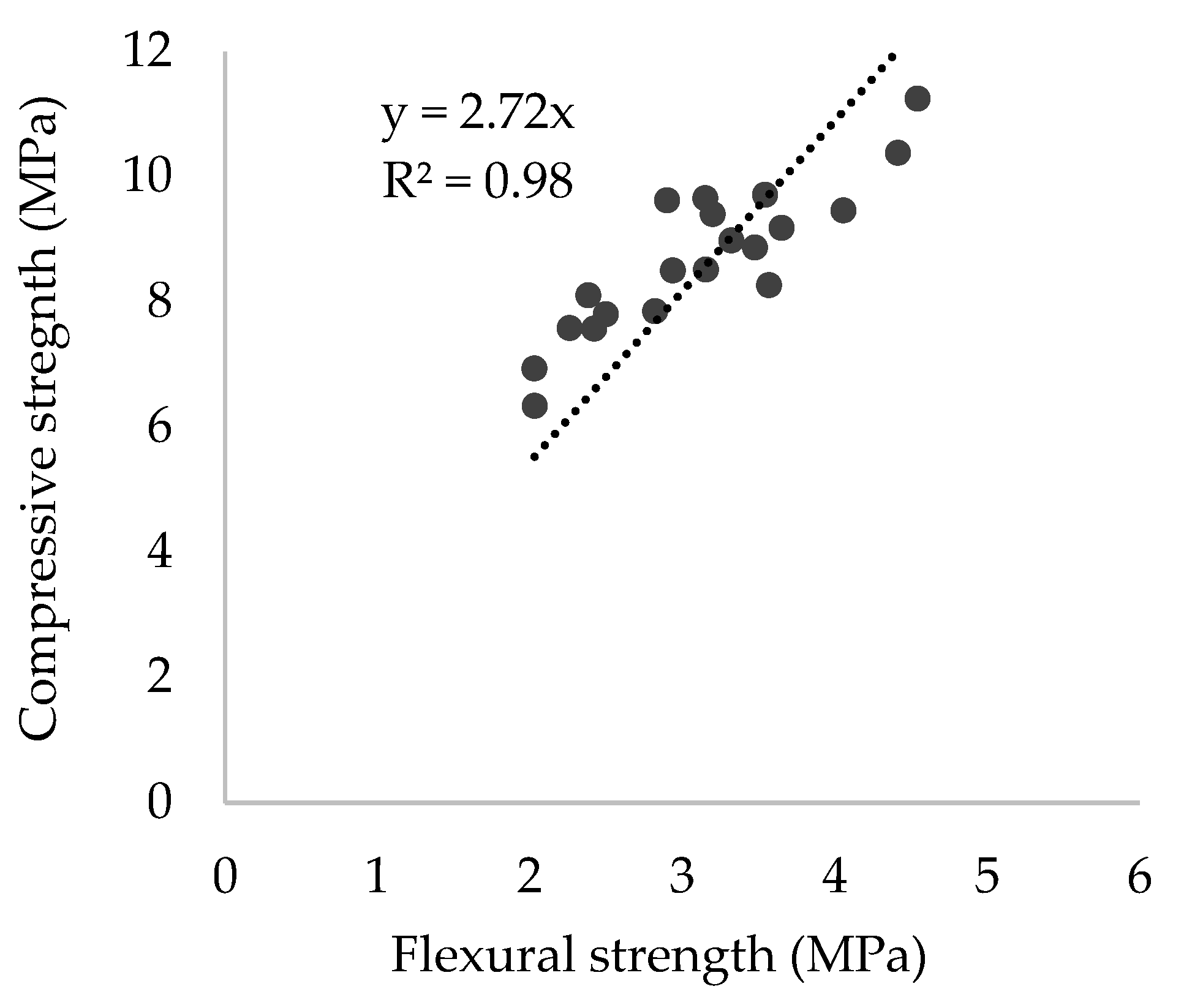
Correlation between flexural strength and compressive strength. Image Credit: López-Uceda, A et al., Materials
The mechanical behavior of the produced mortars was favorable. The adhesive strength was higher than the reference mortar. However, the incorporation of construction by-products had a negative impact on compressive and flexural strength. Due to this, the authors have stated that the best use for these mortars is for coating and rendering applications.
Moreover, incorporating construction waste by-products into mortars can be a valid alternative to conventional fillers, improving the sustainability and environmental friendliness of the construction industry. By valorizing construction waste in mortars and cementitious materials, building projects in the future will be more in line with the concept of the circular industry.
Further Reading
López-Uceda, A et al. (2022) Performance of Sustainable Mortars Made with Filler from Different Construction By-Products [online] Materials 15(7) 2636 | mdpi.com. Available at: https://www.mdpi.com/1996-1944/15/7/2636
Disclaimer: The views expressed here are those of the author expressed in their private capacity and do not necessarily represent the views of AZoM.com Limited T/A AZoNetwork the owner and operator of this website. This disclaimer forms part of the Terms and conditions of use of this website.