A paper recently published in the journal Additive Manufacturing discussed the laser powder-bed-fusion (LPBF) additive manufacturing (AM) technique for three-dimensional (3D) printing of high-quality molybdenum (Mo) components.
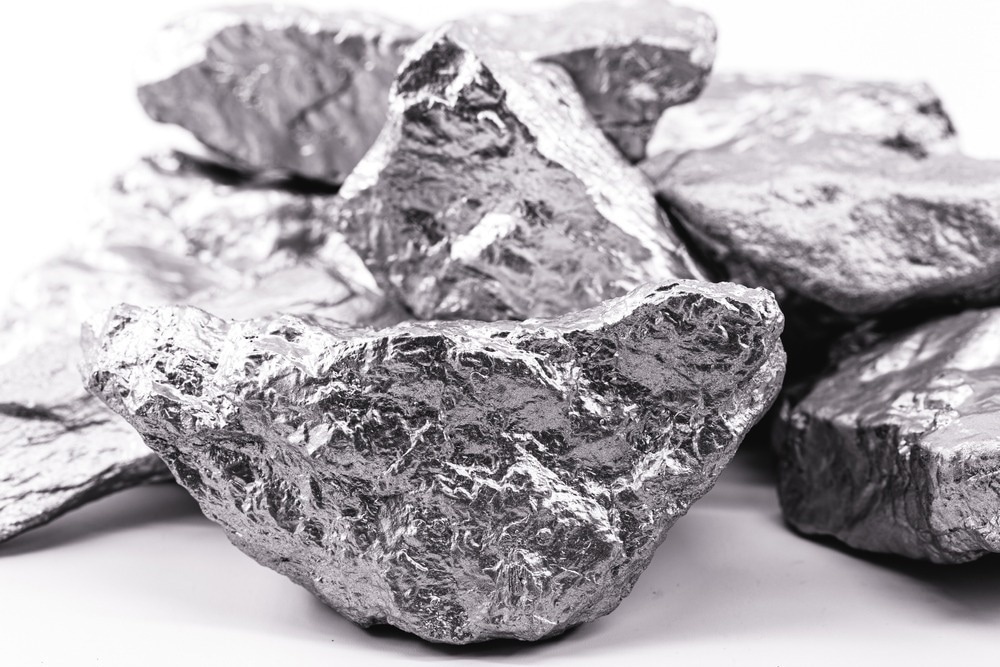
Study: Powder-bed-fusion additive manufacturing of molybdenum: process simulation, optimization, and property prediction. Image Credit: RHJPhtotos/Shutterstock.com
Background
Mo, a refractory rare metal, has gained considerable attention for different applications in industry due to its extremely high melting point, robust thermal and electrical conductivity, low thermal expansion coefficient, good corrosion resistance, and superior high-temperature strength.
However, the manufacturing of Mo using the traditional methods, specifically powder metallurgy (PM), is difficult due to the formation of defects as the metal has poor high-temperature oxidation resistance and low-temperature brittleness. AM can be used to overcome the limitations of PM to manufacture Mo components with complex structures and geometries.
Among the different AM techniques, LPBF is a proven AM technique commonly used to manufacture net-shape parts/components with complicated geometry through alternative powder spreading (PS) and selective laser melting (SLM). PS and the subsequent SLM play a critical role in determining the structure/size precision and the mechanical properties of the printed Mo components.
Several physical and numerical studies were performed to improve the final printed products' properties and quality and spread powder bed. However, obtaining the correct dynamic information in-situ from the physical experiments, specifically the underlying mechanisms and dynamics, has been difficult, which restricted the further development of the LPBF technique.
Computer simulations can overcome the limitations of physical experiments as the simulations can reproduce both PS and SLM processes and solve the identified problems from a particulate scale. Thus, several defects such as cracks, deformation, pores, and balling phenomena that occur in the LPBF process due to the inherent properties of Mo can be solved using computer simulations to obtain a high-quality final product.
Previous studies have specifically focused on the effects of SLM process parameters to obtain Mo samples with fewer cracks and high density. However, fewer studies were performed to systematically evaluate the properties and structure of the powder bed of Mo with continuous size distribution (CSD).
Moreover, the relationship between the molten track performance and powder bed quality also must be identified and understood. A machine learning (ML) approach based on the obtained numerical simulation results can be used to predict the molten track and powder bed properties required for quality/process evaluation and intelligent control of production in the future.
The Study
In this study, the entire LPBF AM process of Mo material was numerically reproduced using coupled discrete element model (DEM) and computational fluid dynamics (CFD) model to systematically investigate the PS and SLM of Mo powder with CSD in the AM process.
Initially, the parameters of the Mo powder with CSD utilized in the actual LPBF AM process, including coefficients of rolling friction, coefficients of sliding friction, coefficients of restitution, and surface energy, were calibrated and then fed into the DEM model for parametric study on powder spreading.
Parameters including spreading velocity and gap height were used for powder spreading simulations. Systematic numerical simulations were performed on the Mo powder spreading to determine the effects of operating parameters on the micro- and macroscopic properties of the powder beds. The process was optimized, and corresponding dynamics/mechanisms were analyzed within this duration.
Subsequently, the SLM of the spread powder beds with various structures was simulated using the CFD model to understand the relationship between molten track performance and powder bed quality. Both DEM and CFD models were validated to ensure their reliability and effectiveness.
Finally, a back propagation neural network (BPNN) model was developed based on the data obtained from CFD and DEM simulations to predict and evaluate the molten track property and powder bed quality to create a process map for optimal operations.
Observations
The coefficient of rolling friction, coefficient of sliding friction, coefficient of restitution, and surface energy of Mo powder obtained after calibration from both numerical simulations and physical experiments were 0.022, 0.324, 0.532, and 0.0597 mJ/m2, respectively.
The quality of the powder bed was closely related to the gap height and spreading velocity. For instance, the surface quality and packing density of the powder bed decreased and the pore size increased corresponding with the increasing spreading velocity or decreasing gap height.
This phenomenon was attributed to the greater inertial motion of particles due to the higher spreading velocity and low probability of particles passing through the gap between the substrate and blade caused by the blocking behavior of the force chains.
Thus, a powder bed with a smooth surface and high packing density can be obtained by properly controlling the gap height and spreading velocity in the range of 2.5 D - 3.5 D and 0.05 m/s - 0.1 m/s, respectively.
In the LPBF AM process, no positive correlation was observed between the powder bed packing density and molten track performance due to the formation of defects such as porosity and balling caused by the over-thickness of the powder bed. Thus, the highest possible packing density of a suitable powder bed must be within the bed thickness threshold.
The BPNN model trained using the data obtained from CFD/DEM simulations accurately predicted the molten track performance and powder bed quality and developed a reasonable map for the proper selection of operating parameters in real processes.
To summarize, the findings of this study provided several crucial references for manufacturing high-quality Mo components using the LPBF AM process.
More from AZoM: ICP-MS for Trace Metal Analysis
Disclaimer: The views expressed here are those of the author expressed in their private capacity and do not necessarily represent the views of AZoM.com Limited T/A AZoNetwork the owner and operator of this website. This disclaimer forms part of the Terms and conditions of use of this website.
Source:
Wu, Y., Fu, H., Zou, Q. et al. Powder-bed-fusion additive manufacturing of molybdenum: process simulation, optimization, and property prediction. Additive Manufacturing 2022. https://www.sciencedirect.com/science/article/pii/S2214860422004614?via%3Dihub