A paper recently published in the journal Energies has evaluated the thermal properties of three-dimensional (3D)-printed walls.
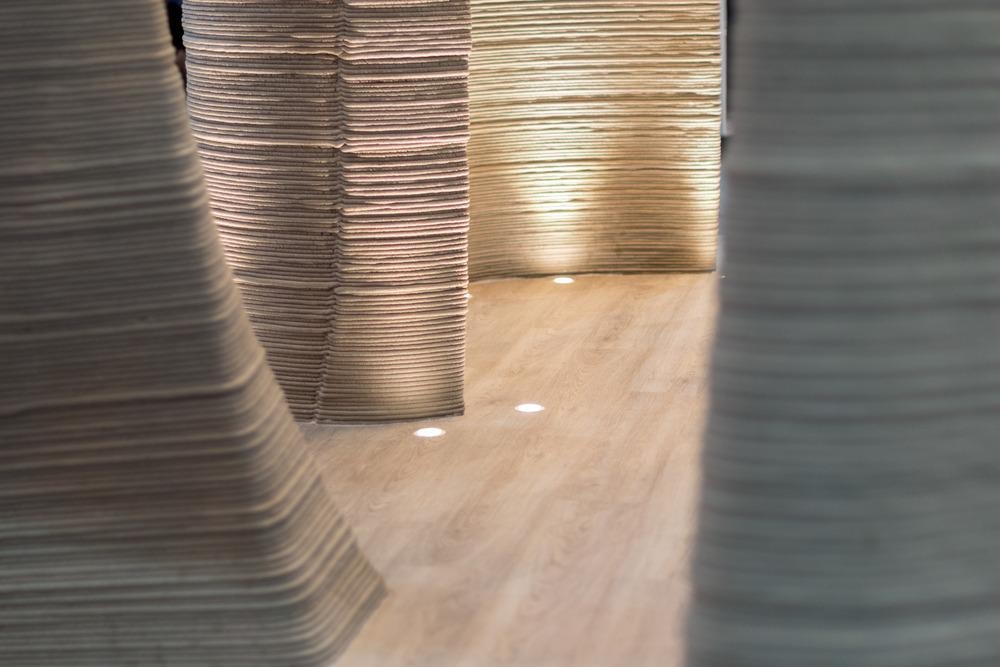
Study: Experimental Study on the Thermal Performance of 3D-Printed Enclosing Structures. Image Credit: Kraipet Sritong/Shutterstock.com
Background
Additive manufacturing or 3D printing, characterized by a low-cost and fast building process, is increasingly gaining prominence in the construction industry. Additive manufacturing has become a common technique to create entire devices or parts, as it allows for rapid prototyping and on-demand manufacturing.
The integration of 3D printed concrete (3DPC) technology with a modular building system can provide sustainable solutions to the current construction challenges. 3DPC technology can increase thermal comfort and decrease energy consumption in a room when integrated and hybridized with other energy-efficient technologies.
Topology optimization can be used to adjust the 3DPC thermal resistance characteristics. For instance, cavities can be introduced in areas requiring low thermal conductivity to improve the insulation properties. However, assessing the energy efficiency and topology optimization of the enclosed structures is necessary using numerical modeling.
Types of enclosing structures. Image Credit: Nemova, D et al., Energies
The Study
In this study, researchers investigated the energy efficiency and suitability of 3D-printed enclosing structures and determined the optimal configuration to obtain enclosing structures with the most suitable thermal characteristics. The thermal resistance coefficient of 3D printed structures was evaluated. A mathematical model was created to describe the mass and heat transfer process, and the proposed model was validated by comparing the model with experimental results.
Mathematical modeling can determine the heat transfer resistance as it can accurately estimate integral characteristics, such as average surface heat flux, compared to an experiment where these values are determined only at monitoring points.
Multiple enclosed structures were selected for the numerical study. The internal structure of cavities of these structures differed from each other. However, all structures were similar in terms of form factor. The linear dimensions were the same for all structures, excluding the structure depth.
The selection of the 3D-printed enclosed structure/additive wall panel for the physical experiment was based on the preliminary numerical studies. The test equipment used in the physical experiment setup to investigate the thermal properties of the additive wall panel included climatic chamber number one, climatic chamber number two, and a temperature and flux density meter. In the climatic chamber number one, the supported temperature range was from −70 °C to +100 °C, while in the climatic chamber number two, the temperature range was from −70 °C to +180 °C.
The size of the 3D-printed wall panel was 390 mm × 680 mm × 310 mm, and the thickness of the structure was 35 mm. A dry mix was utilized for additive manufacturing of the panel. The maximum aggregate fraction size in the dry mix was 0.63 mm. Overall, 1800 kg of the dry mix was used to prepare the one m3 structure, and 0.13–0.16 L of water was required to mix one kg of dry mix.
The mixture was used after hardening. The compressive strength and bending tensile strength of the hardened mixture after 24 h were 18 MPa and 4 MPa, respectively, and after 28 days were 40 MPa and 8 MPa, respectively. The elasticity modulus was 26 GPa. The prepared panel can be applied in all climatic zones.
