A team of scientists from France has reported the development of a novel additive manufacturing approach for the production of YAG (yttrium aluminum garnet) ceramics in a one-step process. The paper has appeared in the journal Nature Scientific Reports, and the proposed method has implications for the design of improved components for the space industry as well as other high-performance industrial demands.
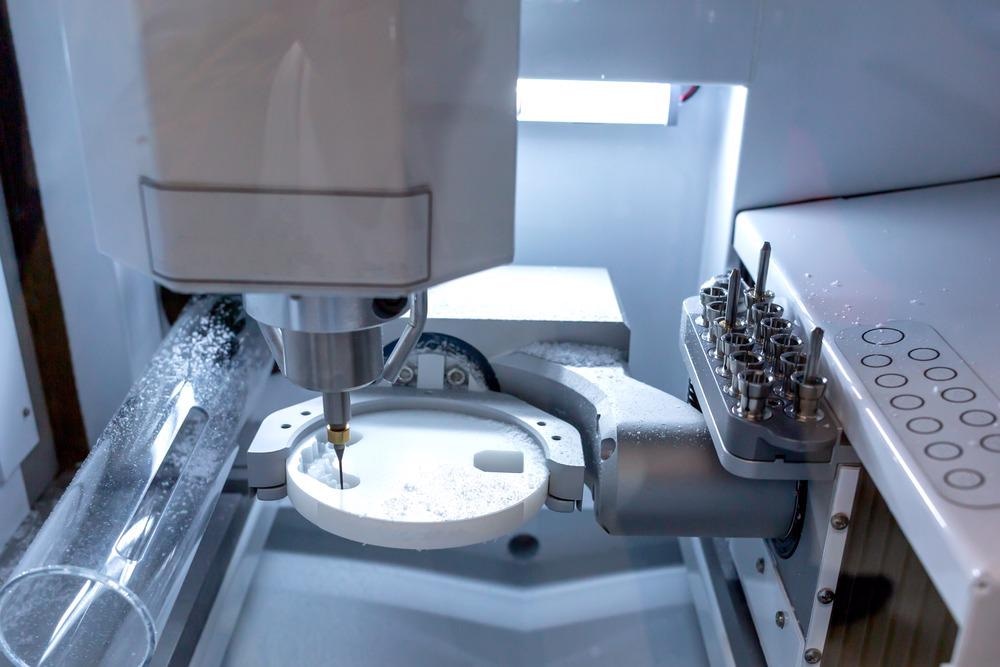
Study: Synthesis and robocasting of YAG xerogel: one-step conversion of ceramics. Image Credit: ANDRIY B/Shutterstock.com
Using Ceramics for Spaceship Design
Space exploration is a hot-button topic currently in science and the media. To make space exploration feasible, selecting materials that can withstand the rigors of outer space and the physical demands of components is essential. Propulsion systems are central elements of spaceship design, and there are limitations placed on their performance metal alloy’s resistance, which governs temperature limits for components such as turbines.
In recent years, research has focused on the development of oxide ceramics, which perform better than the traditional metal alloys employed in propulsion systems and subsystem designs. Incorporating these ceramic materials into systems can increase cycle temperatures and therefore overall efficiency of these crucial design elements. Ceramics that can withstand high-temperature creep could significantly improve the lifetime of engines and propulsion systems.
Preparation protocol for L and SP xerogels. Image Credit: Flores-Martinez, N et al., Nature Scientific Reports
YAG Ceramics
YAG ceramics have been proposed for this application by researchers in recent years. This material has been widely employed in lasers, and its mechanical properties make it an ideal candidate for high-performance applications.
YAG ceramics possess good high-temperature properties due to their superior creep behavior, high strength, chemical and physical stability, and corrosion resistance. Furthermore, it can be used as a thermal barrier coating and in applications that require long-term performance under extreme conditions.
Manufacturing YAG Ceramics and Xerogels
Sol-gel manufacturing methods are the most reliable YAG ceramic fabrication routes due to chemical uniformity being improved by homogenous precursor mixing. Moreover, lower processing temperatures are advantageous for the fabrication of these materials. Several studies have reported the successful synthesis of YAG ceramics using sol-gel methods.
Manufacturing and shaping powders that retain beneficial ceramic properties are central to the performance of the final product. Extrusion-based 3D printing methods have been explored in a few studies recently due to their ease of use and low cost. Most innovations have been in the field of optics. Currently, many studies on YAG powders and their chemical synthesis routes are limited to the laboratory, and industrial scaling is a challenging undertaking.
