By Surbhi JainReviewed by Susha Cheriyedath, M.Sc.Jun 23 2022
In an article recently published in the open-access journal Materials, researchers discussed the preparation and characterization of wood rigid polyurethane composites.
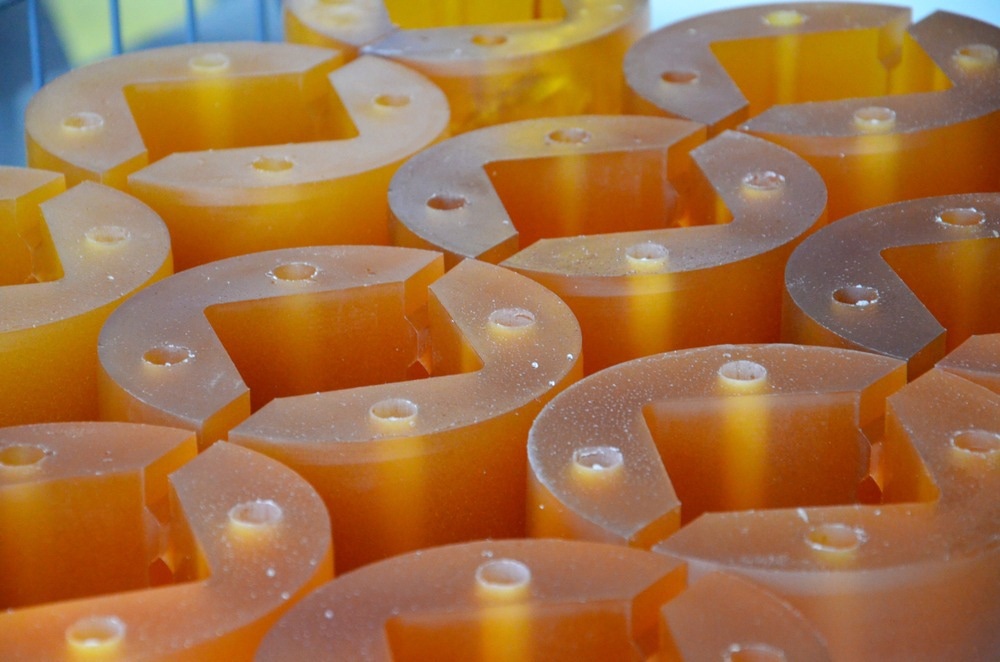
Study: Synthesis and Characterization of Wood Rigid Polyurethane Composites. Image Credit: Valentina Dudnichenko/Shutterstock.com
Background
Wood is one of Canada’s most valuable natural resources, and a significant amount of waste is produced through the use of this resource. For each of the residue categories, there are particular valorization routes, primarily for bioenergy uses. Wood chips are typically employed in the production of pulp and paper. However, due to their poor wettability and detrimental impact on pulp production and paper characteristics, needle-shaped shavings and sawdust are underutilized.
The decline in paper, pulp, and cardboard producers is another indicator of the crisis the paper sector is going through. Since 2010, the manufacturing of wood chips has continued to be a concern for sawmills that are unable to find customers, which lowers the price and revenue. Finding new markets is crucial for valorizing wood chips. Adding natural fibers to polymeric matrices, particularly wood chips, is becoming more popular. Indeed, earlier research has shown that using them can be advantageous from an economic and ecological standpoint.
Compressive strength and dimensional stability were improved by adding cellulose nanocrystals to polyurethane foams made from palm oil. For optimum compressive strength and improved thermal insulation, stiff polyurethane was reinforced with wheat straw lignin. It has also been demonstrated that lignin works well in place of polyol. A high percentage of components from bio-sourced sources must be introduced before bio-based goods may be widely used. This objective might be accomplished by using lignocellulosic fibers to reinforce foams.
