A paper recently published in the journal Additive Manufacturing demonstrated the feasibility of printing three-dimensional (3D) porous carbon structures using partially dehydrated whey as a precursor.
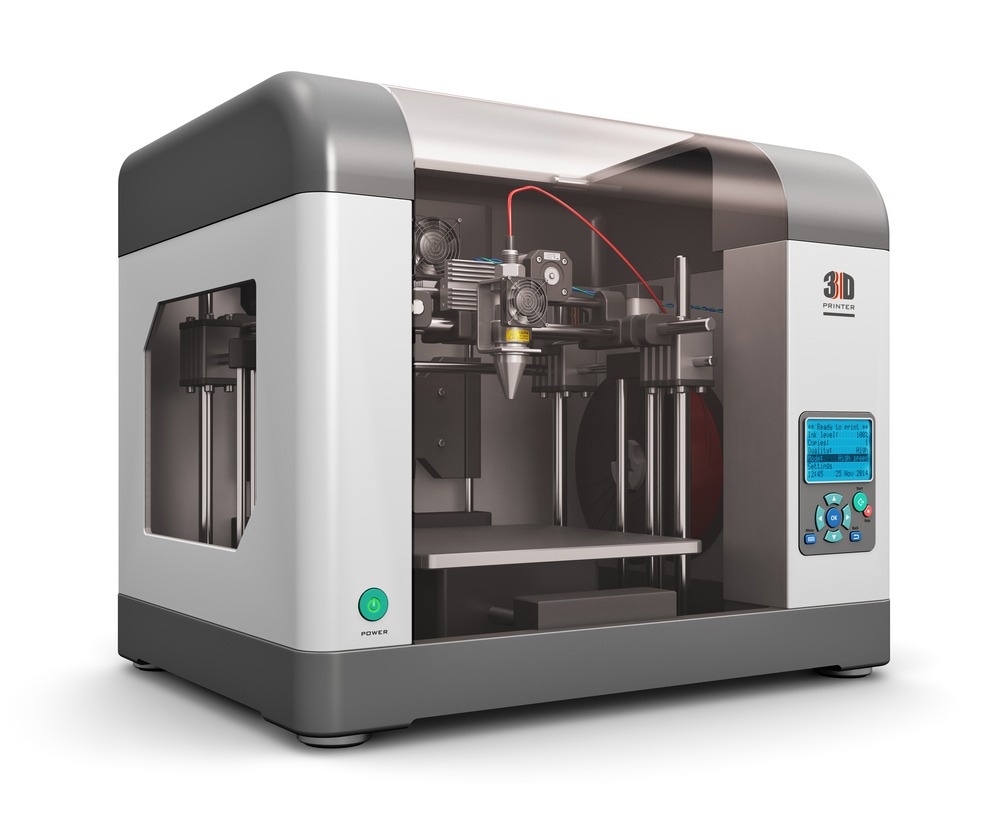
Study: From whey robocasting to custom 3D porous carbons. Image Credit: Oleksiy Mark/Shutterstock.com
Background
Additive manufacturing (AM)/3D printing technologies have been used recently to produce activated carbons. However, most of the porous carbon precursors printed using these techniques are thermoplastic materials that often lose their shape after carbonization.
Although several strategies have been used to overcome this challenge, most of them involve using sophisticated precursors and complicated methods. Thus, researchers proposed a simpler method to synthesize 3D porous carbons in this study using partially dehydrated whey as the carbon precursor. Whey, a sustainable natural product, is produced annually in substantial amounts by the dairy industry across the world.
3D printable inks or pastes can be obtained easily using whey, and the pastes can be used effectively in extrusion-based AM techniques, such as robocasting. Subsequently, the 3D-printed whey structures can be transformed into porous carbon through simple carbonization without losing their original shape.
The Study
In this study, researchers investigated the feasibility of using partially hydrated whey to print various porous carbon structures such as prisms or cylinders with lattice patterned fillings using the robocasting technique. Later, they investigated the properties of the printed carbon structures.
