In a paper recently published in the journal Materials, researchers reviewed recent developments in the fabrication of thermoplastic microfluidic devices and highlighted current and rising approaches to trigger chemical and/or physical characteristics to suit real-world applications.
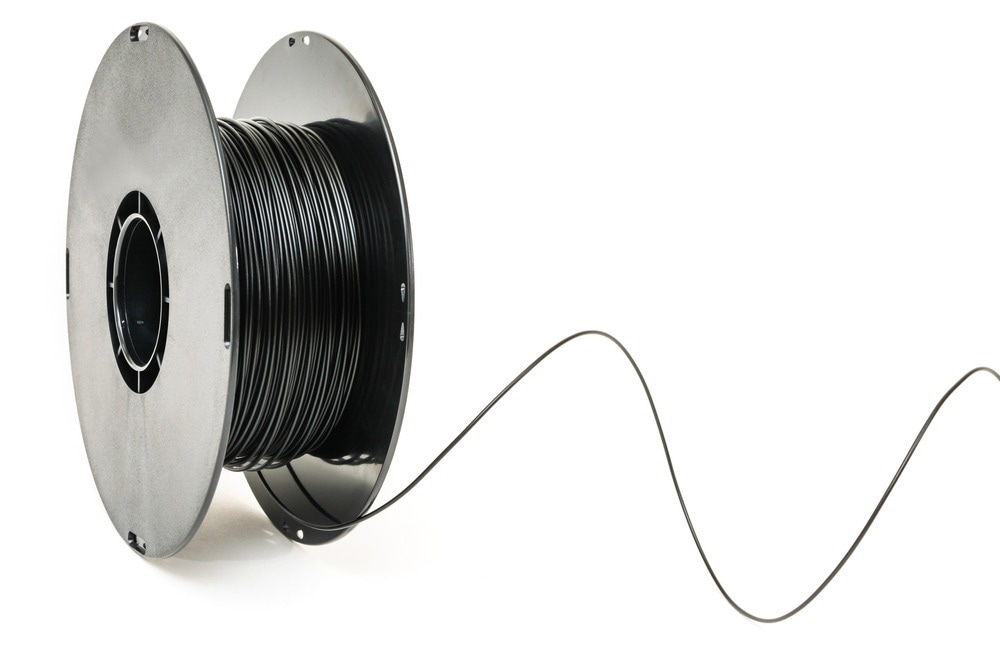
Study: The Fabrication and Bonding of Thermoplastic Microfluidics: A Review. Image Credit: HannaTor/Shutterstock.com
Background
Microfluidic systems have periodically reinvented state-of-the-art methods for high-input clinical screening, biochemical assays, fluidic automation, and a variety of other disciplines since their inception. Because of their chemical and physical versatility, polydimethylsiloxane (PDMS) and glass have been two essential choices of materials in microfluidics. However, the extensive use of PDMS and glass devices has been severely hampered by their expensive and time-consuming production method, low scalability, and considerable irregularity between devices.
On a larger scale, these devices frequently fail in high-pressure environments, rendering several post-fabrication processing procedures impractical. To that aim, considerable attention has been garnered by thermoplastic microfluidic platforms due to their inexpensive costs and superior material qualities in comparison to PDMS and glass devices. The creation of thermoplastic microfluidic platforms comprises two steps: (1) device assembly, which includes forming the microfluidic routes and attaching the layers, and (2) channel operationalization for the intended application.
Development of Microchannel Geometry
Hot embossing has been a common medium-cost method for mass manufacturing of thermoplastic polymers. The microfluidic arrays are formed as polymer cavities by heating the polymer plate above the glass transition temperature (Tg) under hydraulic pressing against a master mold with channel protrusions. Another method for developing microchannels in thermoplastics is injection molding.
This process includes the melting of the thermoplastic polymer granules followed by injection into the mold cavity. In general, injection molding and heat embossing are well-suited for medium-cost mass production via replication techniques and may be used to produce intricate channel layouts. Furthermore, the surface finish quality in these processes is better than in other techniques.
Photolithography is commonly used to create master molds for thermoplastic polymer fabrication in both injection molding and hot embossing. Laser ablation, which is suitable for several polymers including nitrocellulose, polyethylene terephthalate (PET), and Teflon, is another technique utilized to produce thermoplastic polymers featuring microfluidic channel cavities. The main disadvantages of this technique are the inability to fabricate complicated microchannel layouts and poor surface smoothness.
Because of its short production cycle time, additive manufacturing has gathered significant attention in microfluidics. The 3D printed microchannels' resolution and the mechanical and optical qualities, however, are not on par with other methods. The ability of 3D printing to construct 3D objects in one step having detailed and complicated features with lesser space requirements using a digital model is a significant advantage. Despite the recognition, it still shows shortcomings when employed in microfluidics, such as poor bonding with the layers lacking structural integrity. This is because the extruded material hardens immediately, and the neighboring layers do not bond well.
Bonding Techniques
Thermal fusion bonding, chemical bonding, and solvent bonding are the most documented strategies for permanently fusing thermoplastic polymers and preparing enclosed microfluidic devices. Thermal fusion involves heating the polymeric layers over their Tgs while pressing the layers together with a vacuum thermocompressor or a hydraulic press. This is a quick method for thermoplastic layer bonding. However, the requirement of high temperature and pressure limits the possibility of low-cost mass manufacture of microfluidic devices.
Solvent bonding involves solvent diffusion over the polymer interface, dissolving the polymer chains and mobilizing them. The compression of polymer substrates is followed by solvent evaporation. The resultant mobile chains become entangled in one another at the interface, forming a powerful bonding force.
Solvent bonding is typically incompatible with pre-functionalization because the solvent must be applied to both the bottom and the top thermoplastic layers that can remove functional groups while denaturing the restrained biomolecules. Chemical bonding, on the other hand, enables simultaneous functionalization of the inner microchannel surface since the reactive chemical groups produced for joining the two layers may also be integrated for additional covalent biomolecule bonding. Another advantage of this approach is the higher bonding strength achieved by the covalent layer bonding.
Ultrasonic vibration may also be used as a heat source, thus speeding up the bonding process significantly. This technique provides faster as well as superior bonding strength, making it an excellent approach to rapid prototyping. Laser welding is another method for thermoplastic polymer bonding. Double-sided adhesives with pressure sensitivity, such as silicone and acrylic-based tapes, have also been widely used. Furthermore, the use of PDMS as an interface glue can potentially be an option for producing an effective bonding force.
Conclusions
To summarize, the researchers reviewed and summarized the techniques to incorporate thermoplastic polymers inside microfluidic systems. According to the authors, replication methods like injection molding or hot embossing, along with fast prototyping techniques, such as laser ablation and micro-milling, provide a remarkable prospect in the production of low-cost microfluidic devices.
More from AZoM: What is the Function of Isotopic Analysis?
Disclaimer: The views expressed here are those of the author expressed in their private capacity and do not necessarily represent the views of AZoM.com Limited T/A AZoNetwork the owner and operator of this website. This disclaimer forms part of the Terms and conditions of use of this website.
Source:
Shakeri, A.; Khan, S.; Jarad, N.A.; Didar, T.F. The Fabrication and Bonding of Thermoplastic Microfluidics: A Review. Materials 2022, 15, 6478. DOI: https://doi.org/10.3390/ma15186478