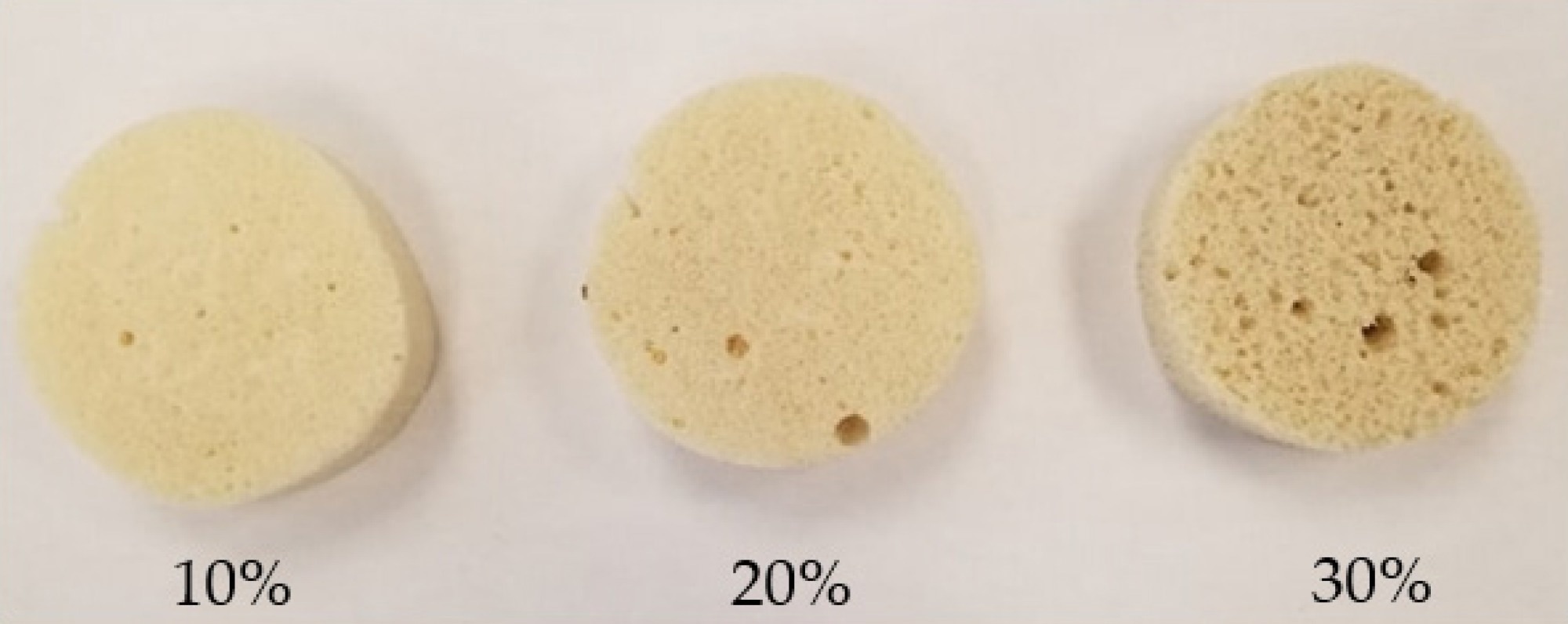
Numerical image of mechanically mixed foams with fine fiber at 10, 20, and 30%. Image Credit: Bradai, H et al., Materials
About the Study
In this study, the authors discussed the utility of different wood particles as reinforcement in rigid polyurethane foams (RPUFs). Milled wood particles of various shapes and sizes, as well as commercial polyol and isocyanate, were used to make reinforced rigid polyurethane foams. The impact of fiber treatments and mechanical stirring on the characteristics of foams was also investigated. Additional tests were carried out on polyisocyanurate foams (PIR) to see how reinforcing affected their characteristics. The impact of wood particle reinforcement on the foam was investigated by measuring mechanical characteristics.
The team revealed the interaction between the wood fibers and the matrix using confocal microscopy and Fourier-transform infrared spectroscopy (FTIR). Wood fibers from milled wood chips having various sizes and a commercial polyurethane formulation were used to make polyurethane biocomposites utilizing a mechanical and manual approach.
The researchers looked at the fibers' ability to reinforce a polyisocyanurate foam and the effect of acetylation on the processing and characteristics of RPUF biocomposites. The usage of wood particles in polyurethane composites was used for turning wood leftovers and by-products into more profitable bioproducts than bioenergy. Understanding the interfacial adhesion between the polyurethane matrix and the wood fiber was also aided by fiber with significant morphological and chemical differences.