Scaling the manufacture and printing of YAG powders is a problematic endeavor. Impurities can form during enlarging processes, processes may not be easily reproducible, and the product’s microstructure can be altered.
Heat treatment profiles of materials and products can be improved by incorporating xerogel into ceramic pastes. Prepyrolysis steps can be avoided, and Debinding steps taken advantage of. Converting xerogel into crystalline YAG materials with additive manufacturing methods confers significant benefits for researchers.
Now, a new paper published in Nature Scientific Reports has provided a novel approach to the manufacture of these commercially important ceramics with a one-step conversion process.
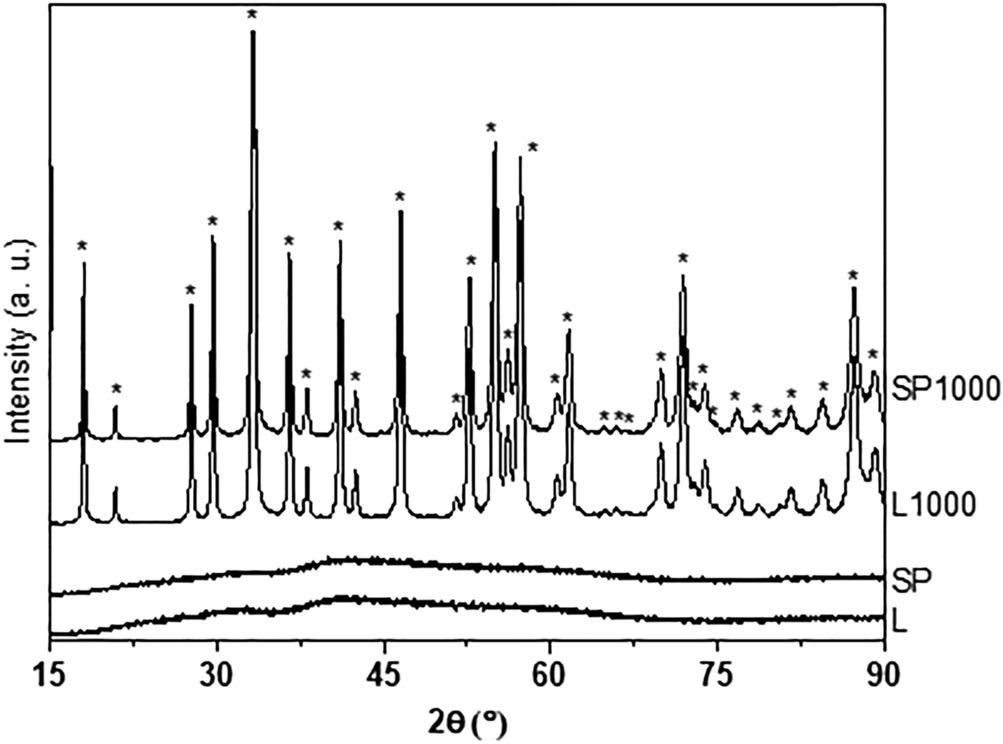
Dried (L, SP) and calcined (L1000, SP1000) YAG xerogel XRD patterns. (*) Peaks corresponding to the ICSD reference card for Y3Al5O12, PDF 04-007-2667. Image Credit: Flores-Martinez, N et al., Nature Scientific Reports
The Study
The research aim was to investigate the possibility of scaling YAG xerogel preparation. A one-step process was demonstrated, with xerogel-based pastes printed and converted to shaped YAG materials. The authors evaluated the printability of xerogel pastes. Structural, microstructural, and thermal properties were characterized in the research.
After preparation, the xerogel samples were centrifuged and dried, with subsequent calcination employed to verify the formation of the YAG phase. Organic residues were eliminated using calcination. XRD revealed that the calcined aerogels matched the structure of pure YAG without any extra phase.
