Scientists from Turkey have investigated how to improve direct metal laser melting techniques by evaluating the feasibility of contact-free supports for overhang structures during prints. The team has published their findings in the journal Materials.
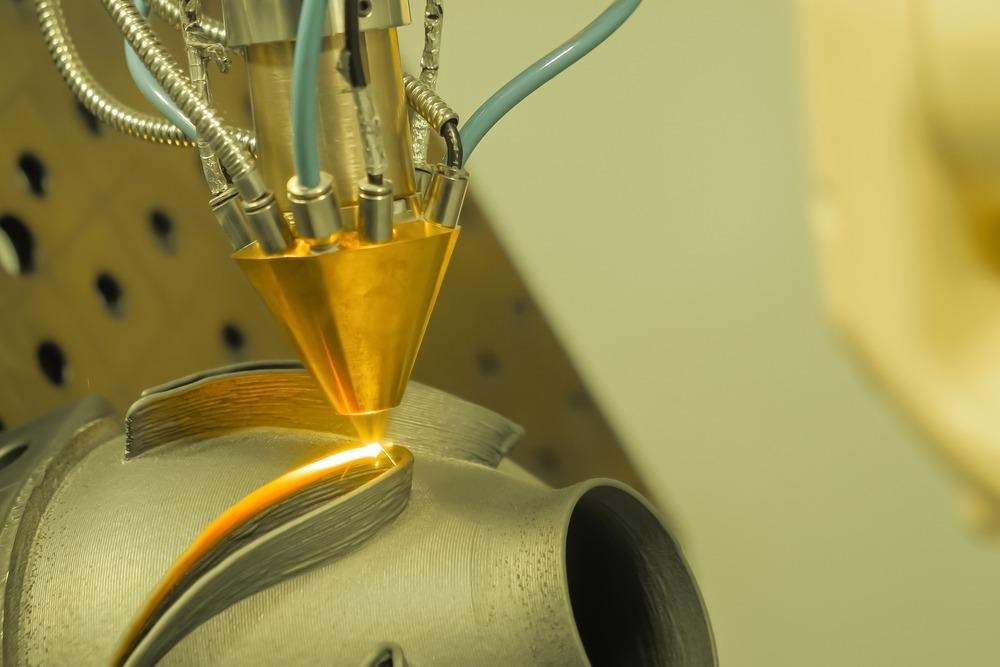
Study: Contact-Free Support Structures for the Direct Metal Laser Melting Process. Image Credit: Zyabich/Shutterstock.com
Direct Metal Laser Melting
Direct metal laser melting is a powder bed fusion technique. Like all additive manufacturing methods, direct metal laser melting offers the benefits of improved design freedom, low cost, and minimal waste and post-processing steps. Along with other powder bed fusion methods, direct metal laser melting fabricates the final product layer-by-layer in a powder bed using thermal energy.
The process starts with a CAD model of the desired product. STL data is produced from the digital model, which includes information on the desired layer thickness and laser paths. This data is then transferred to the equipment.
A layer of powder is deposited on the build plate, which is attached to the build chamber. Lasers are then used to selectively melt the powder, and subsequent layers are selectively melted and fused together to build the final product. Like all 3D printing techniques, direct metal laser melting possesses significant benefits over conventional methods.
Representative sample design. Image Credit: Çelik, A et al., Materials
This additive manufacturing method has been extensively studied in recent years for printing products from metal alloy powders. However, there are some critical issues with this process that hinders its commercial-scale applications.
Problems with Powder Bed Fusion Methods
A major problem in powder bed fusion techniques such as direct metal laser melting is the final printed product’s surface roughness, which can determine fatigue performance. Surfaces of overhang features can especially suffer from this issue. Reducing this problem is essential for producing parts with the desired quality and durability.
To overcome this issue, several conventional post-processing steps such as CNC milling and chemical milling are typically employed. However, material removal is limited by the complexity of powder bed fusion-printed parts. Moreover, problems such as internal cooling channels can occur.
Mechanisms such as powder sticking and stair-stepping determine the roughness of printed parts. Overhang surfaces of parts often exhibit severe issues due to their free-standing nature. In direct metal laser melting, the overhang problem is especially pronounced due to factors such as loose powder beds and lower preheating temperatures compared to other processes.
Supports are typically used in direct metal laser melting to support overhang features. After removal, supports can leave marks on printed parts and play a role in deteriorating surface characteristics. Due to the scale of this issue, many studies have concentrated on understanding support structure behavior and their effects on surface characteristics and minimizing their use during the design phase.