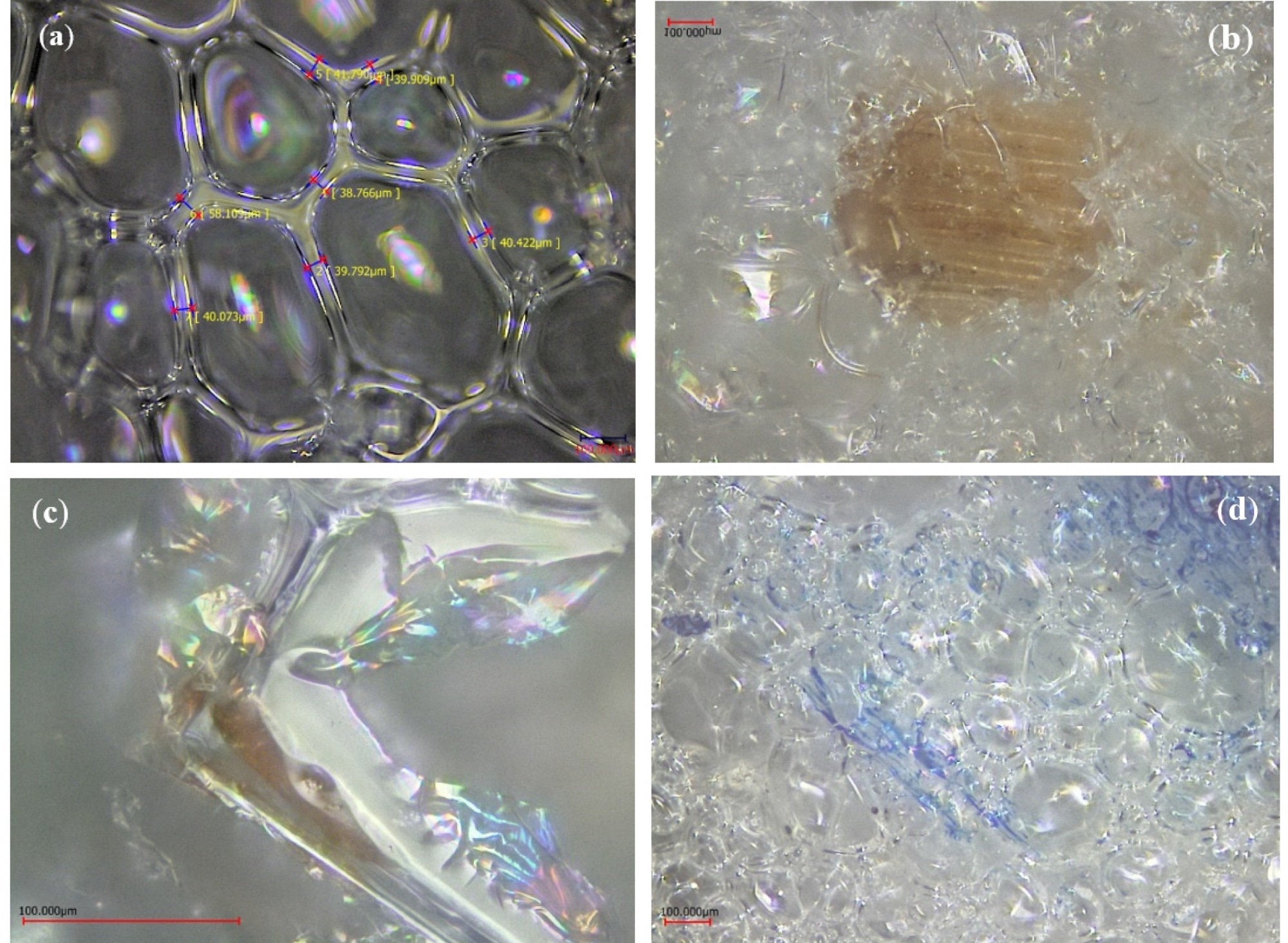
Cell morphology and fiber/matrix interaction: (a) Neat foam, (b) PUR-05, (c,d) PUR-01. Image Credit: Bradai, H et al., Materials
Observations
The thermal conductivity of PIR_01/05-10 foams increased by 16%, from 0.147 W/mK for PIR0 to 0.171 W/m.K for PIR_05-10. PIR_05-10 had a compressive strength of 439 kPa, up from 230 kPa for PIR0. A 10% increase in reinforcement resulted in a large rise in density. The greatest substantial rise was seen in PIR_05-10, which increased by more than 50% from 41 kg/m3 in PIR0 to 62 kg/m3 in PIR 05-10. The compressive strength declined with an increase in the percentage of reinforcement in PUM MC foams, with a 15% fall between PUM_MC-10 and PUM_MC-30, notwithstanding density fluctuation. Foam with kraft fibers (PUM_KR) had the highest density at reinforcement rates of 10 and 20 php.
As the percentage of reinforcement increased, the compressive strength (Rc) of PUR_01 foams decreased. As a matter of fact, Rc decreased from 103 kPa for PUR_01-10 to 83 kPa for PUR_01-30. For a percentage of 20%, which equals almost 120 kPa, this grain size exhibited the best resilience. This denoted the formulation's greatest achieved compressive strength. For PUR_03-30, however, this resistance diminished until it reached 104 kPa. For PUM_01-30, the density of the foam was 103 kg/m3, while for PUM_03-30 it was 81 kg/m3. PUM_01-10 had a maximum compressive strength of 400 kPa, while PU_01-10 had a maximum compressive strength of 120 kPa.
Despite some fiber attachment, the hard-wood fibers pierced most of the cell walls of RPUFs, which explained the drop in compressive strength of the composites for manually mixed foams. Mechanical stirring was found to be a successful way to increase the reinforcing strength of untreated fibers. When untreated wood flour was added to the mix, the characteristics of RPUF foams changed in a similar way, which increased compressive strength considerably.