The size of the wall panel was smaller than the inner part of the climatic chamber, and the remaining space of the chamber was filled hermetically with insulation. The temperatures of the chamber one and two were set at −24 °C (Tcold) and +22 °C (Thot), respectively. The temperature and heat flux density meters were programmed to measure and record the values of temperature and heat flow every 15 min during the day.
The ANSYS CFX software package, a computation fluid dynamics (CFD) program, was employed to assess the heat convection and conduction in the 3D-printed block enclosing structures. The Boussinesq approximation was utilized to describe the airflow in laminar formulation, while the Newton–Richmann law was used to describe the convective temperature on the outer boundaries of the blocks.
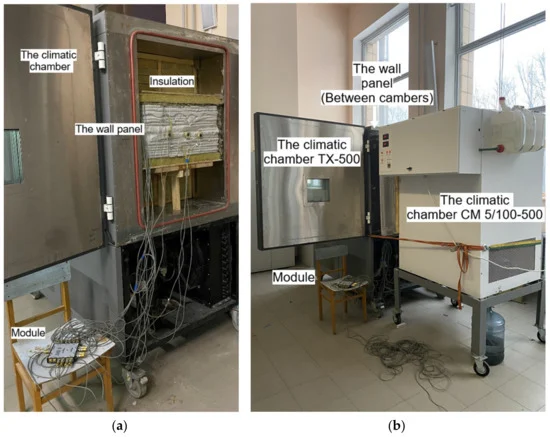
Stand with the additive wall panel. (a) The sample is placed in a climate chamber No. 1.; (b) The sample is placed between two climatic chambers, the start of testing. Image Credit: Nemova, D et al., Energies
Observations
The study analyzed the most common 3D-printed enclosing structures and new enclosing structures. The heat fluxes and temperature outside and inside a 3D-printed structure were measured in climatic chambers for the first time. Energy modeling of a building with 3D-printed enclosing structures with various construction configurations was also conducted successfully.
In the physical experiment, the cold chamber temperature Tcold was dialed in less than 40 min from the start. In the first 120 min, a precipitate drop in the temperature was observed at the sides of the structure/additive wall panel with 0-35 mm thickness, while a significant reduction in temperature was observed inside the structure with 185-255 mm thickness. After 120 min, the time interval was more than two hours for the comparing isotherms.
The CFD modeling of the experimental structure showed that the air was hotter in the upper part of the structure compared to the concrete lintel in the middle part, while the air was colder in the lower part compared to the middle part. The difference in local temperature between air and concrete was 15 oC.
Additionally, the temperature isoline becomes more curved while moving from the cold or hot side to the center of the structure. The temperature difference between the upper and lower sides in the center of the structure’s side face was 5 oC.
Moreover, the heat flux through the air parts was significantly lower compared to the solid parts of the structure. The convection also influenced the surface heat flux distribution as the heat flux changed from 100 to 70 W/m2 along the vertical coordinate when the temperature gradients changed due to convection.
Three cold rectangular cavities, two hot triangle cavities, and one rectangular cavity were observed in the structure. All cavities, excluding the small triangle cavitie,s led to stabilizing effects on the concrete temperature, with notable differences in air temperature present only in the boundary layers. The average heat flux through the U-value of the construction was 1.18.
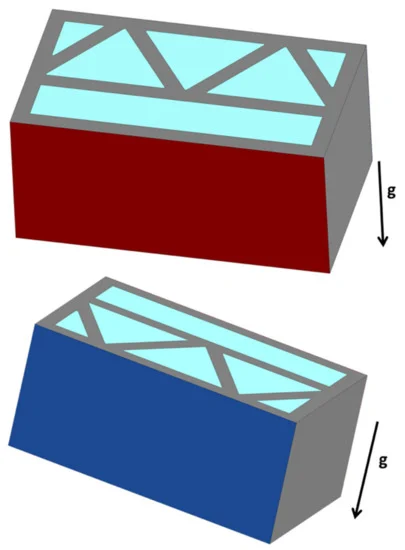
Boundary conditions by colors and gravity direction. Image Credit: Nemova, D et al., Energies
The CFD simulations of the 3D-printed enclosing structures with various configurations demonstrated that some heat resistance can be added due to the convection in the enclosed structures compared to the empirical approach. Moreover, the influence of convection was stronger on more uneven cavern distributions. Thus, empirical formulas were unsuitable for engineering purposes for structures with insulation as they provided lower U-values.
The energy consumption of a 3D-printed building composed of additive enclosing structures with various construction configurations was between 3026 and 8536 kWh per year.
Thermal imaging of the 3D-printed enclosing structure displayed surface irregularities, leading to thermal inhomogeneity. More research is required on inhomogeneities to properly determine the thermophysical properties of the structures.
To summarize, the findings of this study effectively demonstrated the thermal performance of 3D-printed enclosing structures.
Disclaimer: The views expressed here are those of the author expressed in their private capacity and do not necessarily represent the views of AZoM.com Limited T/A AZoNetwork the owner and operator of this website. This disclaimer forms part of the Terms and conditions of use of this website.
Source:
Nemova, D., Kotov, E., Andreeva, D. et al. Experimental Study on the Thermal Performance of 3D-Printed Enclosing Structures. Energies 2022. https://www.mdpi.com/1996-1073/15/12/4230