Researchers from Chalmers University of Technology in Sweden and Gebze Technical University in Turkey have investigated the oxidation of 3D printed IN625. Their findings have been published in a new paper in the journal Corrosion Science.
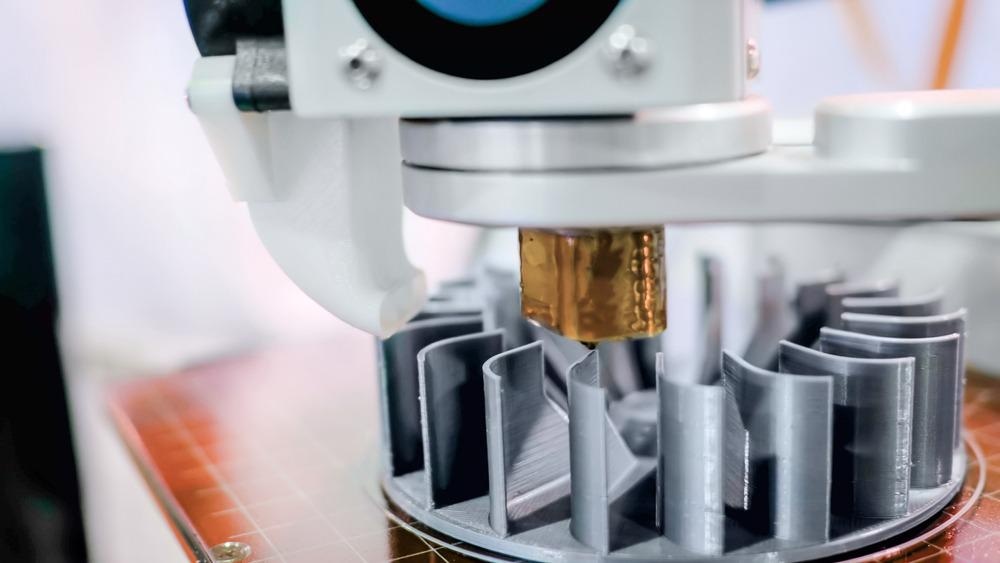
Study: High-temperature oxidation behavior of additively manufactured IN625: effect of microstructure and grain size. Image Credit: Zyabich/Shutterstock.com
Designing Materials for High-Temperature and Corrosion-Resistant Applications
Several industries including offshore power generation, the aerospace industry, and manufacturing require materials that can withstand elevated temperatures and corrosive environments. As well as possessing superior corrosion resistance, materials for applications such as jet engines, furnace linings, and stationary gas turbines must possess good creep strength.
Nickel-based superalloys have proven to be superior candidates for these materials, outperforming other high-temperature and high-entropy alloys, alumina-forming austenites, and cobalt-based superalloys. The ability of these superalloys to form external protective layers of Cr2O3 or Al2o3 oxide scales on component outer surfaces gives them superior oxidation and corrosion resistance.
AM IN 625: additively manufactured cube (a), schematic of sample cuts (b). Image Credit: Chyrkin, A et al., Corrosion Science
IN625
IN625 (Inconel 625) is a wrought nickel-based alloy that was developed in the 1960s. First used as a high-strength material for steam-line piping, further modifications to IN625 improved its weldability and creep resistance. These modifications led to the development of IN718, which is the most widely used nickel-based alloy in the aerospace industry.
IN625 is manufactured by alloying nickel with molybdenum, chromium, and niobium, producing a metal with an optimal combination of corrosion and creep resistance. This alloy can withstand a vast temperature range from cryogenic temperatures to around 1000 oC.
Fabricating Nickel-Based Superalloys with Additive Manufacturing
Additive manufacturing has been explored in recent years to produce nickel-based superalloys. Compared to traditional manufacturing methods, additive manufacturing, otherwise known as 3D printing, offers significant benefits for material fabrication, including freeform design, reduced processing and post-processing steps, cost-effectiveness, and reduced waste materials.