A modified CERAMBOT Pro printer with a 20 Ga plastic nozzle was used to print different 3D porous carbon structures. Pronterface software was used for printing control, while the Fusion 360 and PrusaSlicer were employed for designing and slicing the 3D pieces, respectively.
The layer height for all layers and the printing speed were maintained at 0.6 mm and 20 mm/s, respectively. Additionally, the structures were printed at 20-22 oC without using additional heating devices. The ink/paste was prepared by hand-mixing various proportions of distilled water and whey powders.
A Haake MARS II rotational rheometer with a 20 mm rotary plate over a fixed parallel base was employed to evaluate the paste rheology. Viscoelastic parameters, such as loss modulus, complex viscosity, phase angle, and storage modulus, were determined by performing small amplitude oscillatory shear (SAOS) tests.
The whey structures were dried for 24 h at 60 oC after printing and then cured by initially heating for six h at 150 oC in a lab oven and then up to 250 oC at one oC/min heating rate. Subsequently, the cured specimens were carbonized within a 90 mm ceramic reactor under 100 ml nitrogen/min gas flow at 850 oC at 10 oC/min heating rate with 1.5 h of soaking time.
Selected carbonized specimens were demineralized using conventional washing procedures. Distilled water, hydrochloric acid, and hydrogen fluoride were used sequentially to thoroughly wash the samples for reducing their ash content, which was related to the salt content of the original whey.
Researchers performed organic elemental analysis, thermogravimetric analyses, and field emission scanning electron microscopy-energy dispersive X-ray (FESEM-EDX) analyses for the characterization of the carbonized samples.
The Dubinin-Radushkevich model and Brunauer-Emmett-Teller model were used to determine the micropore volumes and specific surface area of the samples, respectively. An Instron Model 8562 device was employed to perform the compressive tests.
Observations
Different 3D porous carbon structures were synthesized successfully using the robocasting technique, followed by a heating-based curing process and conventional carbonization. Printable pastes were obtained easily by blending water and whey powder, which behaved as a thermoset polymer upon heating.
The paste formulation containing 76 wt% of solids was selected as the best paste formulation for the 3D printer in terms of printing accuracy at room temperature. The selected formulation displayed a proper shear thinning behavior.
Moreover, the dynamic and static yield stresses of the selected whey paste confirmed its ability to flow through the printer nozzle in most robocasting devices and maintain a proper consistency to sustain successive layers vertically.
The ink demonstrated a complete recovery after moderate stresses and a very stable solid-dominating behavior after severe stresses within the linear viscoelastic region. Additionally, no changes were observed in the rheological properties of the paste/ink during the printing time.
The curing of the printed whey structures successfully preserved their initial shape before carbonization by preventing the uncontrolled emission of volatiles. However, a 23% isotropic size reduction was observed in the structures due to thermal shrinkage.
3D lattices of carbon filaments with 425 µm mesh size and 500 µm in diameter were manufactured after carbonization, which displayed the high accuracy of the AM technique in printing porous carbon structures. The absence of paste flow control in the printer used in this study did not affect the printing quality.
Carbonized 3D structures contained substantial amounts of ashes due to the high salt content of the whey precursor. However, demineralization of the structures effectively removed the ash content in the carbonized samples.
Highly porous 3D carbon structures with a maximum porosity up to 72% and specific surface areas up to 500 m2/g were obtained after the process. Moreover, the 3D structures also demonstrated good mechanical properties with relatively high compressive strengths up to 6.3 MPa.
Taken together, the findings of this study demonstrated the feasibility of using partially dehydrated whey as a carbon precursor to print different 3D porous carbon structures using the robocasting technique.
More from AZoM: How is 3D Printing Changing the Textile Industry?
Disclaimer: The views expressed here are those of the author expressed in their private capacity and do not necessarily represent the views of AZoM.com Limited T/A AZoNetwork the owner and operator of this website. This disclaimer forms part of the Terms and conditions of use of this website.
Source:
Fernández, A., Suarez, M., Llamas-Unzueta, R. et al. From whey robocasting to custom 3D porous carbons. Additive Manufacturing 2022. https://www.sciencedirect.com/science/article/pii/S2214860422004730?via%3Dihub