A new paper published in the journal ACS Engineering Au has investigated the experimental quantification of gas dispersion in catalyst structures produced by additive manufacturing. Non-destructive testing is used to inform future structured catalyst design. The research has been performed by scientists from the Eindhoven University of Technology in the Netherlands.
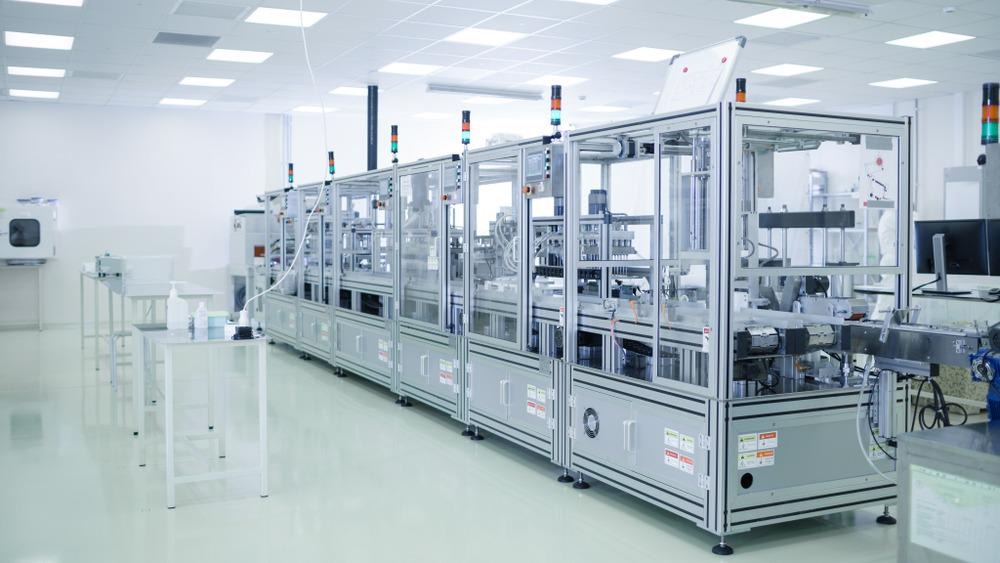
Study: Experimental Quantification of Gas Dispersion in 3D-Printed Logpile Structures Using a Noninvasive Infrared Transmission Technique. Image Credit: Gorodenkoff/Shutterstock.com
Structured Catalysts
Structured catalysts have the benefit of an enhanced surface area without prohibitive process costs. By structuring material, gas holdup can be controlled, more intense phase mixing can be achieved, and a lower pressure drop maintained. By optimizing the catalyst’s specific geometry, trade-offs between mixing, temperature control, and enhanced solid-fluid contact at a low-pressure drop can be managed.
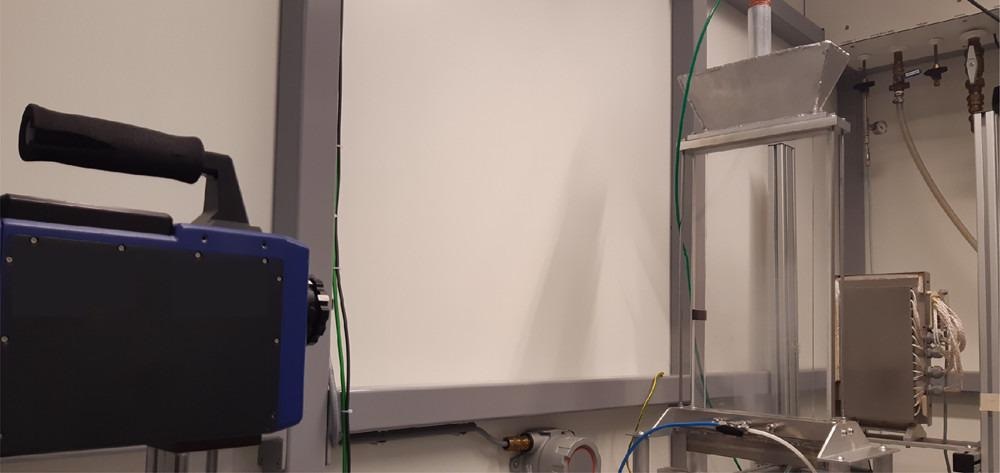
Experimental setup consisting of the IR source on the right, quartz glass column in the middle, and IR camera on the left. Image Credit: Rousseau, L.R.S et al., ACS Engineering Au
This contrasts with catalyst beds, which suffer from a high-pressure drop and the presence of hot spots in materials. Structured catalysts are conventionally manufactured by coating foams and honeycomb monoliths, or are manufactured as extrudates.
Additive Manufacturing
Additive manufacturing, otherwise known as 3D printing, is a manufacturing process that possesses the benefits of design freedom, reduced material waste, and multi-material processing and printing. This relatively new field of manufacturing has powerful potential for improving the properties of structured catalysts. Benefits include design freedom and the ability to produce large structures with localized features.