Powder bed fusion is a subset of additive manufacturing. These methods employ a laser (selective laser melting) or electron beam (electron beam melting) to melt and fuse powders in a powder bed system.
Selective laser melting does not need the use of vacuum, giving it a major advantage over electron beam melting. Furthermore, this technique is more versatile as more materials can be selected, it has high cooling rates, allows easy powder removal, provides a better surface finish, and most importantly, is better at producing a fine-grained microstructure in printed materials.
There are two key features of additive manufacturing alloy printing: directional solidification and rapid cooling rates. Several parameters can affect the printed alloy’s end properties, including beam size, the laser energy density, scanning speed, and powder characteristics such as morphology, particle size distribution, and purity. Layer thickness can vary between 20 and 100 µm.
The additive manufacturing process significantly influences the microstructure of alloys. Nevertheless, studies have discovered several similarities between IN625 alloys produced with either selective laser melting or electron beam melting.
In recent years, there has been considerable research effort to categorize the influence of microstructure on the oxidation behavior of nickel-based alloys at elevated temperatures. Researchers generally agree that oxidation is more rapid in additively manufactured alloys compared to their conventionally manufactured counterparts.
Research has also indicated that structural anisotropy does not significantly affect oxidation kinetics. Moreover, the origin of higher corrosion in these alloys is not well understood. Currently, there are significant research gaps in the field of additively manufactured nickel-based alloys.