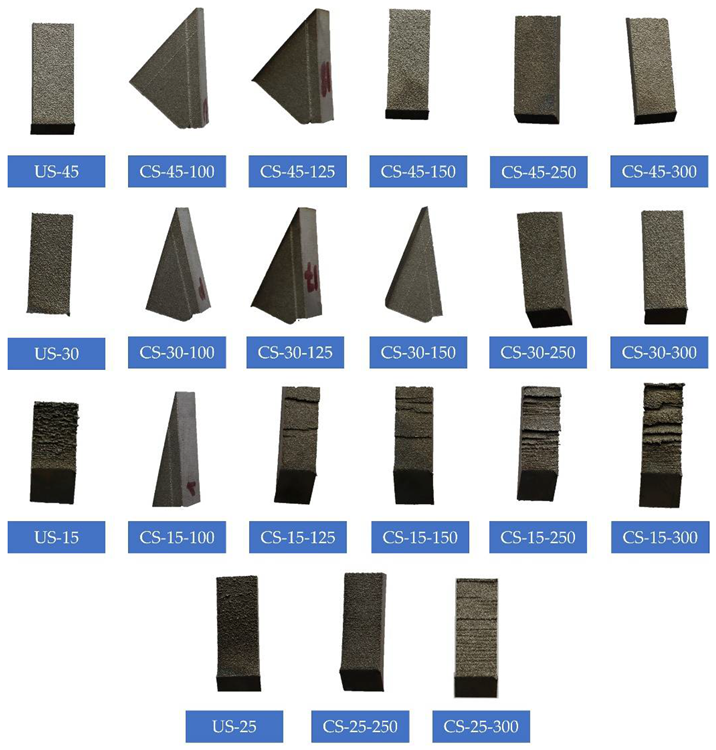
Contact-free supported geometries printed via DMLM (Coupons like pyramids are the ones that fused to support. Remaining ones represent overhang areas of corresponding coupons). Image Credit: Çelik, A et al., Materials
The Study
The new paper has investigated the use of contact-free supports for direct metal laser melting processes to improve the quality and durability of printed parts. Contact-free supports (also referred to as contactless supports) do not touch overhang surfaces but still provide heat evacuation during printing. Using these supports helps to reduce post-processing steps and associated costs.
Some studies have been conducted recently on investigating the use of contact-free supports during print processes. Whilst contact-free supports offer significant benefits for producing parts with improved surface characteristics and performance, the authors have noted that current studies are still limited in number and scope.
The authors investigated the effects of contact-free support printing on overhang features of parts produced from Cr-Co-Mo alloy powder. Contactless supports were placed under overhang features with different inclination angles from 15o to 45o and with different gap distances from 100 μm to 300 μm. Microstructural characterizations, optical microscopy, and roughness measurements were used to identify the surface and sub-surface characteristics of the printed overhang features.
The study demonstrated that, at all inclination angles, using contactless supports can help to reduce overhang surface roughness when using the correct gap distance. Setting the correct gap distance avoids the sintering of powder between supports and overhangs. Furthermore, if this distance is too large, thermal conductivity is reduced. Therefore, operators should optimize gap distance to improve the quality of print parts.
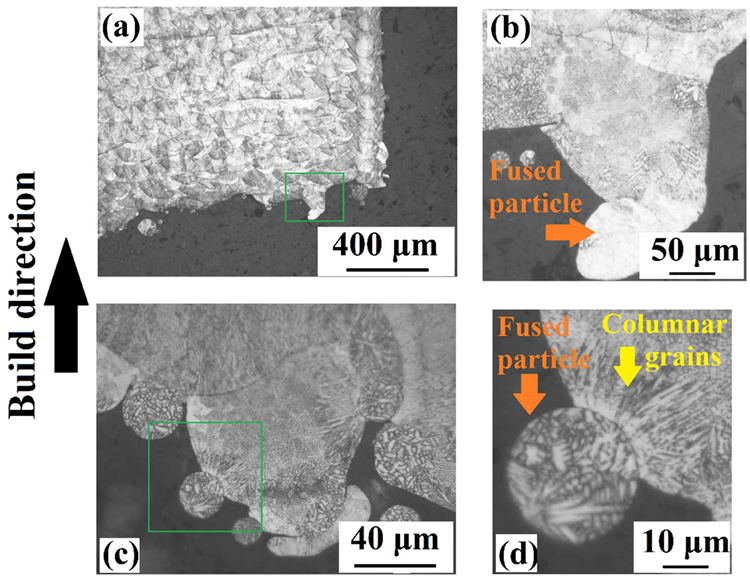
The cross-sectional OM images obtained from: (a) US-30° (×50) and (b) US-30° (×200), (c) US-45° (×1000) and (d) US-45° (×2000). Image Credit: Çelik, A et al., Materials
In Summary
The paper has demonstrated the suitability of contact-free supports for printing parts with direct metal laser melting methods. By optimizing gap distance, the fusion of printed parts is avoided whilst maintaining higher thermal conductivity. The use of contact-free supports significantly reduces surface roughness defects, fatigue properties, and therefore print quality and durability of parts.
Further Reading
Çelik, A et al. (2022) Contact-Free Support Structures for the Direct Metal Laser Melting Process Materials 15(11) 3765 [online] mdpi.com. Available at: https://www.mdpi.com/1996-1944/15/11/3765
Disclaimer: The views expressed here are those of the author expressed in their private capacity and do not necessarily represent the views of AZoM.com Limited T/A AZoNetwork the owner and operator of this website. This disclaimer forms part of the Terms and conditions of use of this website.