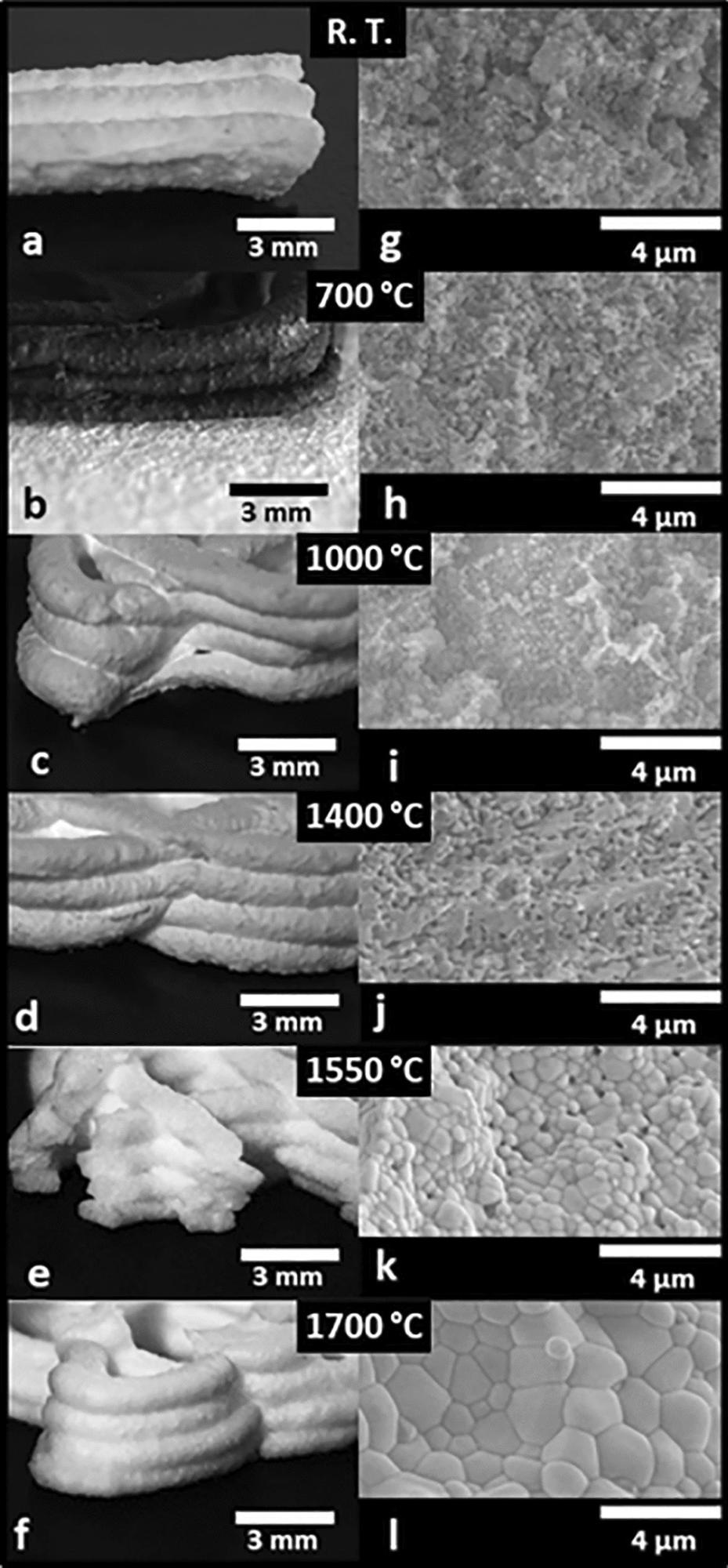
High-resolution images (a-f) and SEM micrographs (g-l) of fractured cords at different temperatures. Image Credit: Flores-Martinez, N et al., Nature Scientific Reports
The prepared xerogel paste contained few agglomerates, as evidenced by clear printing of YAG xerogel cords with no nozzle clogging. Minimal relative differences between the theoretical and experimental densities of the powders further demonstrated that the samples were close to pure YAG. Regardless of the synthesis scale, the prepared xerogels formed pure YAG ceramics.
Using the proposed approach, the authors demonstrated the formulation of direct robocast printing of xerogel pastes, with improved scaling potential compared to conventional manufacturing processes. After thermal treatments at 1550-1700 oC, it was possible to sinter the material and obtain cohesive YAG samples.
The lack of prior pyrolysis in the proposed method did not have a detrimental effect on fabrication. Moreover, the process provides a low-cost and energy-saving alternative to convention manufacturing approaches. The authors have proposed that their method is beneficial for the manufacture of turbine parts for propulsion subsystems, which can be utilized in the space industry for building exploration vessels.
Further Reading
Flores-Martinez, N et al. (2022) Synthesis and robocasting of YAG xerogel: one-step conversion of ceramics Nature Scientific Reports 12 8454 [online] nature.com. Available at: https://www.nature.com/articles/s41598-022-12204-6
Disclaimer: The views expressed here are those of the author expressed in their private capacity and do not necessarily represent the views of AZoM.com Limited T/A AZoNetwork the owner and operator of this website. This disclaimer forms part of the Terms and conditions of use of this website.