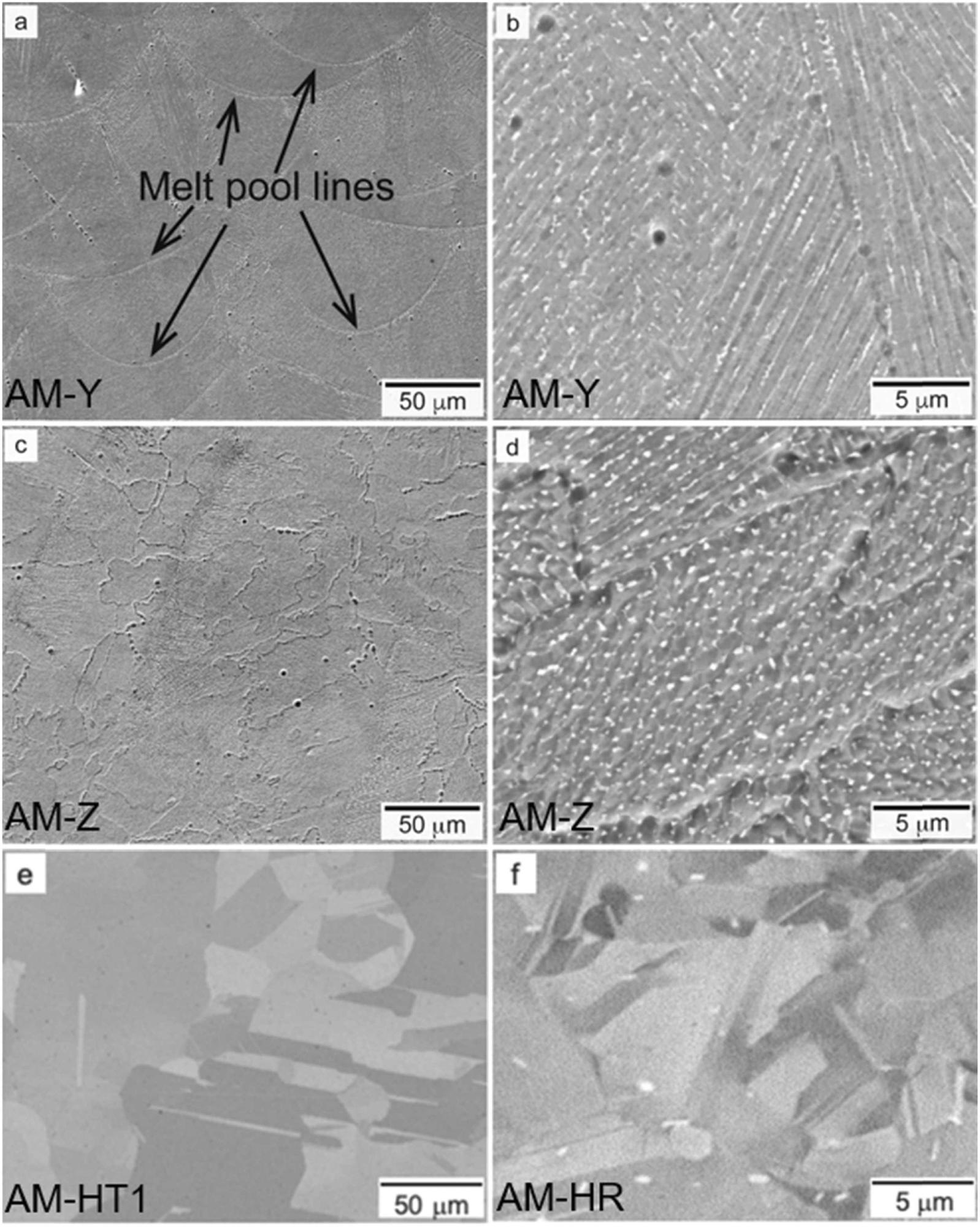
SE images of AM IN 625, Y-cut (a,b) and Z-cut. (c,d), AM-HT1 (e), AM-HR (f). Image Credit: Chyrkin, A et al., Corrosion Science
The Study
There exists a fundamental question on oxidation behavior in 3D printed nickel-based alloys. The question is whether the differences are caused by specific additively manufactured microstructures or does the manufacturing process itself produce minor deviations in the printed alloy's chemical composition.
To help answer this fundamental question, the authors have aimed to elucidate the microstructure’s role in the oxidation behavior of IN625 manufactured with selective laser melting. The specific role of texture and grain size was explored in the research.
The selective laser melting-manufactured IN625 was compared with the same alloy which was subjected to hot-rolling, hot-forged, and heat-treatment processes. This was to retain the original chemical composition of the material but change its grain structure to investigate the effect of the alloy’s microstructure.
Study Findings
Several key findings were published in the paper. Firstly, the authors demonstrated that intergranular oxidation morphology was not affected by manipulating the microstructure. Secondly, oxidation kinetics in the printed IN625 was more rapid than conventionally manufactured alloys at elevated temperatures of 900-1000 oC.
Whilst various heat treatments and hot-rolling affects, to some extent, the alloy’s overall oxidation kinetics, the principal oxidation morphology was independent of the grain size. The authors concluded that the oxidation behavior of additively manufactured alloys was more likely due to minor differences in alloy chemistry. Severe intergranular oxidation seems to play a key role in the higher oxidation kinetics of additively manufactured nickel-based alloys.