Several different additive manufacturing processes have been developed over the years, including direct ink writing, stereolithography, digital light processing, selective laser melting, and selective heat sintering. How beneficial 3D printing is for the synthesis of structured catalysts depends on the technique employed.
Amongst the various additive manufacturing processes available, direct ink writing is a mature process. In this additive manufacturing technique, a viscous material slurry is extruded from a nozzle according to a pre-determined design. The material is then deposited layer-by-layer to build the component. Direct ink writing has the added benefit of multi-material processing and multiple extrusion capabilities.
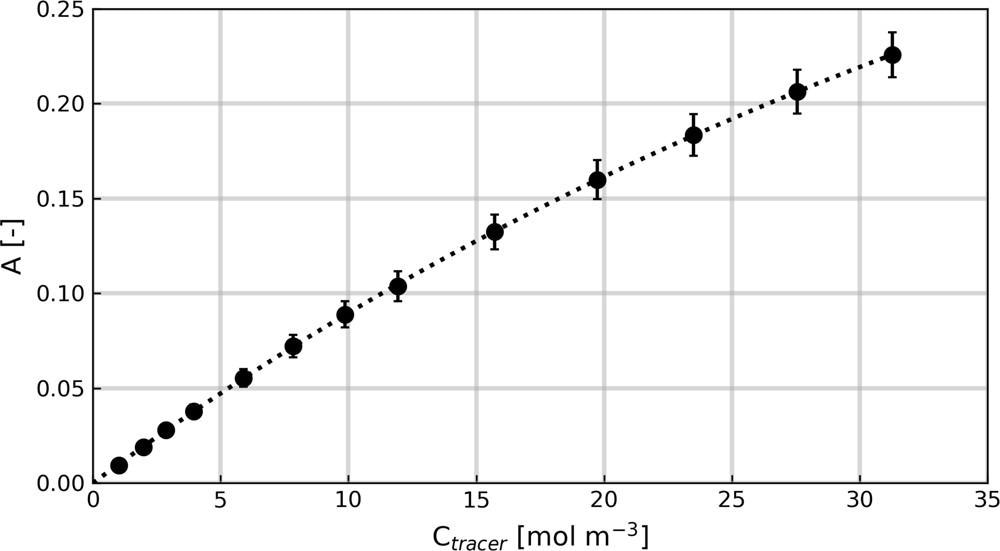
Calibration data with standard deviation (dots) and fitted curve (dotted line). Image Credit: Rousseau, L.R.S et al., ACS Engineering Au
Manufacturing Logpile Structured Catalysts
Before devices are 3D printed, a viscous slurry of ceramic particles, binders, and diluent is prepared for extrusion. Many studies have produced catalysts with monolith-like logpile structures. These structures can possess either a staggered or straight configuration. In a staggered configuration, features in the axial direction are offset from each other in each layer, whereas in a straight configuration, they are parallel to each other.
Changing the printed features’ size and the size of the aperture between them can be utilized during extrusion to vary the structure’s geometry and control the porosity of the final printed construct. Critical parameters such as rheological properties and printer settings are used to control the final properties of printed materials, such as catalytic activity, porosity, and mechanical strength. Logpiles have several benefits compared to conventional honeycomb-structured monoliths.
Logpile structures have benefits for structured catalysts, including allowing reactants to travel transversely and broader operating windows. Moreover, heat transfer can be enhanced due to the transverse dispersion a logpile structure facilitates. This improves the catalyst’s chemical processes and avoids thermal effects which can lead to material degradation. The catalyst’s performance, durability, and selectivity are also improved.
The Study
The new paper has considered the use of direct ink writing methods for the purpose of manufacturing structured catalysts. Recent studies have employed direct ink writing to manufacture several ceramic-like catalysts, including metal-organic frameworks and zeolites, and catalyst support materials including alumina and silica. The extensive use of direct ink writing in producing catalysts and support materials has proven the technology’s maturity in this field of research.
In the study, non-destructive techniques have been employed to quantify transverse dispersion in direct ink writing-manufactured logpile structured catalysts. The technique employed for quantification in the research is a noninvasive, instantaneous, and whole-field technique.
