By Surbhi JainReviewed by Susha Cheriyedath, M.Sc.May 23 2022
In an article recently published in the journal Additive Manufacturing, researchers discussed the on-the-fly metrology of volumetric additive manufacturing.
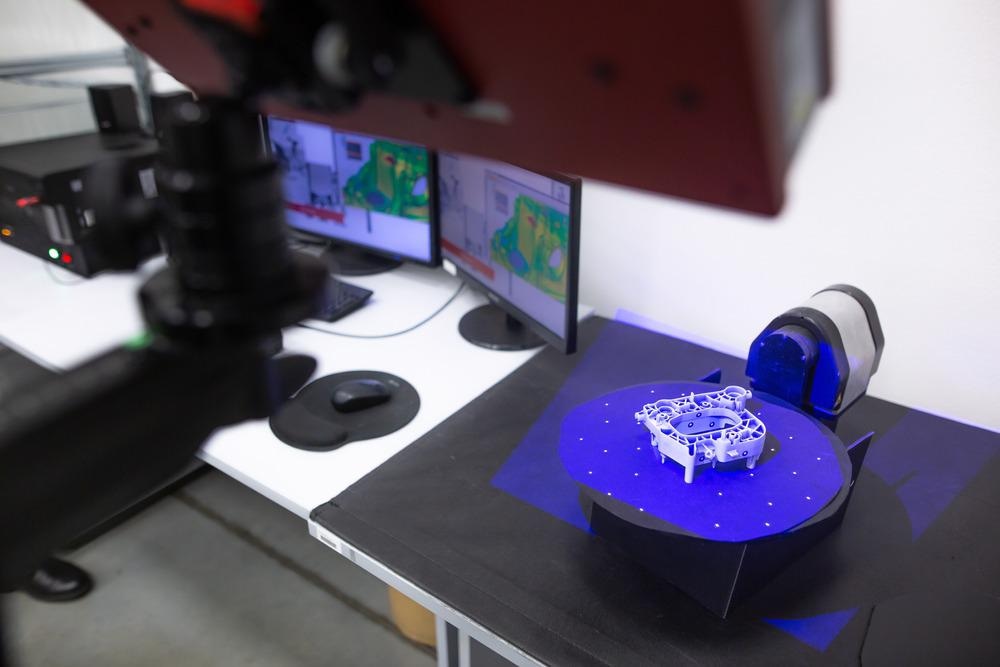
Study: On-the-fly 3D metrology of volumetric additive manufacturing. Image Credit: Simon Kadula/Shutterstock.com
Background
Recent advances in volumetric additive manufacturing (VAM) have shifted the additive manufacturing (AM) paradigm. VAM techniques enable quick 3D printing of all the layers simultaneously, rather than progressively building up items layer by layer. Tomographic VAM is currently the most extensively used VAM method.
While VAM has facilitated the AM speed to new heights, the necessity for rapid print metrology and inspection remains a major barrier across all AM modalities. In situ AM metrology is now restricted to evaluating local material properties. There is currently no device that can accurately assess the geometry of a complete object during or after printing.
VAM stands to benefit in particular, notwithstanding the need for real-time geometry monitoring across all AM approaches. To deal with VAM's exposure time sensitivity, the best exposure time must be determined. Despite the fact that this practical issue is rarely highlighted in VAM literature, it precludes reproducible and accurate printing outcomes.
About the Study
In this study, the authors discussed fully simultaneous 3D metrology and printing. For real-time 3D imaging, a photo-resin's substantial increase in light scattering during gelation was incorporated. During tomographic volumetric additive manufacturing, prints were imaged. The light scattering density in the build volume was imaged to produce quantitative, artifact-free 3D + time models of cured items that were accurate to within 1% of the print size.
The team presented an optical imaging approach for the real-time 3D mapping of the curing process in AM. The dramatic increase in light scattering caused by a resin during gelation was used to discriminate between cured and uncured print volume regions.
High contrast projection images of the print were obtained by monitoring the scattering light intensity within the volume built in a darkfield configuration. In the proposed optical scattering tomography (OST), side-scattered light from the volume of the print was scanned as it spun to form a sinogram of every layer of the object and allowed tomographic reconstruction.
The researchers showed 4D imaging of complicated tomographic prints and compared the OST imaging findings to the reference print geometry.
Observations
The scattering density that corresponded to gelation could be reliably calibrated, which resulted in print reconstruction being accurate to within 1% of the print size. It was discovered that even complex objects like the gyroid could be tomographically reconstructed using OST. The OST imaging system greatly accelerated the ability to obtain successful print parameters over a wide range of print geometries and resins.
The cured monomer was highly scattering and bright, while the uncured monomer was black. The rotating build volume allowed for simultaneous tomographic dose projection and tomographic imaging. The real-time nature of OST print imaging also enabled the user to pinpoint the source of print errors. OST also removed the trial and error associated with discovering new print times.
It was observed that OST allowed the operator to accommodate for changes in printing speed caused by temperature fluctuations and when recycling resin. OST could be used to study photopolymerization kinetics in addition to being an important tool for end-user printer operation.
The darkfield imaging of scattered light during the gelation process was a significant component of the proposed metrology approach. This optical configuration was useful in tomographic VAM, but it could also be employed in other AM approaches.
Conclusions
In conclusion, this study introduced the OST imaging modality, which allowed for live 3D imaging of the tomographic VAM process. As an optical contrast mechanism, OST exploited scattering caused by a micro-scale refractive index difference between liquid monomer and solid polymer. Although weak internal scattering occurred during VAM printing, it was usually reduced during post-curing when the cured object achieved a homogenous refractive index, resulting in prints with good internal clarity.
Rayleigh scattering theory captured the approximate dependency of the OST scattering signal on the refractive index mismatch. The dimensional accuracies and root-mean-square errors (RMSE) of experimental OST-derived 3D models and reference geometries were often less than or equal to the OST voxel size of 0.155 mm or around 1% of the size of the print. This result suggested that the proposed tomographic print system achieved a state-of-the-art and novel VAM print fidelity.
The authors believe that easy-to-use spatial-temporal metrology, such as that offered by OST, will be crucial in improving the fidelity of tomographic VAM while also making it more accessible to end-users. They also mentioned that the findings of this study lay the way for next-generation fast prototyping with real-time fault identification and correction by including form measurement in the printing process.
More from AZoM: Applications of Synchrotron-Based X-Ray Fluorescence Microscopy
Disclaimer: The views expressed here are those of the author expressed in their private capacity and do not necessarily represent the views of AZoM.com Limited T/A AZoNetwork the owner and operator of this website. This disclaimer forms part of the Terms and conditions of use of this website.
Source:
Orth, A., Sampson, K. L., Zhang, Y., et al. On-the-fly 3D metrology of volumetric additive manufacturing. Additive Manufacturing 102869 (2022). https://www.sciencedirect.com/science/article/abs/pii/S2214860422002688