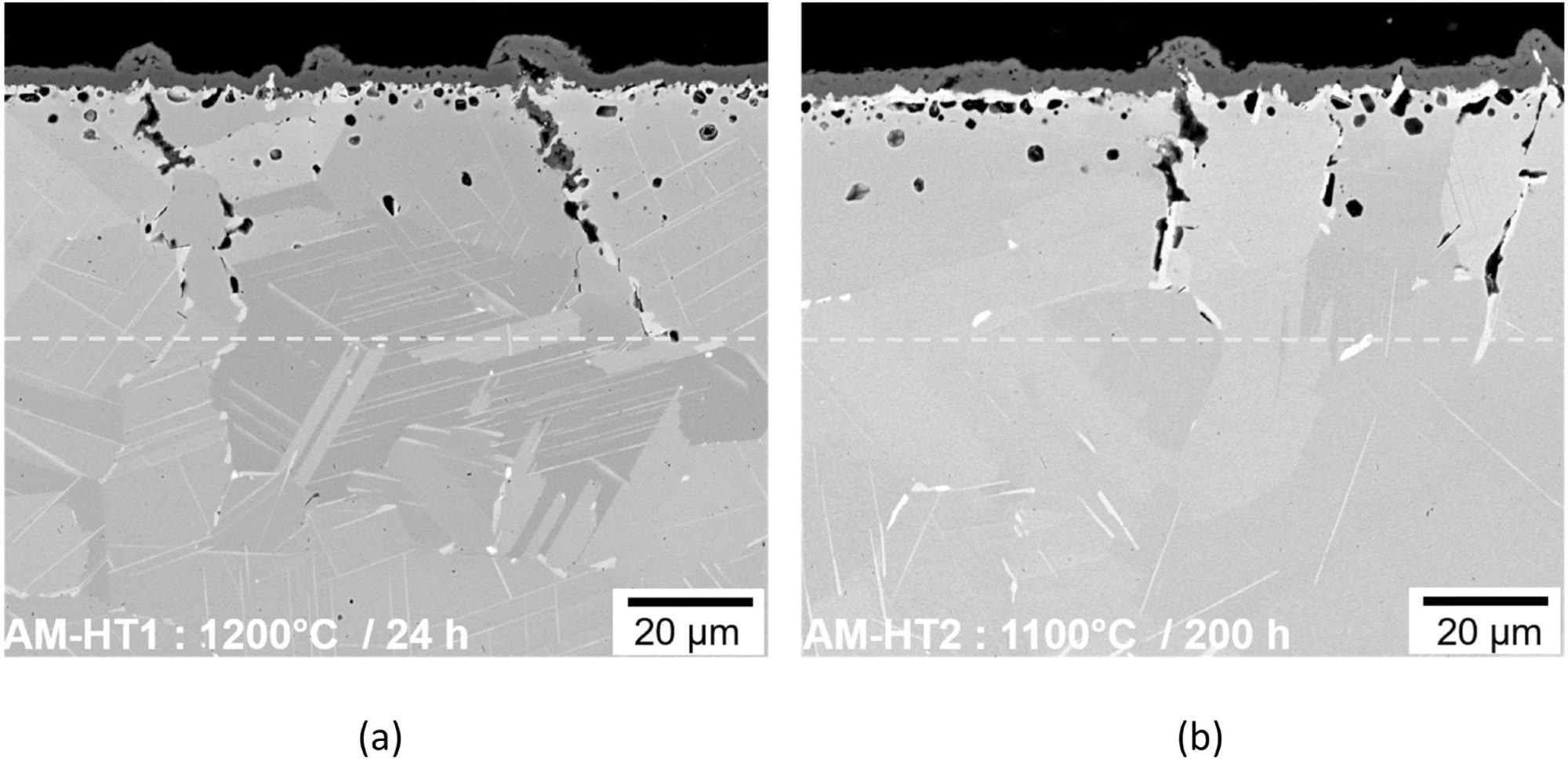
BSE images of oxide scales on heat-treated AM IN 625 after 168 h of air oxidation at 900 °C: (a) AM-HT1 (annealed for 24 h at 1200 °C) (b) AM-HT2: (annealed for 200 h at 1100 °C). Image Credit: Chyrkin, A et al., Corrosion Science
The study has provided an important contribution to the field of additive manufacturing for high-temperature and corrosion-resistant alloys. By categorizing the effect of microstructure on the alloy’s oxidation kinetics and behavior, the authors have provided information that will help researchers answer fundamental questions about materials and processes and guide future research in this field.
Further Reading
Chyrkin, A et al. (2022) High-temperature oxidation behavior of additively manufactured IN625: effect of microstructure and grain size Corrosion Science 110382 [online, pre-proof] sciencedirect.com. Available at: https://www.sciencedirect.com/science/article/pii/S0010938X22003006?via%3Dihub
Disclaimer: The views expressed here are those of the author expressed in their private capacity and do not necessarily represent the views of AZoM.com Limited T/A AZoNetwork the owner and operator of this website. This disclaimer forms part of the Terms and conditions of use of this website.