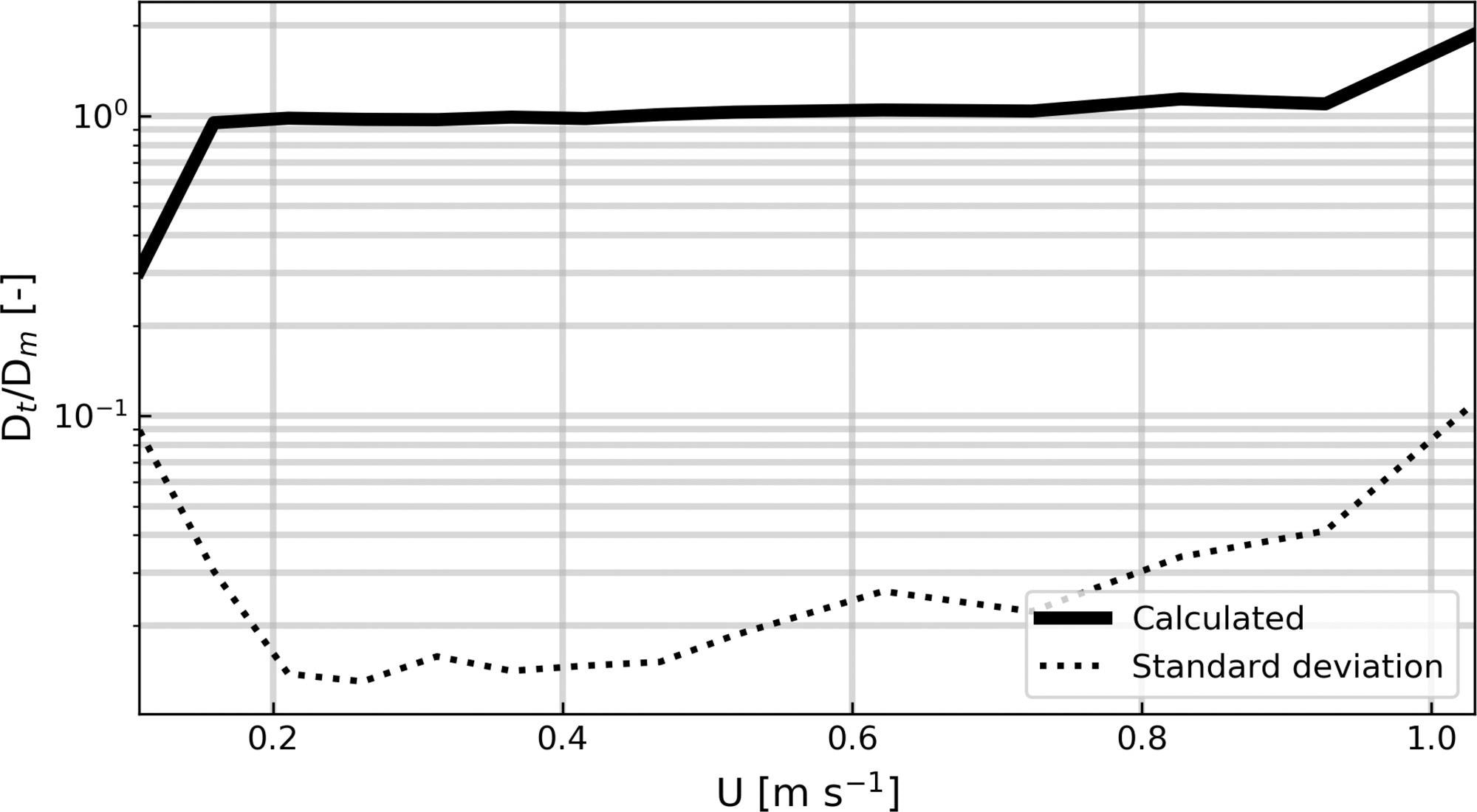
Validation of the measurement of the molecular diffusion coefficient in an empty column. Values were averaged over 340 positions along the axial coordinate, and the standard deviation was calculated from this data. Image Credit: Rousseau, L.R.S et al., ACS Engineering Au
The novel method employed in the research features an infrared source and a column. Tracer gas, which absorbs infrared radiation, is fed through the column. A configured infrared camera is used to visualize the flow of gas through the catalyst’s structure. A significant advantage of this novel method over conventional techniques is the single-measurement determination of the entire concentration field.
Twenty-two logpile structures were assessed in the study with various configurations. Assessment results indicated that staggered logpile structures possess a significantly higher transverse dispersion that can be tailored by changing the catalyst’s characteristics, such as porosity and feature size. These structures, due to their tunability and other properties, have a broader range of operation than their straight-structured counterparts.
In addition, the authors correlated the dispersion behavior of the materials with their geometry and operating conditions. This correlation and the results of the study’s analysis will aid future catalyst design. The authors have noted that further analysis and modeling will be required to investigate and understand the influence of structural parameters and provide a fundamental explanation of phenomena.
Further Reading
Rousseau, L.R.S et al. (2022) Experimental Quantification of Gas Dispersion in 3D-Printed Logpile Structures Using a Noninvasive Infrared Transmission Technique ACS Engineering Au [online] pubs.acs.org. Available at: https://pubs.acs.org/doi/10.1021/acsengineeringau.1c00040
Disclaimer: The views expressed here are those of the author expressed in their private capacity and do not necessarily represent the views of AZoM.com Limited T/A AZoNetwork the owner and operator of this website. This disclaimer forms part of the Terms and conditions of use of this website.