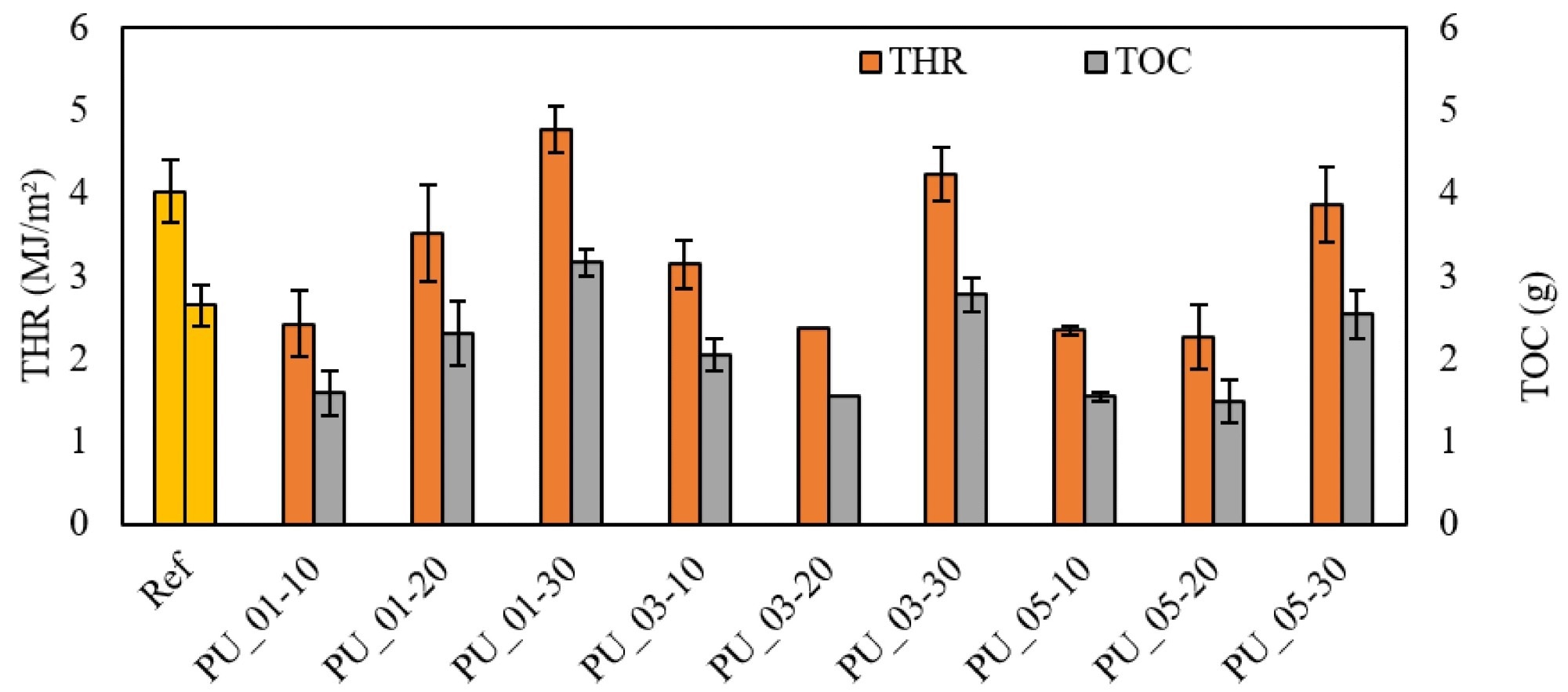
Effect of particle size and percentage on the total heat release and total oxygen consumption. Image Credit: Bradai, H et al., Materials
Conclusions
In conclusion, this study elucidated the development of RPUFs of various filler types and sizes. The addition of fillers validated the interaction of wood fibers with isocyanate as well as their adherence to the matrix. Coarse particles were shown to be ineffective in reinforcing RPUFs. Furthermore, when compared to hand stirring, mechanical steering improved compressive strength. The fiber treatments could not improve the foam's mechanical capabilities, which was mostly due to the aggregation of treated fibers, which resulted in abnormalities in the foam's three-dimensional structure.
Wood fibers increased the compressive strength of both polyisocyanurate and polyurethane foams when added at 10 php. Wood fibers increased the thermal conductivity, thermal stability, and fire retardancy of the foams by a little amount.
Disclaimer: The views expressed here are those of the author expressed in their private capacity and do not necessarily represent the views of AZoM.com Limited T/A AZoNetwork the owner and operator of this website. This disclaimer forms part of the Terms and conditions of use of this website.
Source:
Bradai, H., Koubaa, A., Bouafif, H., et al. Synthesis and Characterization of Wood Rigid Polyurethane Composites. Materials 15(12) 4316 (2022). https://www.mdpi.com/1996-1944/15/12/4316